Aluminum Smelting And Electrolysis
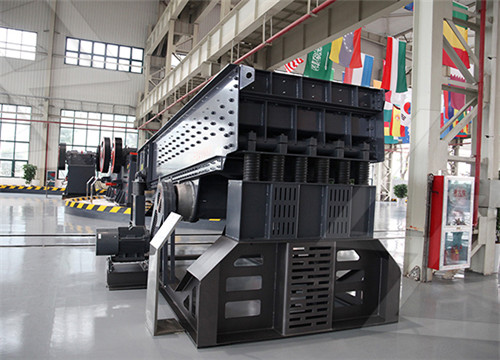
Aluminium smelting Wikipedia
OverviewLayout of an aluminium smelterPrincipleCell componentsEnvironmental issues of aluminium smeltersExample aluminium smeltersSee also
The Hall-Héroult electrolysis process is the major production route for primary aluminium. An electrolytic cell is made of a steel shell with a series of insulating linings of refractory materials. The cell consists of a brick-lined outer steel shell as a container and support. Inside the shell, cathode blocks are cemented together by ramming paste. The top lining is in contact with the molten metal and acts as the cathode. The molten electrolyte is maintained at high temperature
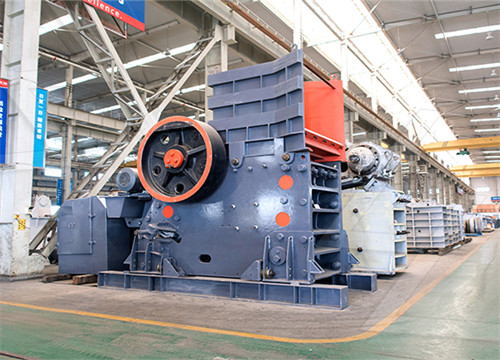
Aluminum processing Smelting Britannica
根据热度为您推荐•反馈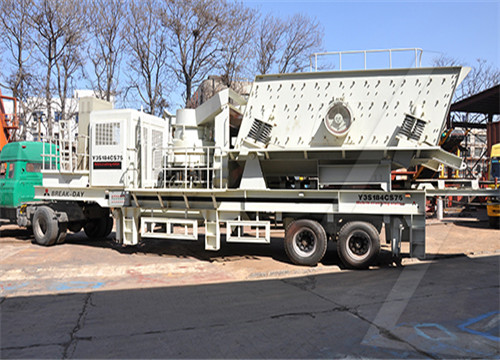
The Aluminum Smelting Process : Journal of Occupational
Inside, there are hundreds of aluminum electrolysis cells and each of them can be 10 to 15 m long. A photograph of a modern cell line is shown in Fig. 1. FIGURE 1: has far
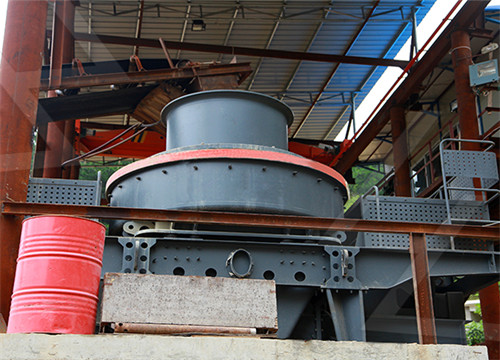
Aluminium Analysis IEA
It further announced that, as a part of its Pollution Reduction and Carbon Reduction Synergies Implementation Plan, the output of recycled aluminium will reach 11.5 Mt by 2025, and the proportion of renewable
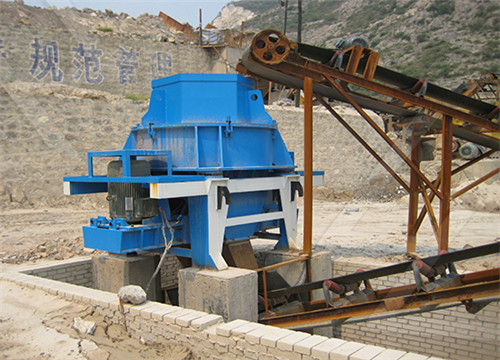
Aluminum Electrolysis an overview ScienceDirect Topics
Overall process of aluminum electrolysis is described by the following equation: (2)Al2O3 → 2Al + 1.5O2. Eq. (2) corresponds to electrolysis, in which the anode is non
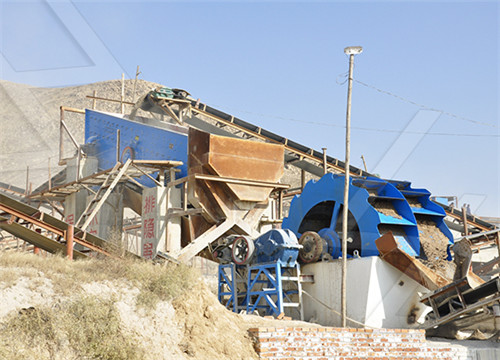
The Aluminum Smelting Process Explained HARBOR
On the industrial scale, the Hall-Héroult process of aluminum smelting requires a great deal of power, producing aluminum through electrolysis. Dissolved aluminum separates and moves to a collection area. Energy

Chapter 2. Production and Processing of Aluminum The
Throughout the world, primary aluminum is still produced by the electrolysis of alu-mina in molten fluoride salt. This is, in essence, the process that Hall and Héroult in-vented, and
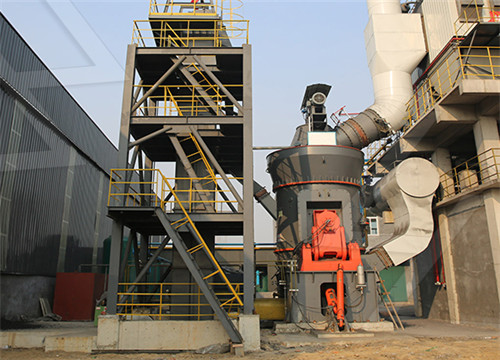
Electrolysis and extraction of aluminium BBC Bitesize
The extraction is done by electrolysis, but first the aluminium oxide must be melted so that electricity can pass through it. However, aluminium oxide has a very high melting point
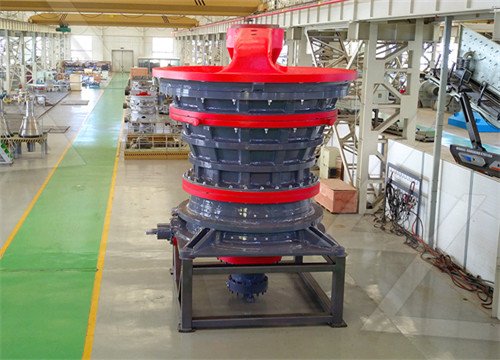
Is aluminium electrolysis using inert anodes a blind alley?
2019年4月24日The electrodes are oriented horizontally. Aluminium (Al) is formed at the cathode (in the electrochemical sense), which is the top of the molten metal. The process employs carbon (C) anodes. The anodes are
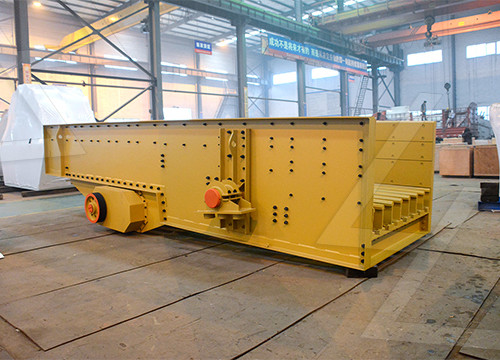
Production of Aluminum: The Hall-Héroult Process
The aluminum oxide is dissolved by the caustic soda, precipitated out of the solution, washed and heated to eliminate water. The resulting alumina is a white powder resembling sugar. Step 3: Smelting into aluminum An
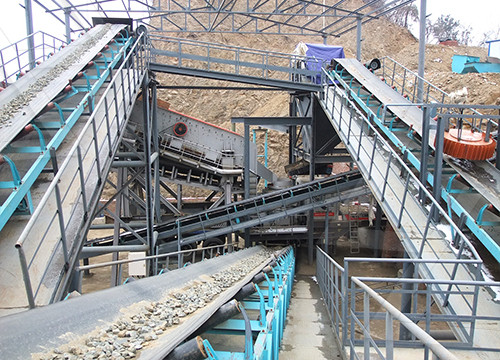
Decarbonizing Aluminum: Rolling Out a More Sustainable Sector
2022年2月25日The Hall-Heroult process of smelting the aluminum oxide to release pure aluminum comprises the second stage. By removing carbon anodes from aluminum’s electrolysis smelting reaction and replacing them with new nonreactive materials, the process would only emit oxygen as a byproduct. Though still in R&D, the
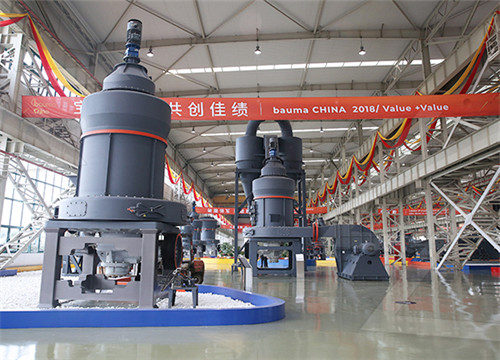
The Aluminum Smelting Process : Journal of Occupational and LWW
Inside, there are hundreds of aluminum electrolysis cells and each of them can be 10 to 15 m long. A photograph of a modern cell line is shown in Fig. 1. FIGURE 1: has far greater potential for achieving sustainability than improvements in energy efficiency within the aluminum smelting processes. Aluminum is also essential in environmental
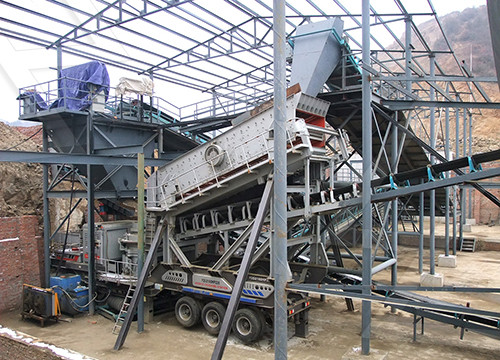
The Aluminum Smelting Process and Innovative Alternative Technologies LWW
Today, all aluminum smelters use carbon anodes in their electrolysis cells. Carbon is a reasonably good electrical conductor, and more importantly, it is able to withstand the action of the corrosive fluoride-containing molten electrolyte at about 960°C.
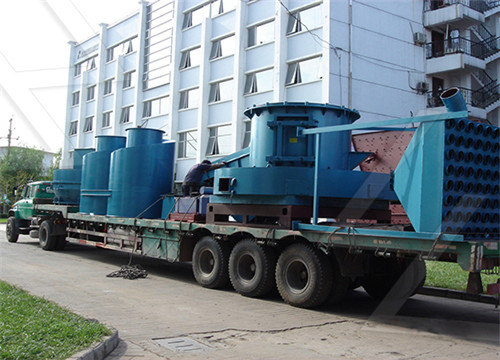
Alcoa -- ELYSIS
The name ELYSIS refers to the process at the center of aluminum smelting, the electrolysis of alumina. The technology could eliminate 6.5 million metric tons of annual greenhouse gas emissions in Canada
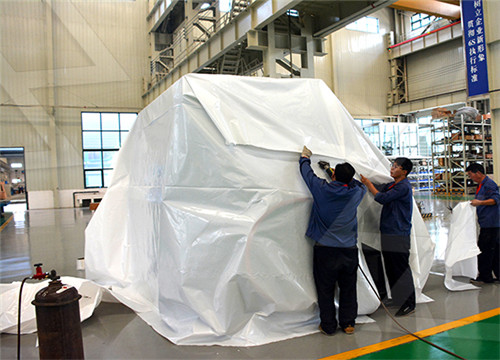
Research Background of Inert Anodes for Aluminum Electrolysis
2021年5月5日The amperage of the cell gradually developed from the initial 2–50 kA or greater. In the 1940s, Soderberg cells with vertical anode studs appeared. After the 1950s, the emergence of prebaked anode batteries brought electrolytic aluminum smelting technology into a new stage of large-scale development and modernization.
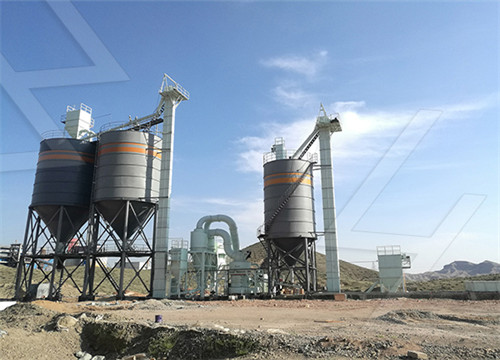
Controlled Ledge Profile of Aluminum Smelting Cell Using
2023年3月7日The results may provide database optimization for a more flexible aluminum smelting cell. This work aims to study the effect of sidewalls molten salt heat exchangers (MSHE) on the ledge profile in an aluminum smelting cell. Saevarsdottir G (2022) Net carbon consumption in aluminum electrolysis: impact of anode properties
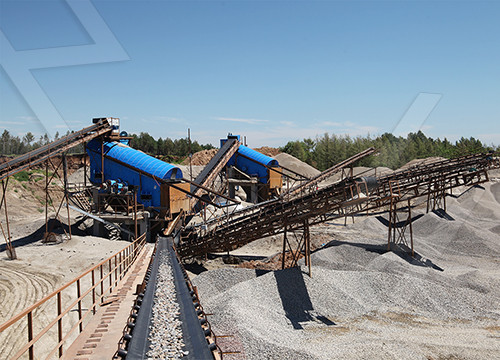
Primary Aluminium Smelting Energy Intensity
2022年8月9日Definitions Primary aluminium smelting energy intensity is reported as AC and DC power used for electrolysis by the Hall-Héroult processes per tonne of aluminium production.
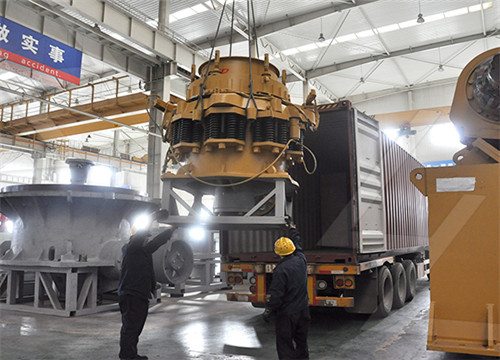
The Shift Toward Renewable Power in Aluminum Smelting
2023年3月8日The aluminum smelters in Europe obtain the highest percentage (6%) of their electrical power from renewable sources on the electrical power grid. The total installed and operational onshore wind power in France in 2020 was 17.4 GW, compared to 16.4 GW in 2019 for a 6.1% increase.
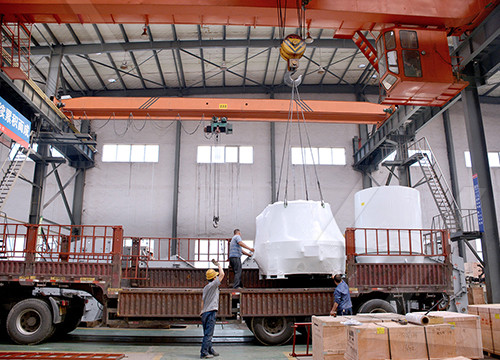
[PDF] Effect of sintering atmosphere on corrosion resistance of Ni
2016年11月1日@article{Tian2016EffectOS, title={Effect of sintering atmosphere on corrosion resistance of Ni/(NiFe2O4–10NiO) cermet inert anode for aluminum electrolysis}, author={Zhongliang Tian and Guo Weichang and Yanqing Lai and Zhang Kai and Li Jie}, journal={Transactions of Nonferrous Metals Society of China}, year={2016},
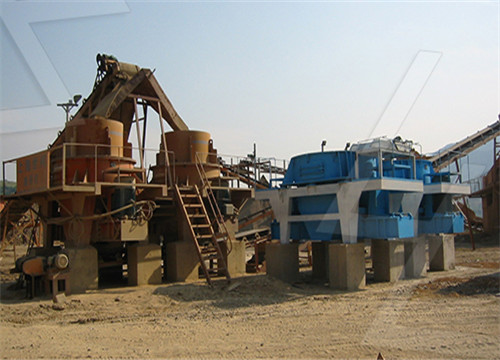
(PDF) The Aluminum Smelting Process and
2014年5月1日The industrial aluminum production process is addressed. The purpose is to give a short but comprehensive description of the electrolysis cell technology, the raw materials used, and the health...
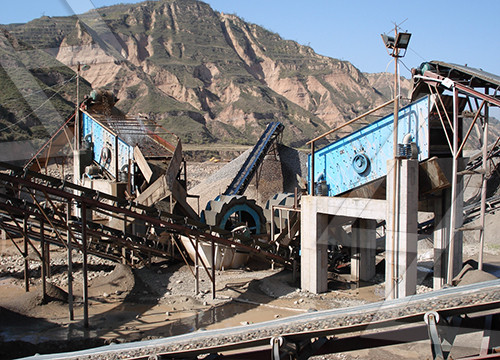
Applied Sciences Free Full-Text Stereolithographic Additive
Zirconia electrodes with dendritic patterns were fabricated by stereolithographic additive manufacturing (STL-AM). A solid electrolyte of yttria-stabilized zirconia (YSZ) was selected for oxygen separation in the molten salt electrolysis of aluminum smelting without carbon dioxide excretion. Thereafter, 4, 6, 8 and 12-coordinated dendritic structures composed
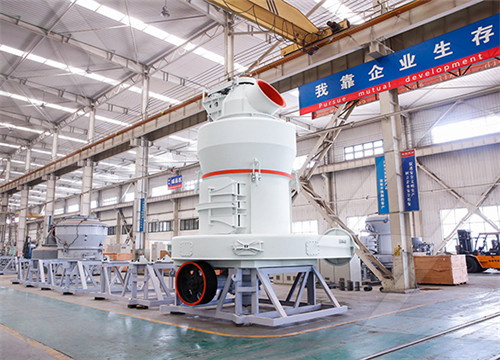
HalZero zero-emission electrolysis from Hydro
Hydro’s goal is to have an industrial-scale pilot up and running by 2030, making the HalZero technology viable for implementation in new electrolysis capacity from 2030 onwards. *The name HalZero alludes to the common way of naming Hydro Aluminium cell technology HAL and our promise to deliver zero emissions. Updated: January 19, 2022.
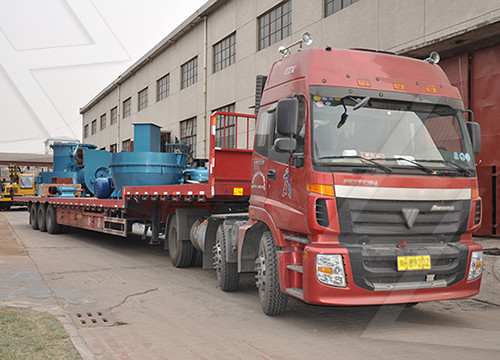
The TMS Industrial Aluminum Electrolysis Course SpringerLink
2022年2月5日The TMS Industrial Aluminum Electrolysis (IAE) Course on Theory and Practice has been held sixteen times in eight different countries in four continents since 1996. The location was always selected so that a visit to a nearby aluminum smelter was a part of the program of the course.
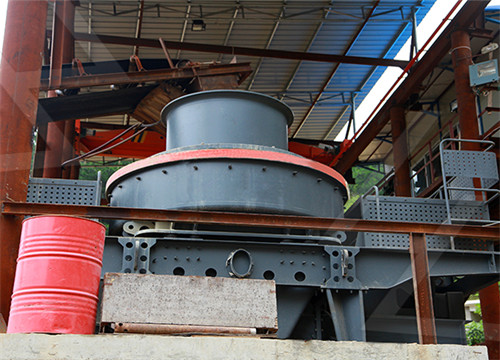
Decarbonizing Aluminum: Rolling Out a More Sustainable Sector
2022年2月25日The Hall-Heroult process of smelting the aluminum oxide to release pure aluminum comprises the second stage. By removing carbon anodes from aluminum’s electrolysis smelting reaction and replacing them with new nonreactive materials, the process would only emit oxygen as a byproduct. Though still in R&D, the
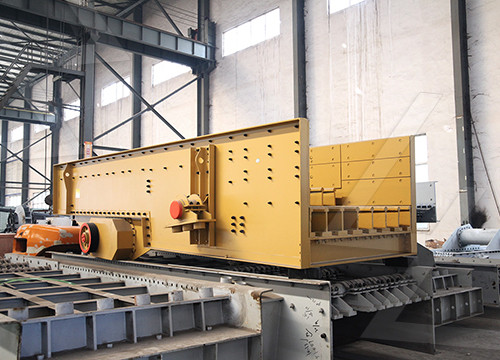
The Aluminum Smelting Process : Journal of Occupational and LWW
Inside, there are hundreds of aluminum electrolysis cells and each of them can be 10 to 15 m long. A photograph of a modern cell line is shown in Fig. 1. FIGURE 1: has far greater potential for achieving sustainability than improvements in energy efficiency within the aluminum smelting processes. Aluminum is also essential in environmental
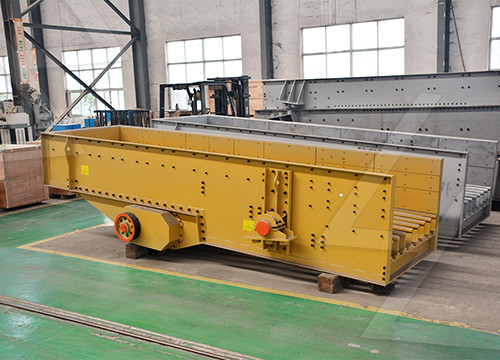
Aluminum Electrolysis an overview ScienceDirect Topics
Aluminum Electrolysis. Therefore, in the aluminium electrolysis process, the production schedule is to form the batch tapping of the cells into crucibles and arrange batch feeding of the crucibles into holding furnaces, considering the constraints of the electrolysis and cast. From: Computer Aided Chemical Engineering, 2018. Related terms: Smelting
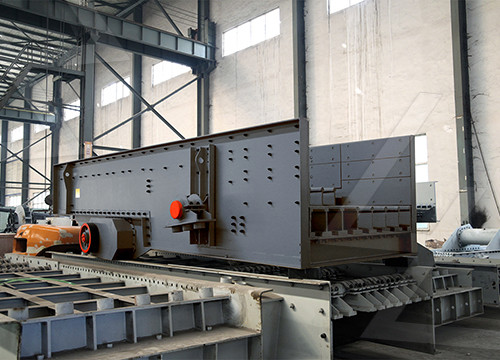
Research Background of Inert Anodes for Aluminum Electrolysis
2021年5月5日The cryolite-alumina molten salt electrolysis process of Hall and Heroult mainly consists of two steps: 1. Production of raw materials, including alumina, fluoride salts, carbon materials, and other raw materials for electrolysis. 2. Metal aluminum electrolysis production. The process of modern electrolytic aluminum smelting is shown in Fig. 1.2.
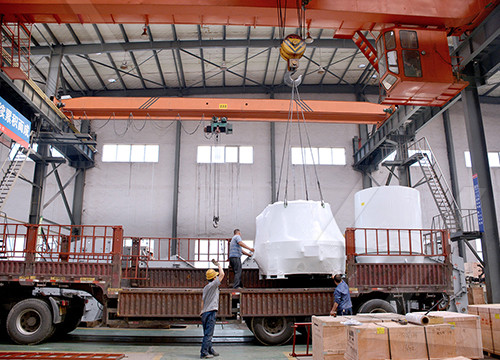
(PDF) The Aluminum Smelting Process and
2014年5月1日The industrial aluminum production process is addressed. The purpose is to give a short but comprehensive description of the electrolysis cell technology, the raw materials used, and the health...
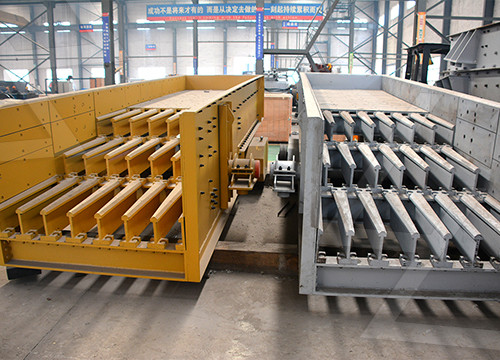
Controlled Ledge Profile of Aluminum Smelting Cell Using
2023年3月7日The results may provide database optimization for a more flexible aluminum smelting cell. This work aims to study the effect of sidewalls molten salt heat exchangers (MSHE) on the ledge profile in an aluminum smelting cell. Saevarsdottir G (2022) Net carbon consumption in aluminum electrolysis: impact of anode properties
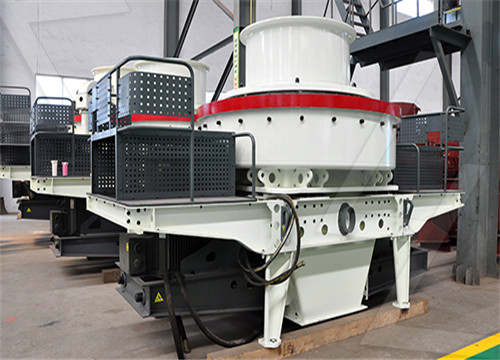
Primary Aluminium Smelting Energy Intensity
2022年8月9日Definitions Primary aluminium smelting energy intensity is reported as AC and DC power used for electrolysis by the Hall-Héroult processes per tonne of aluminium production.
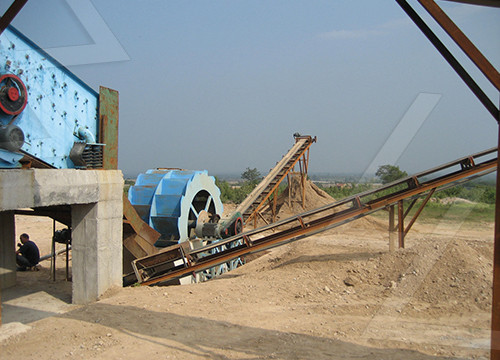
Applied Sciences Free Full-Text Stereolithographic Additive
Zirconia electrodes with dendritic patterns were fabricated by stereolithographic additive manufacturing (STL-AM). A solid electrolyte of yttria-stabilized zirconia (YSZ) was selected for oxygen separation in the molten salt electrolysis of aluminum smelting without carbon dioxide excretion. Thereafter, 4, 6, 8 and 12-coordinated dendritic structures composed
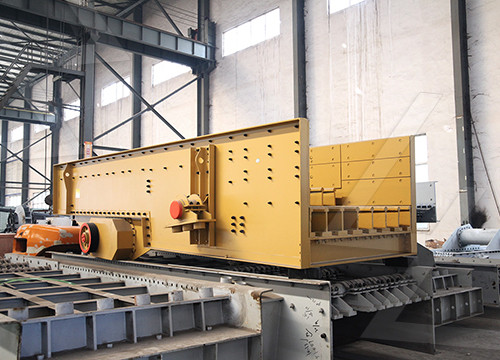
The Shift Toward Renewable Power in Aluminum Smelting
2023年3月8日The aluminum smelters in Europe obtain the highest percentage (6%) of their electrical power from renewable sources on the electrical power grid. The total installed and operational onshore wind power in France in 2020 was 17.4 GW, compared to 16.4 GW in 2019 for a 6.1% increase.
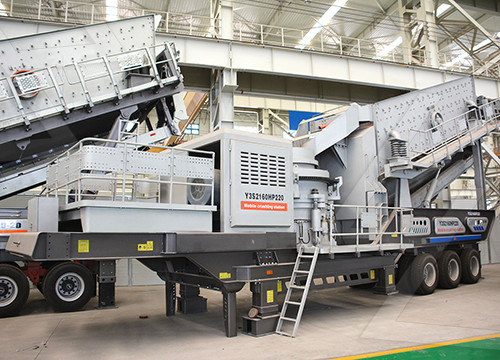
[PDF] Effect of sintering atmosphere on corrosion resistance of Ni
2016年11月1日@article{Tian2016EffectOS, title={Effect of sintering atmosphere on corrosion resistance of Ni/(NiFe2O4–10NiO) cermet inert anode for aluminum electrolysis}, author={Zhongliang Tian and Guo Weichang and Yanqing Lai and Zhang Kai and Li Jie}, journal={Transactions of Nonferrous Metals Society of China}, year={2016},
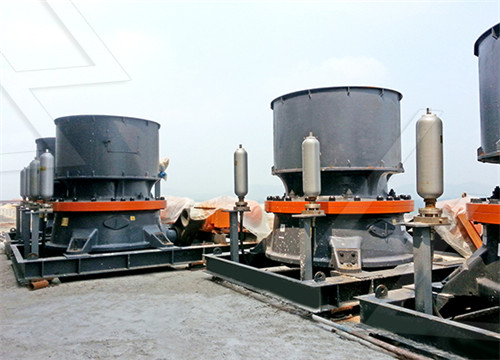
HalZero zero-emission electrolysis from Hydro
Hydro’s goal is to have an industrial-scale pilot up and running by 2030, making the HalZero technology viable for implementation in new electrolysis capacity from 2030 onwards. *The name HalZero alludes to the common way of naming Hydro Aluminium cell technology HAL and our promise to deliver zero emissions. Updated: January 19, 2022.
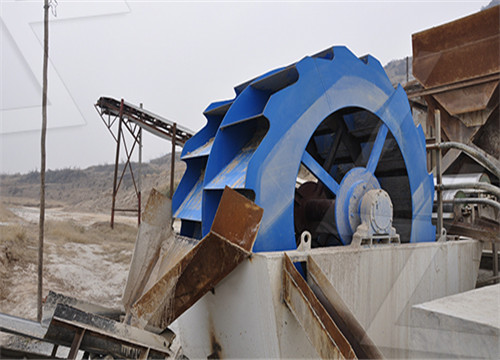
Aluminum Production in the Times of Climate Change: The Global
2019年11月21日Aluminum electrolysis is very energy intensive, with a global average of 14.1 kWh/tonne of aluminum in 2021, including conversion losses [49], and therefore the source of electric energy used for
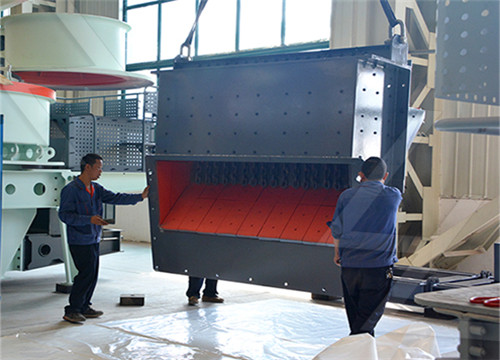
Aluminum Electrolysis Production Process SpringerLink
2021年5月5日3.2 Aluminum Tapping. The aluminum produced during the electrolysis process is periodically and quantitatively removed from the electrolytic cell. The time between two tapings is usually 1–2 days, and large cells can be tapped once a day. The tapping is carried out with a vacuum ladle.