Jamaica Iron Ore Iron Ore Process
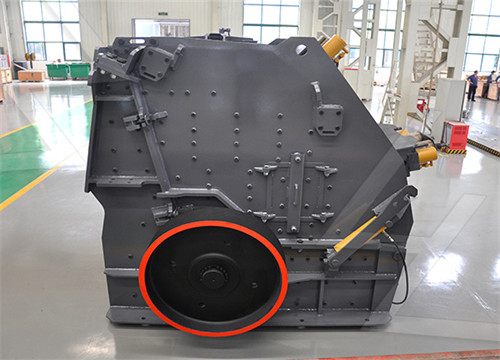
Iron processing Definition, History, Steps, Uses,Facts
Iron (Fe) is a relatively dense metal with a silvery white appearance and distinctive magnetic properties. It constitutes 5 percent by weight of the Earth’s crust, and it is the fourth most abundant element after oxygen,
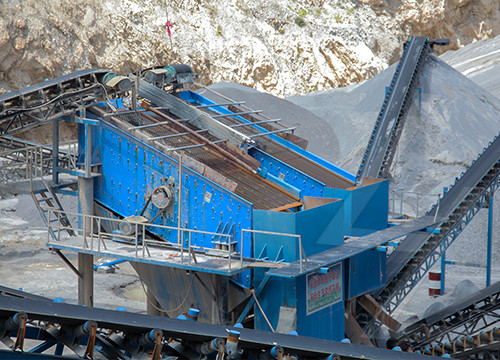
Iron processing Ores Britannica
Iron ore sintering consists of heating a layer of fines until partial melting occurs and individual ore particles fuse together. For this purpose, a traveling-grate machine is used,
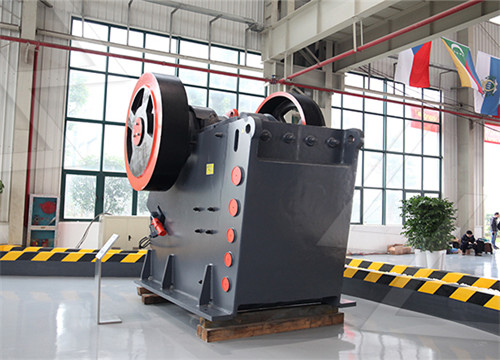
The six main steps of iron ore processing Multotec
Screening. We recommend that you begin by screening the iron ore to separate fine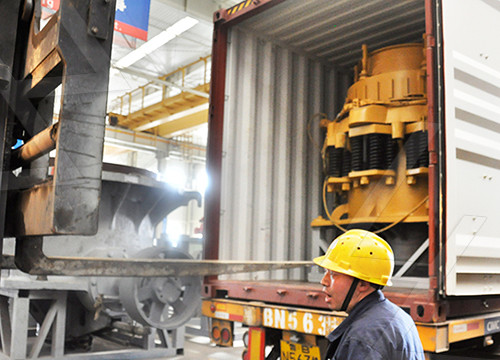
Ironmaking 101 From Ore to Iron with Blast Furnaces
2017年10月10日The carbon in the coke reacts with the oxygen to produce a reducing gas, carbon monoxide (CO) according to the following
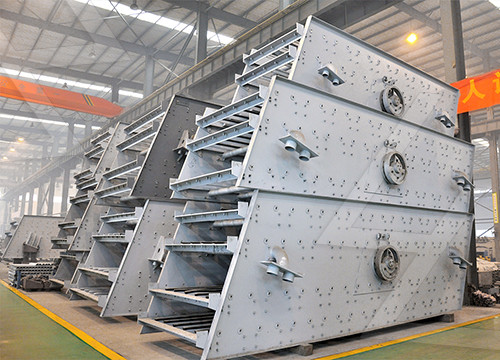
Sintering: A Step Between Mining Iron Ore and Steelmaking
2019年6月11日World resources are estimated to be greater than 800 billion tons of crude ore containing more than 230 billion tons of iron.
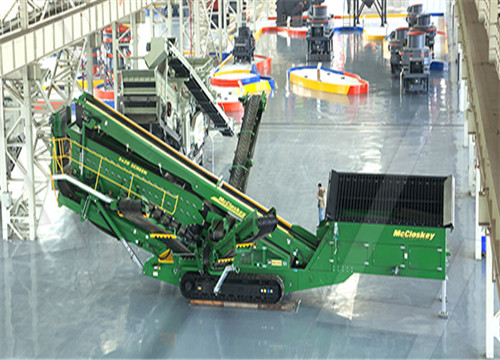
Iron Ore Pelletizing Process: An Overview IntechOpen
2018年7月11日The iron ore production has significantly expanded in recent years, owing to increasing steel demands in developing countries. However, the content of iron in ore deposits has deteriorated and low
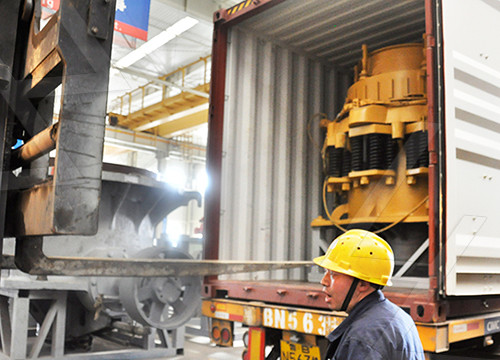
From mine to port LKAB
The crushed iron ore is then processed above ground to either fines or iron ore pellets. It is a complex process that takes place in several stages: Sorting: The ore is roughly sorted
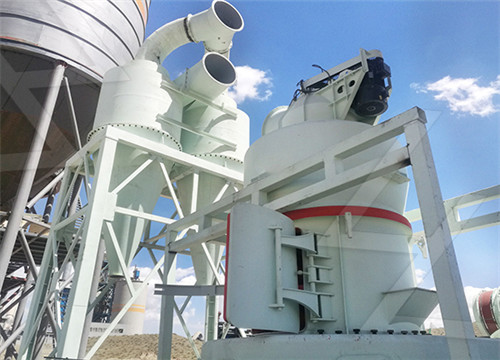
Bog iron Wikipedia
Bog iron is a form of impure iron deposit that develops in bogs or swamps by the chemical or biochemical oxidation of iron carried in solution. In general, bog ores consist primarily of iron oxyhydroxides, commonly
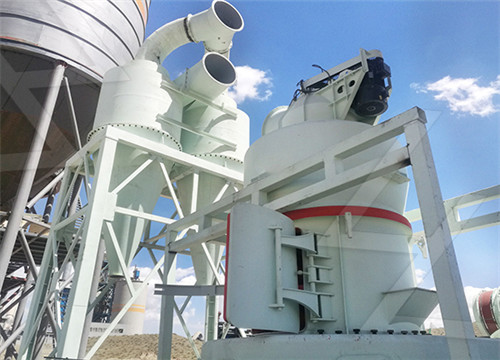
Mineral Commodity Summaries 2022 Iron Ore USGS
Domestic iron ore production was estimated to be 46 million tons in 2021, a 21% increase from 38.1 million tons in 2020. Total raw steel production was estimated to have
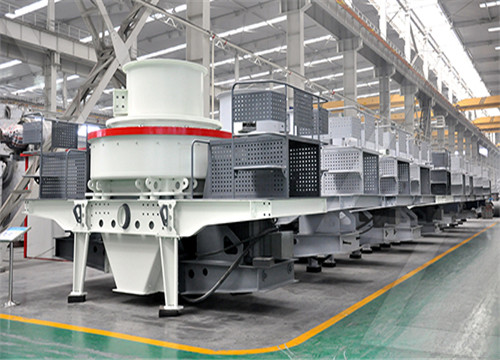
Iron Ore Beneficiation Mineral Processing
Iron Ore Processing Plant The iron ore beneficiation process mainly includes crushing, screening, grinding (ball mill), classification (classifier), separation (gravity separation,
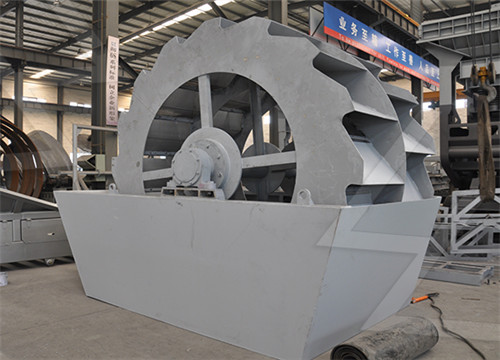
Iron ore BHP
Iron ore is mixed with coke (from super-heated metallurgical coal) in a blast furnace. Heating Air that has been heated to around 1,200°C is injected into the furnace, converting the iron ore to molten pig iron and slag.
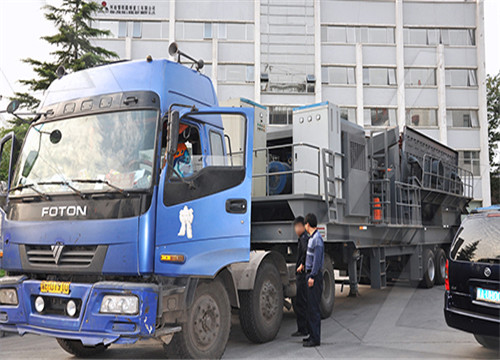
Iron processing Ores Britannica
Iron ores occur in igneous, metamorphic (transformed), or sedimentary rocks in a variety of geologic environments. Most are sedimentary, but many have been changed by weathering, and so their precise origin is difficult to determine. The most widely distributed iron-bearing minerals are oxides, and iron ores consist mainly of hematite (Fe2O3), which is red;
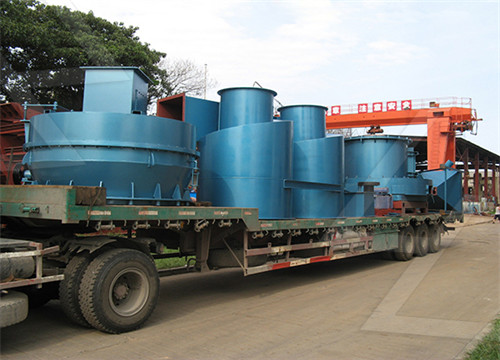
Ironmaking 101 From Ore to Iron with Blast Furnaces
2017年10月10日Iron is made by reacting iron ore (iron oxide and impurities), coke (a reductant) and limestone (CaCO 3) in a blast furnace. Iron ores with lower iron content such as taconite are first processed to
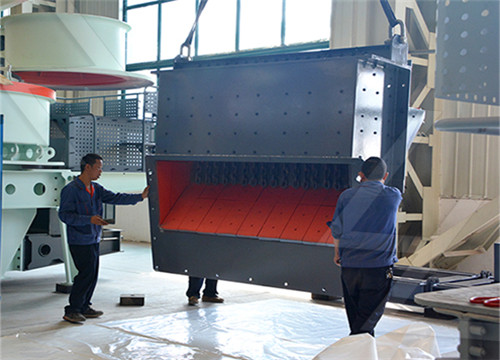
Iron ore quality a potential headwind to green steelmaking IEEFA
2022年6月28日DRI steelmaking requires a higher grade of iron ore than blast furnaces, the dominant global process. DR-grade iron ore ideally has an iron (Fe) content of 67% or more and such deposits are scarce --only a small percentage of global seaborne iron ore comes close to DR-grade. Seaborne Iron Ore Supply by Fe Content (%) Source: Vale
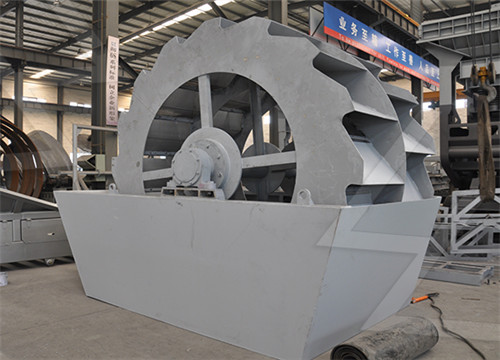
Sintering: A Step Between Mining Iron Ore and
2019年6月11日According to the U.S. Environmental Protection Agency, the sintering process converts fine-sized raw materials, including iron ore, coke breeze, limestone, mill scale, and flue dust, into an agglomerated

Metals Free Full-Text Impact of Iron Ore Pre-Reduction Degree
In the HPSR process, the type of iron ore or iron-containing residuals affects ore reduction by hydrogen. The process eliminates the prior agglomeration process, and iron ore fines can be directly introduced. The process is compared with fluidized bed reduction, which uses hydrogen as a reducing agent and fine ore as feed material.
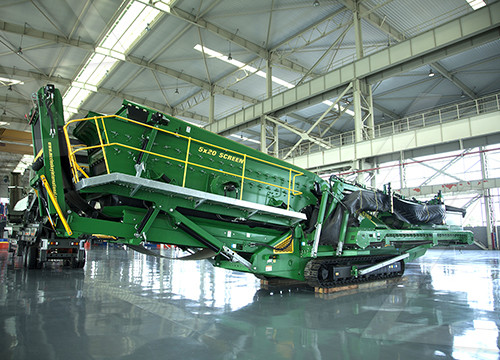
Iron Ore Mining Techniques Metal Extraction
Iron is concentrated by the process of calcinations. Once it is concentrated, the water and other volatile impurities such as sulfur and carbonates are removed. This concentrated ore is then mixed with limestone (CaCO 3)
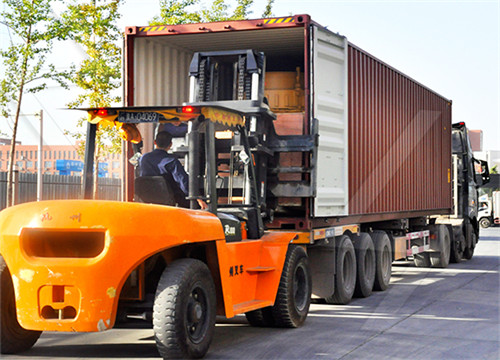
Non-isothermal reduction kinetics of low-grade iron ore-coal mini
A more accurate measure for iron phase distribution in this ore was carried out via chemical phase dissolution and the result is presented in Table 3.Hematite accounts for 90.67 % of the total iron content in the iron element, followed by martite, ferrosilite and magnetite, which is consistent with Table 2.In addition, the process mineralogy analysis results
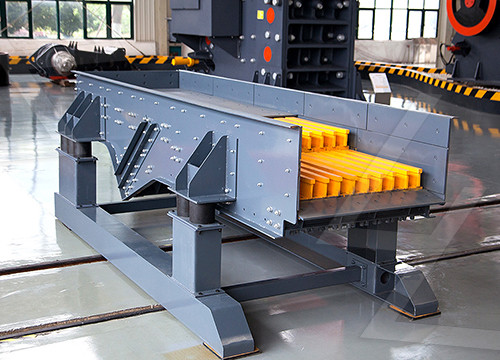
A Commercial Production Test of Iron Ore Sinter Using High
1997年11月15日To utilize pisolite ores as raw materials of iron ore sinter, a commercial production trial was carried out by designing the structure of quasi particles. Main results obtained from the trial are summarized as follows: (1) The commercial production test using 40 mass% pisolite ores in raw materials showed that high quality sinter was produced by
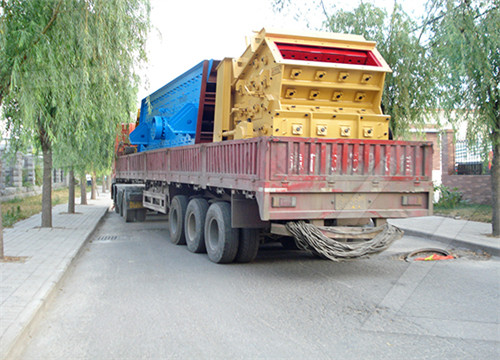
Phosphorus Removal of High Phosphorous Oolitic Iron Ore with
A process with acid leaching followed by hydrogen-based fluidized reduction and melt separation is presented for recovering DRI (direct reduced iron) from high-phosphorus oolitic hematite in this study, and the aim of this study is to provide theoretical and technical basis for economical and rational use of high phosphorus oolitic iron ores
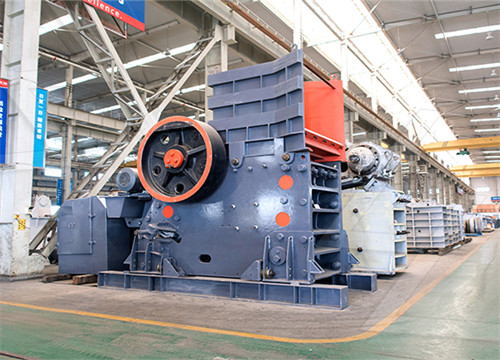
How iron is made material, manufacture, making,
Iron ore is converted into various types of iron through several processes. The most common process is the use of a blast furnace to produce pig iron which is about 92-94% iron and 3-5% carbon with smaller amounts of
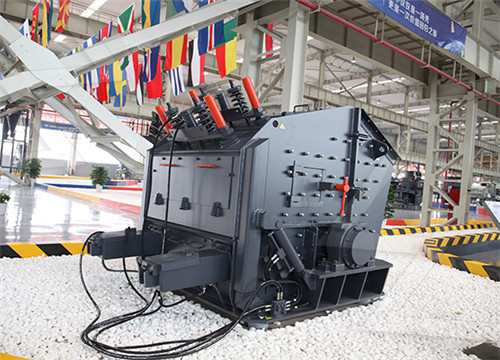
(PDF) iron-steel making From start to finish ResearchGate
2019年12月27日PDF On Dec 27, 2019, Mr. Bhavesh R Rana published iron-steel making From start to finish Find, read and cite all the research you need on ResearchGate
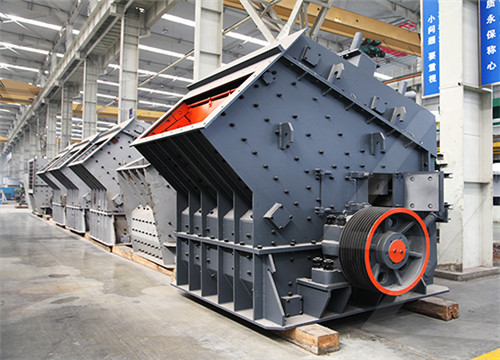
How iron ore is mined? linkedin
2023年3月7日Iron ore is a mineral substance that is extracted from the earth's crust and is used in the production of steel. The process of mining iron ore can be divided into two main stages: exploration and
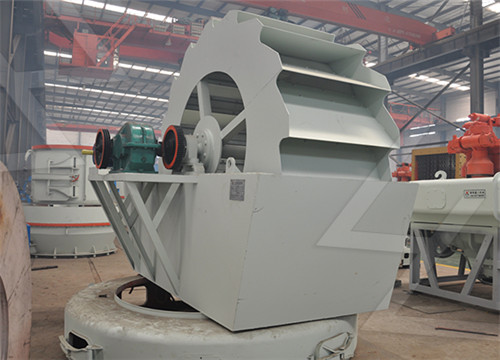
Beneficiation Plants and Pelletizing Plants for Utilizing Low
1. Iron ore supply and demand outline 1.1 Types of iron ore Iron ores can be classified in different ways. The most important has to do with the iron content. In many cases, ore with a total iron content of 60% to 63%, or greater, is regarded as high grade, and ore with a lower iron content is regarded as low grade.
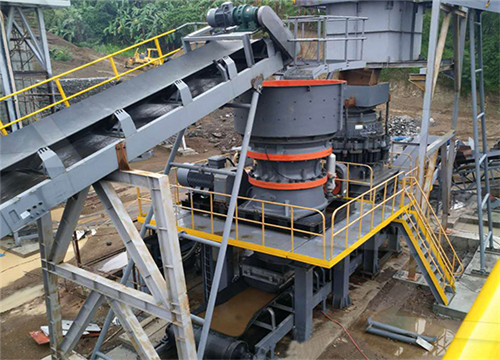
Iron ore BHP
Iron ore is mixed with coke (from super-heated metallurgical coal) in a blast furnace. Heating Air that has been heated to around 1,200°C is injected into the furnace, converting the iron ore to molten pig iron and slag.
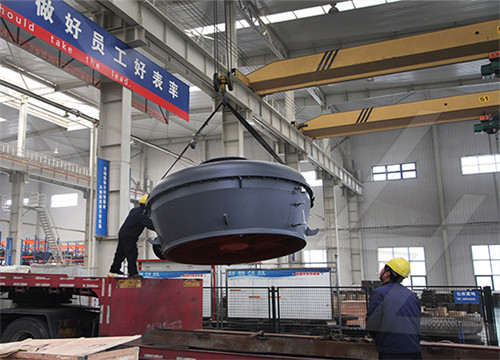
Iron processing Ores Britannica
Iron ore sintering consists of heating a layer of fines until partial melting occurs and individual ore particles fuse together. For this purpose, a traveling-grate machine is used, and the burning of fine coke (known as coke breeze)
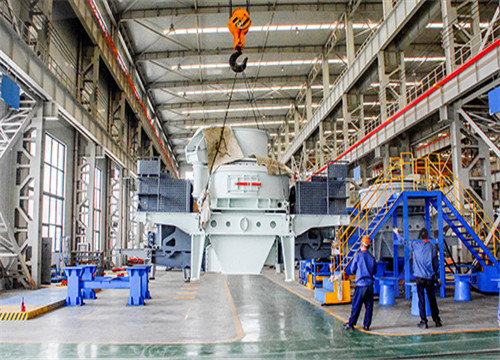
Ironmaking 101 From Ore to Iron with Blast Furnaces
2017年10月10日Iron is made by reacting iron ore (iron oxide and impurities), coke (a reductant) and limestone (CaCO 3) in a blast furnace. Iron ores with lower iron content such as taconite are first processed to
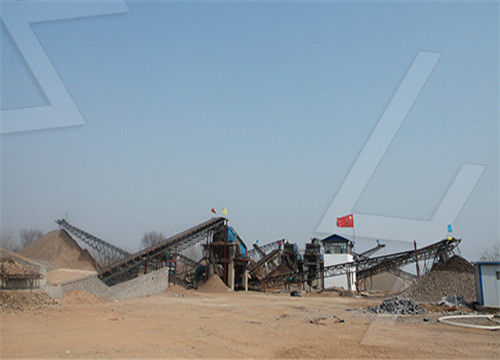
Iron Ore Pelletizing Process: An Overview IntechOpen
2018年7月11日The iron ore pelletizing process consists of three main steps: Pelletizing feed preparation and mixing: the raw material (iron ore concentrate, additives—anthracite, dolomite—and binders are prepared
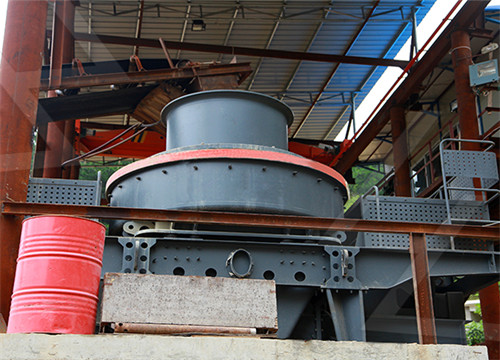
Metals Free Full-Text Impact of Iron Ore Pre-Reduction Degree
In the HPSR process, the type of iron ore or iron-containing residuals affects ore reduction by hydrogen. The process eliminates the prior agglomeration process, and iron ore fines can be directly introduced. The process is compared with fluidized bed reduction, which uses hydrogen as a reducing agent and fine ore as feed material.
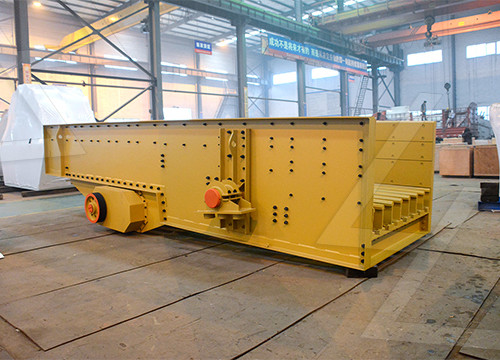
Non-isothermal reduction kinetics of low-grade iron ore-coal mini
A more accurate measure for iron phase distribution in this ore was carried out via chemical phase dissolution and the result is presented in Table 3.Hematite accounts for 90.67 % of the total iron content in the iron element, followed by martite, ferrosilite and magnetite, which is consistent with Table 2.In addition, the process mineralogy analysis results
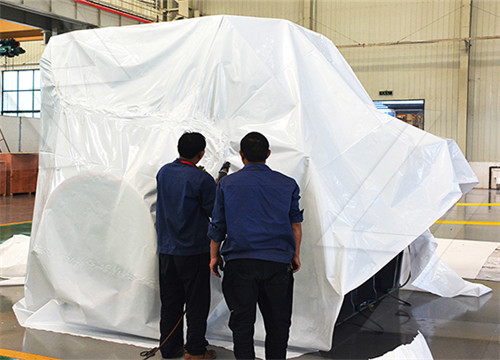
Iron Ore Mining Techniques Metal Extraction
Iron is concentrated by the process of calcinations. Once it is concentrated, the water and other volatile impurities such as sulfur and carbonates are removed. This concentrated ore is then mixed with limestone (CaCO 3)
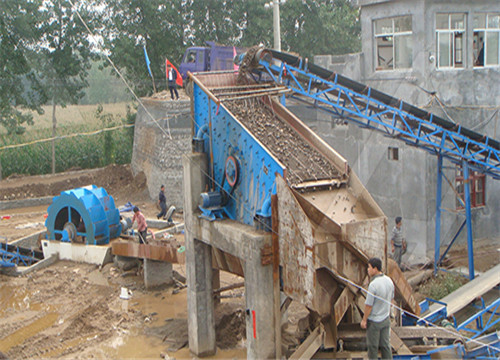
How iron is made material, manufacture, making,
Iron ore is converted into various types of iron through several processes. The most common process is the use of a blast furnace to produce pig iron which is about 92-94% iron and 3-5% carbon with smaller amounts of
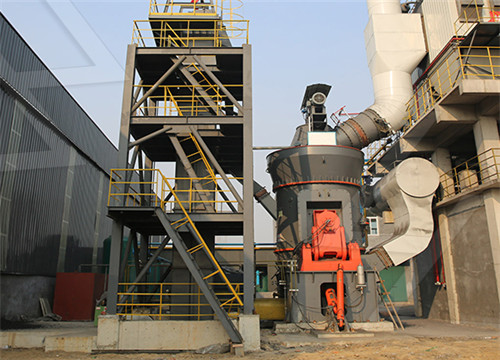
A Commercial Production Test of Iron Ore Sinter Using High
1997年11月15日To utilize pisolite ores as raw materials of iron ore sinter, a commercial production trial was carried out by designing the structure of quasi particles. Main results obtained from the trial are summarized as follows: (1) The commercial production test using 40 mass% pisolite ores in raw materials showed that high quality sinter was produced by
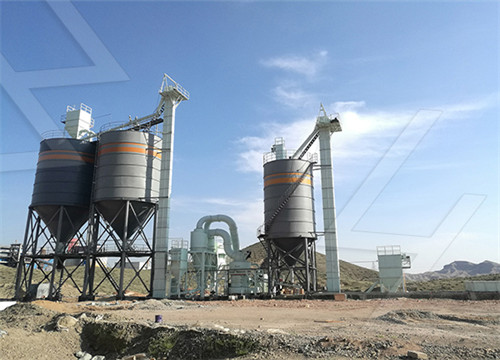
Phosphorus Removal of High Phosphorous Oolitic Iron Ore with
A process with acid leaching followed by hydrogen-based fluidized reduction and melt separation is presented for recovering DRI (direct reduced iron) from high-phosphorus oolitic hematite in this study, and the aim of this study is to provide theoretical and technical basis for economical and rational use of high phosphorus oolitic iron ores
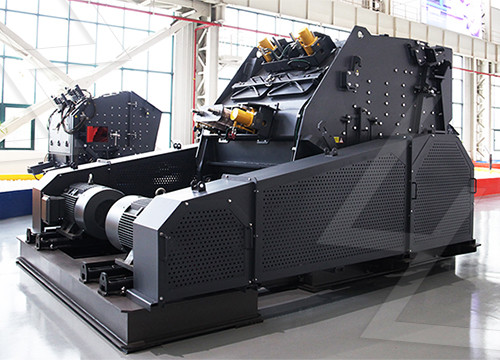
How iron ore is mined? linkedin
2023年3月7日Iron ore is a mineral substance that is extracted from the earth's crust and is used in the production of steel. The process of mining iron ore can be divided into two main stages: exploration and
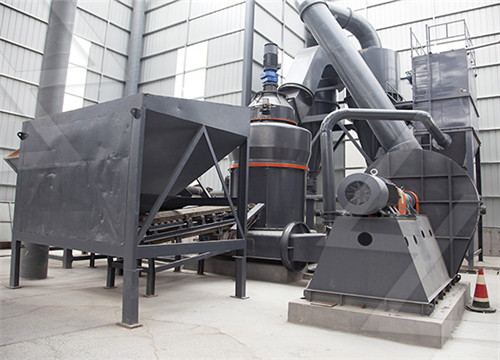
Types of Iron Ore: Hematite vs. Magnetite INN
2022年8月30日Because of its high iron content, hematite ore must undergo only a simple crushing, screening and blending process before being shipped off for steel production. For that reason, hematite...
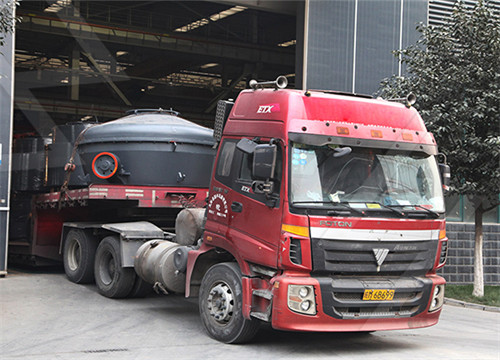
(PDF) iron-steel making From start to finish ResearchGate
2019年12月27日PDF On Dec 27, 2019, Mr. Bhavesh R Rana published iron-steel making From start to finish Find, read and cite all the research you need on ResearchGate
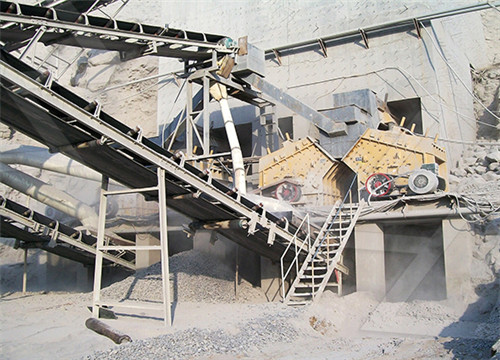
Iron Ore an overview ScienceDirect Topics
Iron ore is regarded as the second most important commodity behind oil. As an essential input for the production of crude steel, iron ore feeds the world’s largest trillion-dollar-a-year metal market and is the backbone of global infrastructure. To meet the growing demand for steel products, world iron ore production has increased