Feed Arrangement Cone Mining Mill
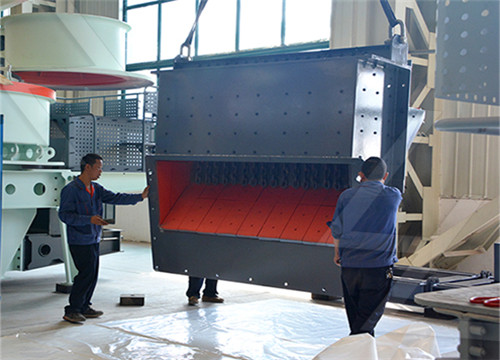
Cone crusher basics in 4 minutes SRP
Cone crusher basics in 4 minutes This is the starting point for understanding how cone crushers work and how they can make your mine or quarry more productive.
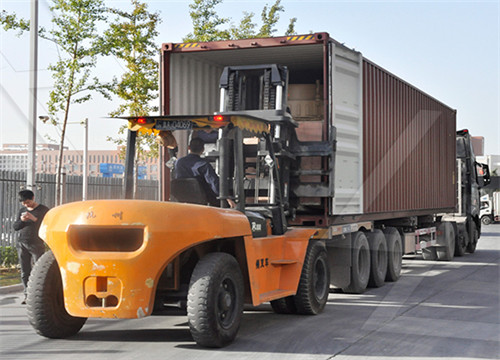
进一步探索
Operation Manual For Cone CrusherCone Crusher VS Gyratory Crusher JXSC Mine根据热度为您推荐•反馈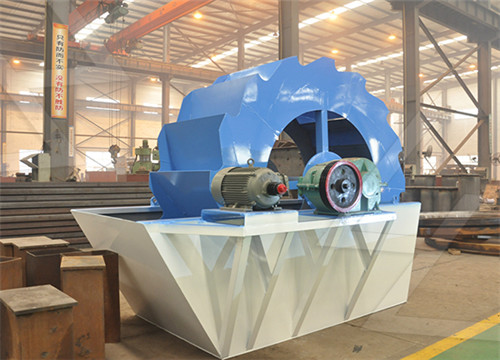
Cone Mill KEK Mills Veratile Size Reduction Kemutec
根据热度为您推荐•反馈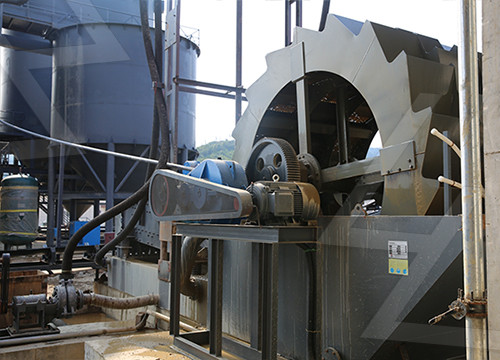
SAG Mill Liner Design Mineral ProcessingMetallurgy
2016年6月6日Based on experience, mill-liner designs have moved toward more open-shell lifter spacing, increased pulp lifter volumetric capacity,
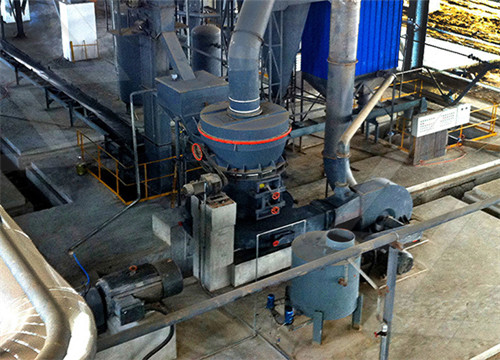
AMIT 135: Lesson 5 Crushing Mining Mill Operator
The purpose of the primary crusher is to reduce the ROM ore to a size amenable for feeding the secondary crusher or the SAG mill grinding
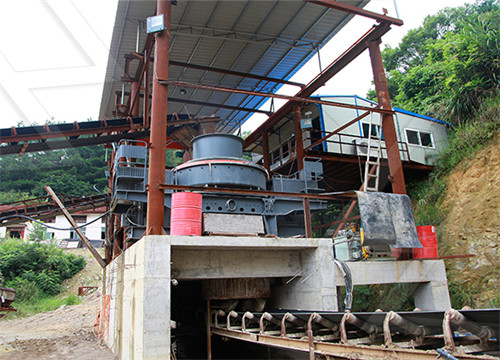
Introduction to Cyclones AusIMM
A grinding mill needs a classifier to extract the particles that have been milled sufficiently A cyclone does this, with the cyclone overflow being the mill final product, and the

Types of Classifiers in Mineral Processing
2016年5月26日The feed enters the cone through an inner truncated cone, settled solids gradually building up in the cone to a point restricting the out-flow of the inner truncated cone. This arrangement maintains
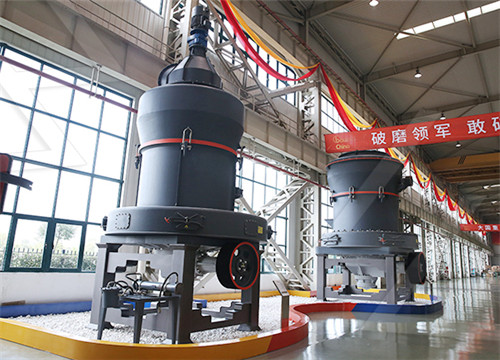
Grinding mills for mining and minerals processing
Metso Outotec continues to pioneer innovations in horizontal grinding mills technology with over a century of leadership, exceptional performance and unmatched expertise by
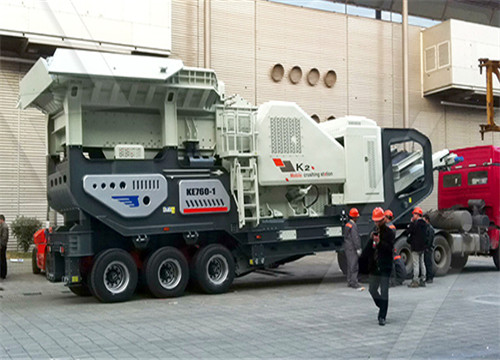
Flexible milling and grinding solutions that last
Optimal feed material milling and grinding solutions Carefully crafted to meet your milling and grinding needs, our robust and well-designed solutions are highly adaptable for a range of feed materials. With compact layouts,
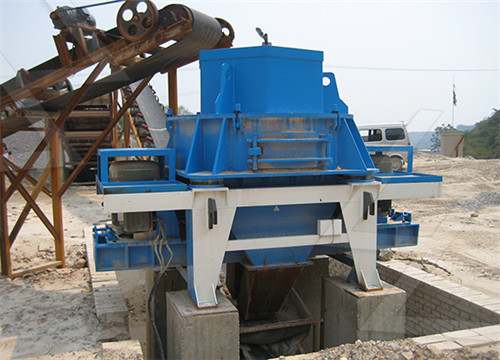
SAG Mill Autogenous and Semi-Autogenous Mills
Single stage SAG Mills are very beneficial in reducing CAPEX for plants with a staged throughput approach. When future tonnage is to be increased, the SAG Mill can feed downstream ball milling to boost capacity. Fuller
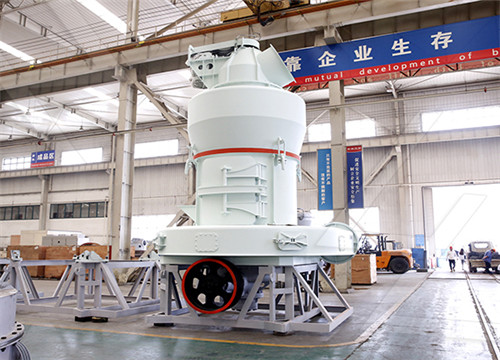
AMIT 145: Lesson 2 Classifying Cyclones Mining
Inlet Feed Designs [image 145-2-9] Cone Section. Cone angles vary from 6 ° to 90 ° 20 ° cone angle has been the standard; however, 10 ° is common for cyclones in the mineral industry. High cone angles are typically used
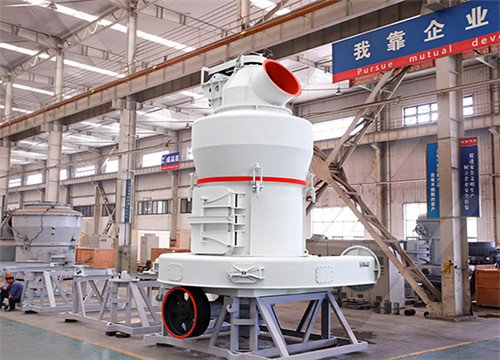
Cone Mill KEK Mills Veratile Size Reduction
The KEK Cone Mill is globally recognised as one of the most versatile size reduction milling machines, due to the wide range of materials it processes. The KEK range includes the widest available, from lab through to bulk
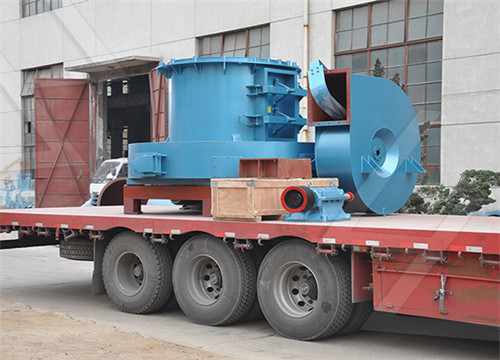
SAG Mill Liner Design Mineral Processing
2016年6月6日Based on experience, mill-liner designs have moved toward more open-shell lifter spacing, increased pulp lifter volumetric capacity, and a grate design to facilitate maximizing both pebble-crushing circuit
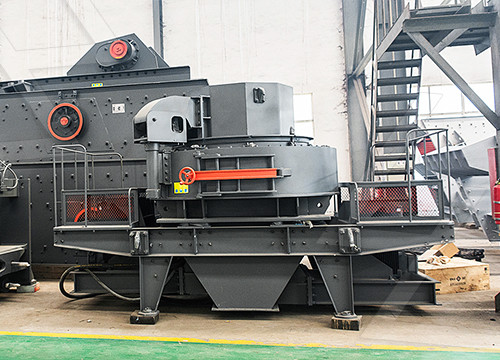
CrushingScreening Plant Mineral Processing
2016年7月12日A typical Ross chain feeder consists of six lengths weighing 5½ tons. The feeder is driven by a 5-hp. motor through a bronze worm reducer, with a sprocket chain-gear and pinion arrangement. This
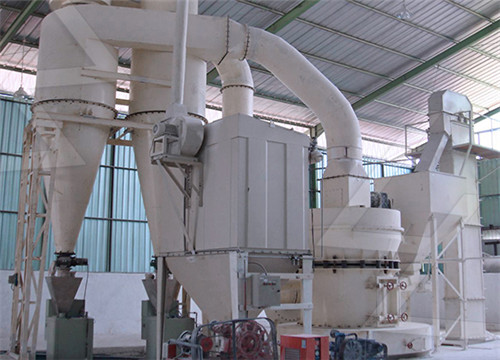
SAG Mill Autogenous and Semi-Autogenous Mills
Single stage SAG Mills are very beneficial in reducing CAPEX for plants with a staged throughput approach. When future tonnage is to be increased, the SAG Mill can feed downstream ball milling to boost capacity. Fuller
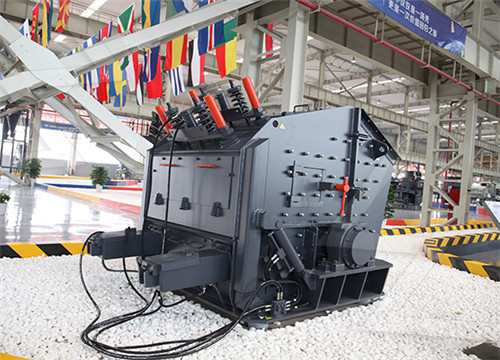
Kek Cone Mills Kemutec
Kek Cone Mill for Gentle and Intermediate Grinding “FULLY CUSTOM BUILT AND DESIGNED CONE MILLS” Kek Cone Mills are low energy and versatile mills for the gentle, intermediate grinding and deagglomeration
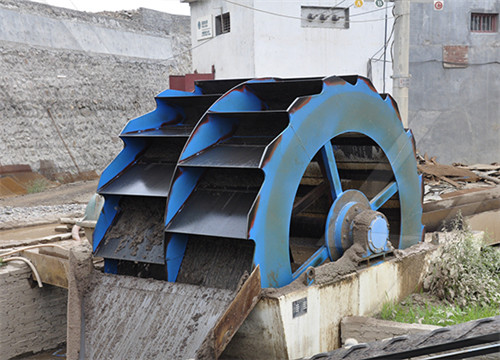
Stirred Media Detritors (SMD) Metso Outotec
Feeding SMD from a thickener or scalping cyclone regulates the flow very well and generates a suitable feed density. Feed Density. The feed density is required, in conjunction with the feed flow-rate, to establish the feed rate of solids. Typical operational feed density range is 30-60% solids.
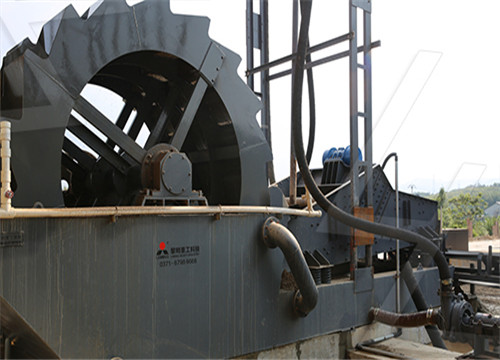
Flexible milling and grinding solutions that last
Optimal feed material milling and grinding solutions. Carefully crafted to meet your milling and grinding needs, our robust and well-designed solutions are highly adaptable for a range of feed materials. With
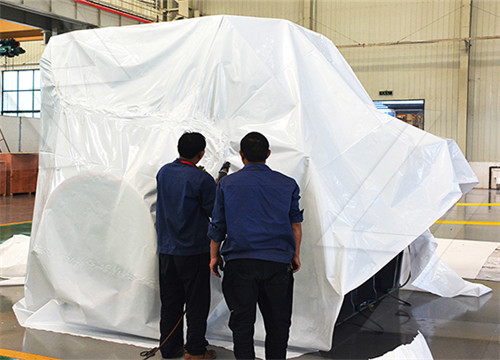
Back to Basics Hammer Milling and Jet Milling
feeding (e.g., making metering into the mill difficult), grind-ing (e.g., plugging the hammer mill screen or blocking the air classifier of a jet mill), and collection (e.g., plugging the bag filters). There are two ways to grind sticky materials. The first solution is to dry the material prior to grinding, or dry and
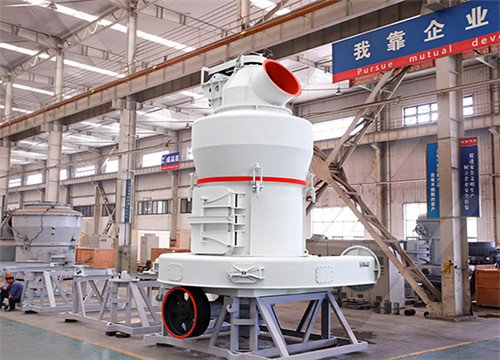
Gyratory Crusher Explained saVRee
The process of reducing mined ore for processing is known as ‘comminution’, which is defined as ‘the action of reducing a material, especially a mineral ore, to minute particles or fragments’; this is
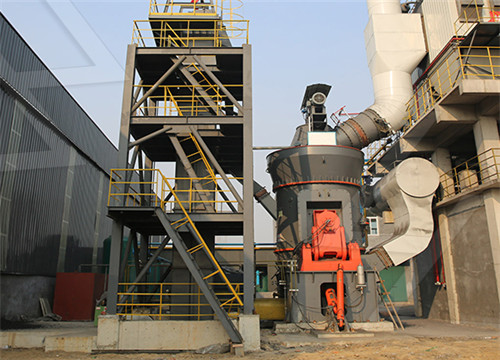
(PDF) Cone Crusher Performance ResearchGate
2015年5月13日A cone crusher is a core component of the particle crushing process employed in various industrial sectors [1]. Capacity is one of the most important indexes of cone crushers, which determines...
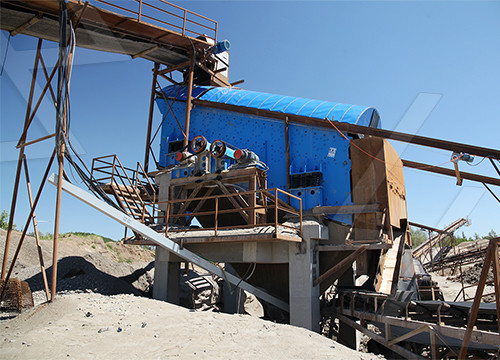
Tips to maximize crushing efficiency PitQuarry
2019年5月13日Efficiency can be defined by the ratio of a machine’s work to the energy supplied to the machine. To apply what this means to your crusher, operations produce the exact sizes in the reduction process that their market demands. In the past, quarries produced a range of single-size aggregate products up to 40 mm in size.
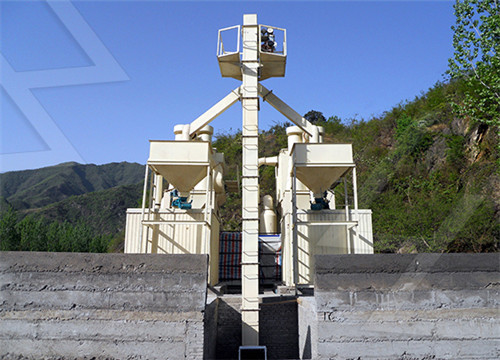
CNU Feed arrangement of ball mill Google Patents
The utility model belongs to the technical field of the grinding equipment technique and specifically relates to a feed arrangement of ball mill, which comprises a supporting pedestal and is characterized by further comprising, install the inlet pipe on the support base, the one end of inlet pipe is connected with the feed inlet of ball mill, the other end
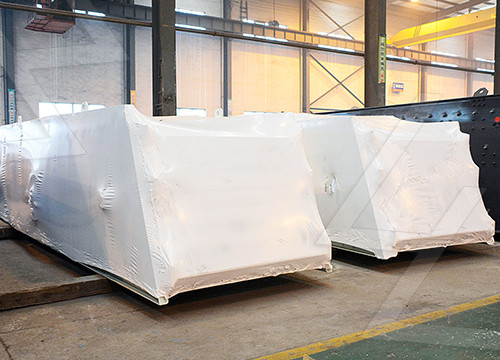
Vibrocone Mining Crushers Cone Crusher by Mining
Feed arrangements and discharge with product conveyor belts require minimal changes in most cases. Vibrocone can be adapted to the same footprint as a conventional 7′ crusher so there is no need to rebuild the entire concrete foundation.
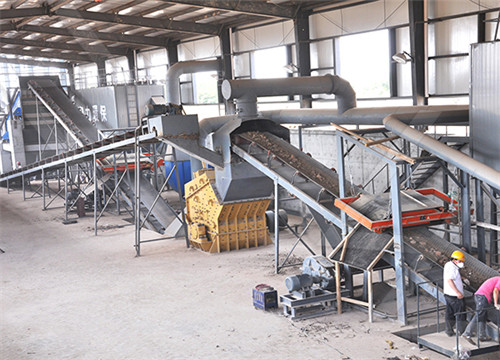
AMIT 145: Lesson 2 Classifying Cyclones Mining
Inlet Feed Designs [image 145-2-9] Cone Section. Cone angles vary from 6 ° to 90 ° 20 ° cone angle has been the standard; however, 10 ° is common for cyclones in the mineral industry. High cone angles are typically used
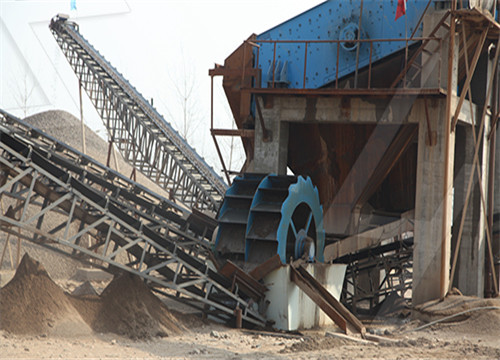
Cone Mill KEK Mills Veratile Size Reduction
The KEK Cone Mill is globally recognised as one of the most versatile size reduction milling machines, due to the wide range of materials it processes. The KEK range includes the widest available, from lab through to bulk
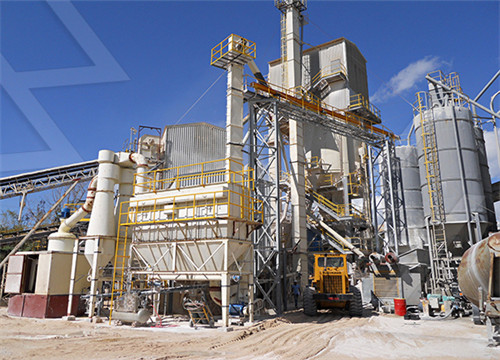
SAG Mill Autogenous and Semi-Autogenous Mills
Single stage SAG Mills are very beneficial in reducing CAPEX for plants with a staged throughput approach. When future tonnage is to be increased, the SAG Mill can feed downstream ball milling to boost capacity. Fuller-Traylor SAG/AG Mills range in size from 4.3m through 12.2m in diameter with powers as high as 28,000 kW.
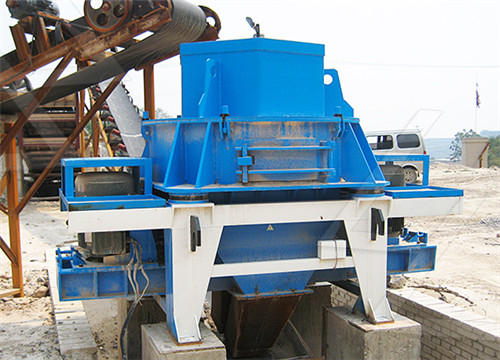
SAG Mill Liner Design Mineral ProcessingMetallurgy
2016年6月6日Based on experience, mill-liner designs have moved toward more open-shell lifter spacing, increased pulp lifter volumetric capacity, and a grate design to facilitate maximizing both pebble-crushing circuit utilization and SAG mill capacity. As a guideline, mill throughput is maximized with shell lifters between ratios of 2.5:1 and 5.0:1.
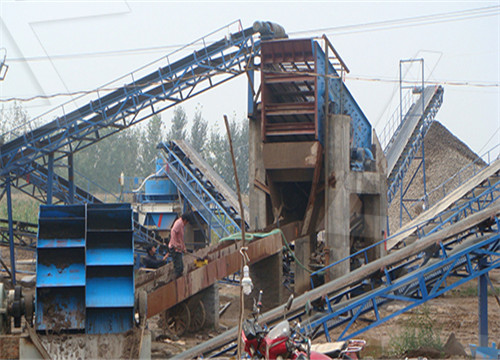
SAG Mill Grinding Circuit Design Mineral Processing
2016年6月6日Single stage AG/SAG milling. AG/SAG mills as a primary grinding stage in a circuit with or without additional stages of comminution. Inclusion of pebble-crushing circuits in the AG/SAG circuit. Circuits above, but with feed preparation including two stages of crushing—typically referenced as pre-crushing.
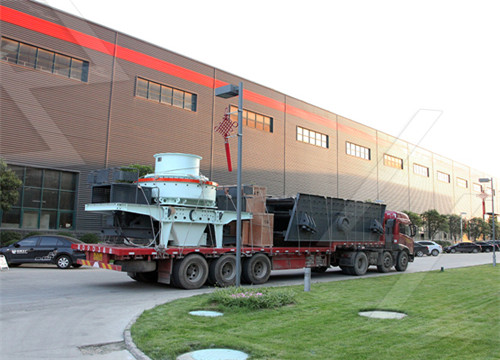
Kek Cone Mills Kemutec
Kek Cone Mill for Gentle and Intermediate Grinding “FULLY CUSTOM BUILT AND DESIGNED CONE MILLS” Kek Cone Mills are low energy and versatile mills for the gentle, intermediate grinding and deagglomeration of powders and granules. Milled Particle Size Range D50 500µ to < 250µ Contact Us Put Us To The Test Download Brochure
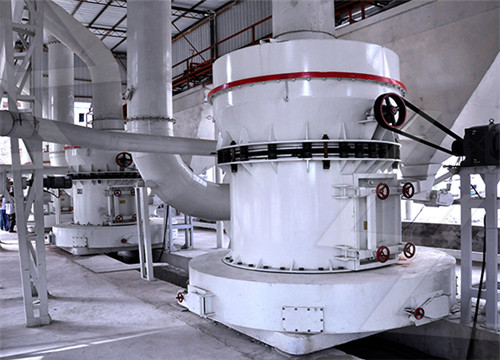
Stirred Media Detritors (SMD) Metso Outotec
Feeding SMD from a thickener or scalping cyclone regulates the flow very well and generates a suitable feed density. Feed Density. The feed density is required, in conjunction with the feed flow-rate, to establish the feed rate of solids. Typical operational feed density range is 30-60% solids.
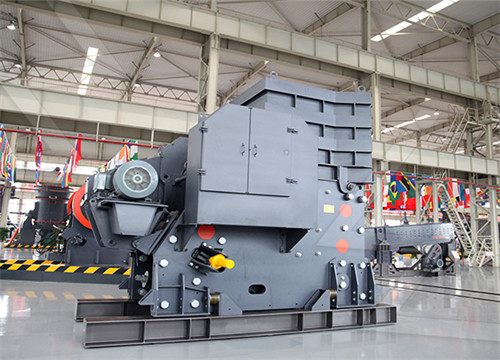
Flexible milling and grinding solutions that last
Optimal feed material milling and grinding solutions. Carefully crafted to meet your milling and grinding needs, our robust and well-designed solutions are highly adaptable for a range of feed materials. With compact layouts, long-lasting wear parts and easy access for maintenance, you can save on civil, operation and maintenance costs.
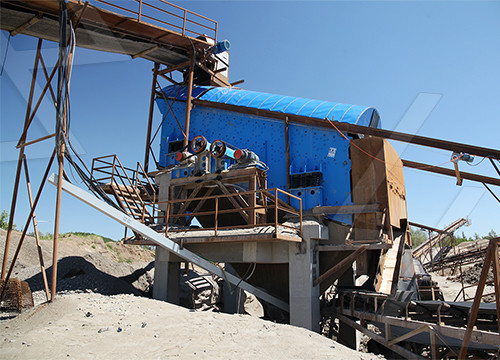
Industrial Hammer Mills and Pulverizing Machines Pulva
Mining; Hammer Mill Pulverizer Benefits. The Model A is also available with an overhead feed screw arrangement which has a single 2-15/16” diameter feed screw for handling larger feed stock and can take a feed size up to 2”. A gravity feed model is also available which is recommended for high capacity grinding where fineness of
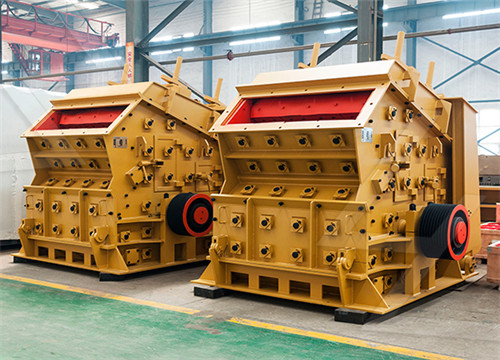
Back to Basics Hammer Milling and Jet Milling
feed stream in hammer mills for grinding tough materials. However, liquid nitrogen is seldom used in jet milling opera-tions due to the swift heat exchange between the material and the grinding gas. The grinding gas heats up the super-cooled feed stream, and the material loses its brittleness when it absorbs this heat. Stickiness.

Gyratory Crusher Explained saVRee
The process of reducing mined ore for processing is known as ‘ comminution ’, which is defined as ‘the action of reducing a material, especially a mineral ore, to minute particles or fragments ’; this is normally achieved at mining operations through one or more stages of crushing and milling. Early mining activities were labour intensive.
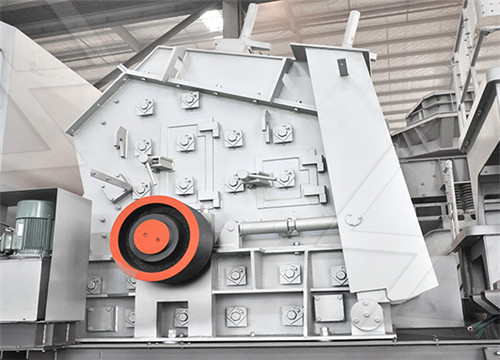
Tips to maximize crushing efficiency PitQuarry
2019年5月13日Efficiency can be defined by the ratio of a machine’s work to the energy supplied to the machine. To apply what this means to your crusher, operations produce the exact sizes in the reduction process that their market demands. In the past, quarries produced a range of single-size aggregate products up to 40 mm in size.
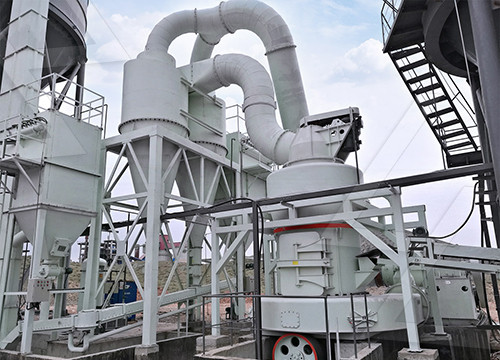
Crushers, Pulverizers, Grinders Lavallab
For over 35 years Laval Lab Inc is the one-stop specialist for size reduction of all types of materials. We have the right crusher, pulveriser, grinder or mill for the laboratory to pilot plant sample processing. We serve all major industries such as mining and metallurgy, chemistry, pharmaceutical, cement, material engineering, environment
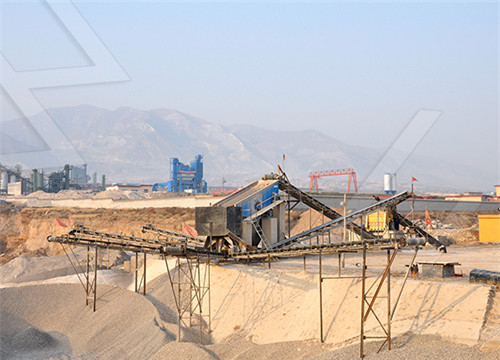
cone mining mill arrangement
cone mining mill arrangement. Cone Mill for Size Reduction Increase productivity and improve production versatility and reliability across a wide array of dry milling and wet conditioning applications with conical milling Cone milling is one of the most common methods of milling in the pharmaceutical We are a professional mining machinery