Iron Ore Processing Is Simple
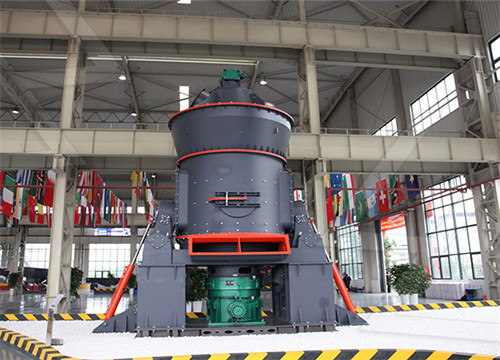
Iron processing Definition, History, Steps, Uses,Facts
iron processing, use of a smelting process to turn the ore into a form from which products can be fashioned. Included in this article also is a discussion of the mining of iron and of its preparation for smelting. Iron (Fe) is a
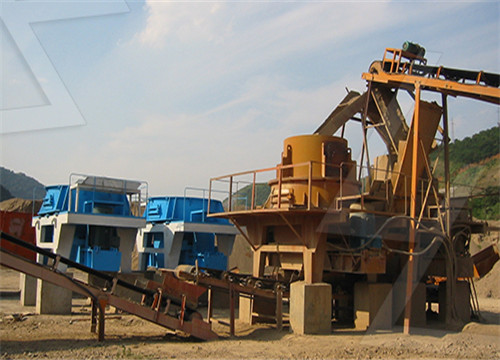
Iron processing Iron making Britannica
This is any process in which iron is extracted from ore at a temperature below the melting points of the materials involved. Gangue remains in the spongelike product, known as direct-reduced iron, or DRI, and must be
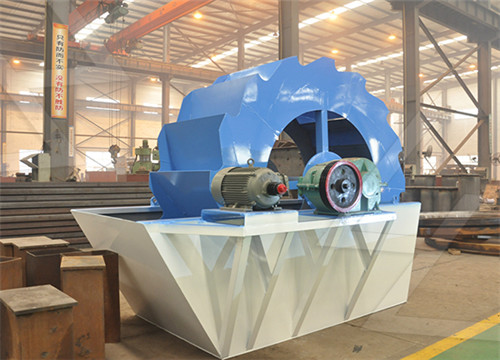
Iron ore BHP
根据热度为您推荐•反馈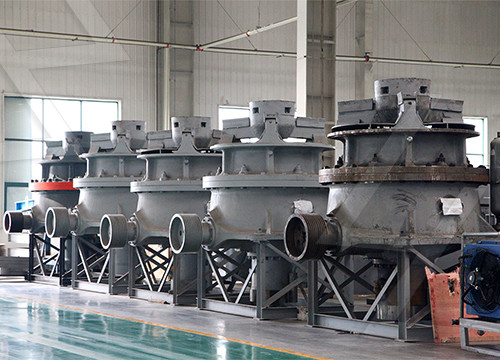
Sintering: A Step Between Mining Iron Ore and Steelmaking
2019年6月11日The USGS defines iron ore as a mineral substance which, when heated in the presence of a reductant, will yield metallic iron (Fe).
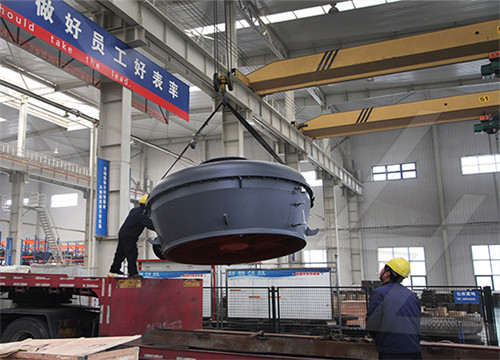
Iron Ore Processing an overview ScienceDirect Topics
Iron Ore Processing In India, where iron ore processing is one of the major industries, the generation of tailings is estimated to be 10-25 % of the total iron ore mined, amounting
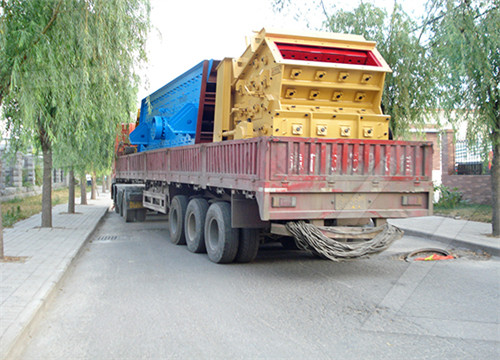
The six main steps of iron ore processing Multotec
The six main steps of iron ore processing When iron ore is extracted from a mine, it must undergo several processing stages. Six steps to process iron ore 1. Screening We
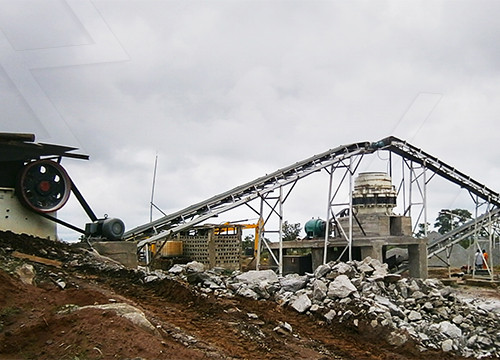
Iron Ore Processing Prominer (Shanghai) Mining
Iron ore is the key raw material for steel production enterprises. Generally, iron ore with a grade of less than 50% needs to be processed before smelting and utilization. After crushing, grinding, magnetic separation,
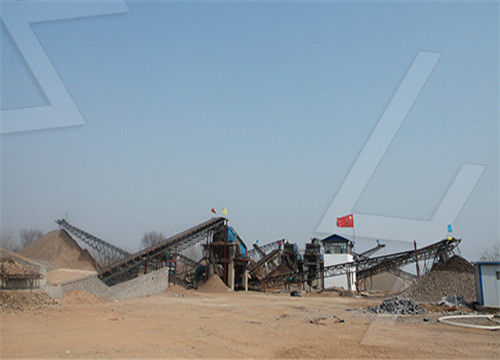
Iron Ore: From Mining to Processing to Dust Control
Iron ore is a rock or mineral from which metallic iron can be extracted economically. It constitutes 5% of the earth’s crust. Viable forms of ore contain between 25% and 60% iron. Ore greater than 60% iron is
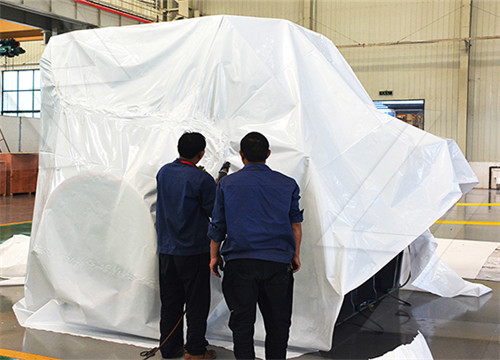
Beneficiation of Iron Ore Mineral ProcessingMetallurgy
2016年5月24日The Iron Ore Process Flowsheet The iron ore beneficiation flowsheet presented is typical of the large tonnage magnetic taconite operations. Multi-parallel circuits are necessary, but for
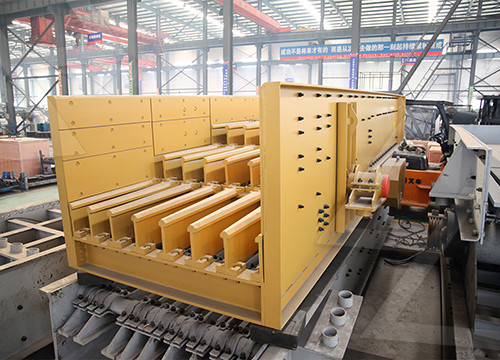
Dry beneficiation of iron ore Mineral Processing
The haematite ore in South Africa is processed in a dry process to a HQ lump ore with 64 % iron content and a sintered fine ore with 63.5 % iron content. For fine ore
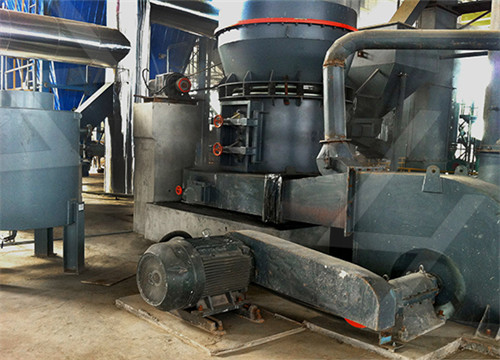
Iron processing Iron making Britannica
The primary objective of iron making is to release iron from chemical combination with oxygen, and, since the blast furnace is much the most efficient process, it receives the most attention here. Alternative
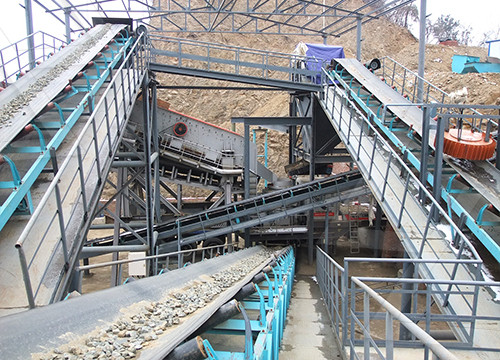
Iron processing Ores Britannica
Iron ore sintering consists of heating a layer of fines until partial melting occurs and individual ore particles fuse together. For this purpose, a traveling-grate machine is used, and the burning of fine coke (known as coke breeze)
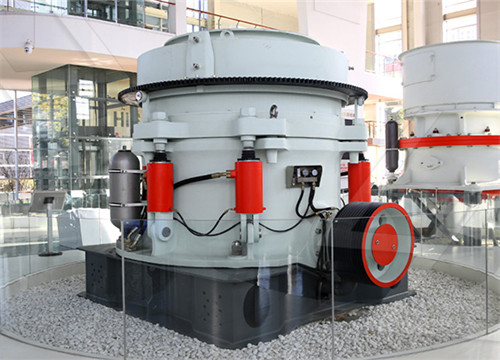
Sintering: A Step Between Mining Iron Ore and
2019年6月11日The USGS defines iron ore as a mineral substance which, when heated in the presence of a reductant, will yield metallic iron (Fe). It almost always consists of iron oxides, the primary forms of which are
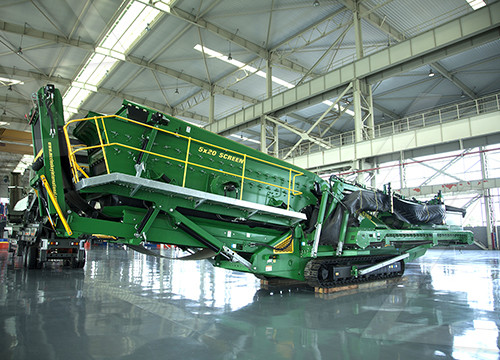
Making steel ArcelorMittal
Making steel. Steel is made from iron ore, a compound of iron, oxygen and other minerals that occurs in nature. The raw materials for steelmaking are mined and then transformed into steel using two different processes: the blast furnace/basic oxygen furnace route, and the electric arc furnace route. Both processes are being continually improved
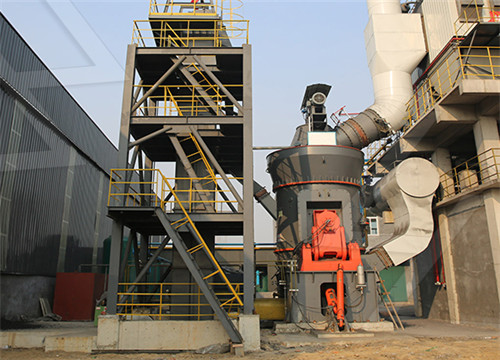
The six main steps of iron ore processing Multotec
The six main steps of iron ore processing When iron ore is extracted from a mine, it must undergo several processing stages. Six steps to process iron ore 1. Screening We recommend that you begin by screening the iron ore to separate fine particles below the crusher’s CSS before the crushing stage.
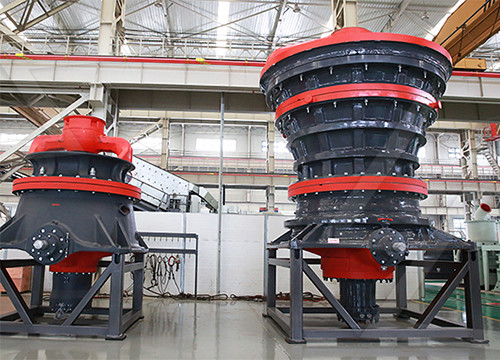
Iron Ore ScienceDirect
Description. Iron Ore: Mineralogy, Processing and Environmental Issues summarizes recent, key research on the characterization of iron ores, including important topics such as beneficiation (separation and refining), agglomeration (e.g., production of pellets or powders), blast furnace technology for smelting, and environmental issues relating
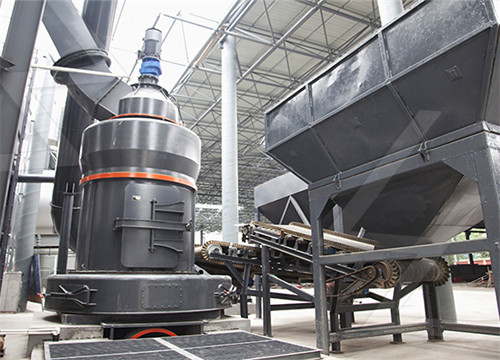
Iron Ore production in the Pilbara Rio Tinto
Process Processing of the ore ranges from simple crushing and screening to a standard size, through to processes that beneficiate or upgrade the quality of the iron ore products. This is done by physical processes, which remove impurities by differences in particle density or size gravity or size separation. Processing may be wet or dry.
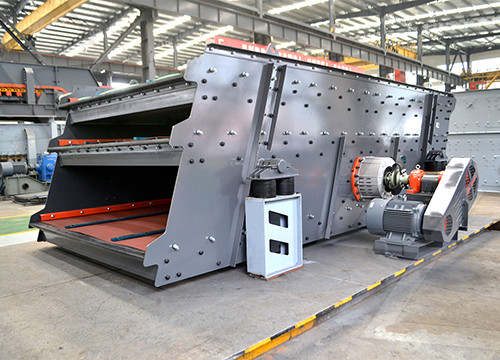
Dry beneficiation of iron ore Mineral Processing
The haematite ore in South Africa is processed in a dry process to a HQ lump ore with 64 % iron content and a sintered fine ore with 63.5 % iron content. For fine ore beneficiation, wet processes are used. Capacity at the Minas Rio is to be increased from 26.5 Mta capacity to 28 Mta in the forthcoming years.
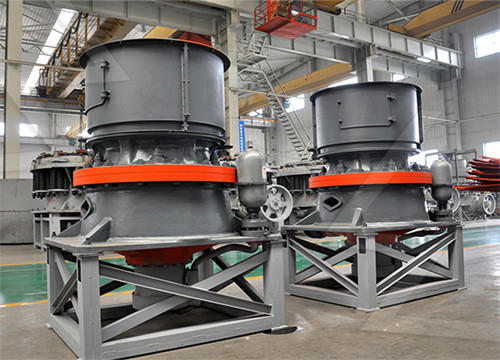
Non-isothermal reduction kinetics of low-grade iron ore-coal mini
A more accurate measure for iron phase distribution in this ore was carried out via chemical phase dissolution and the result is presented in Table 3.Hematite accounts for 90.67 % of the total iron content in the iron element, followed by martite, ferrosilite and magnetite, which is consistent with Table 2.In addition, the process mineralogy analysis results
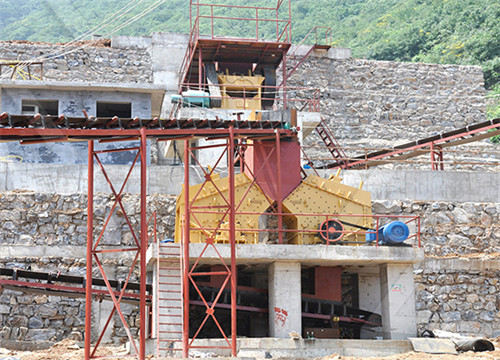
Beneficiation of Iron Ore Mineral Processing
2016年5月24日The Iron Ore Process Flowsheet The iron ore beneficiation flowsheet presented is typical of the large tonnage magnetic taconite operations. Multi-parallel circuits are necessary, but for
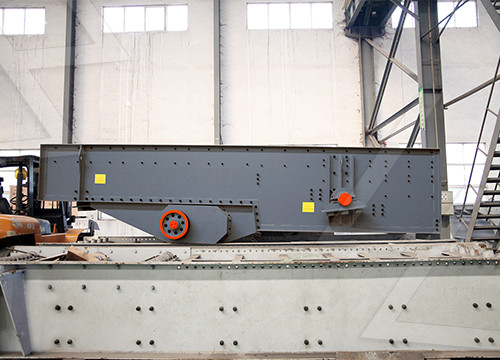
Iron Ore 2nd Edition Elsevier
2021年12月2日Description Iron Ore: Mineralogy, Processing and Environmental Sustainability, Second Edition covers all aspects surrounding the second most important commodity behind oil. As an essential input for the production of crude steel, iron ore feeds the world's largest trillion-dollar-a-year metal market and is the backbone of the global
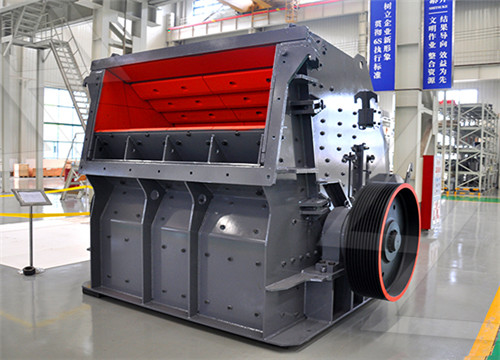
Deep Learning Approach at the Edge to Detect Iron Ore Type
There is a constant risk of iron ore collapsing during its transfer between processing stages in beneficiation plants. Existing instrumentation is not only expensive but also complex and challenging to maintain. In this research, we propose using edge artificial intelligence for early detection of landslide risk based on images of iron ore transported
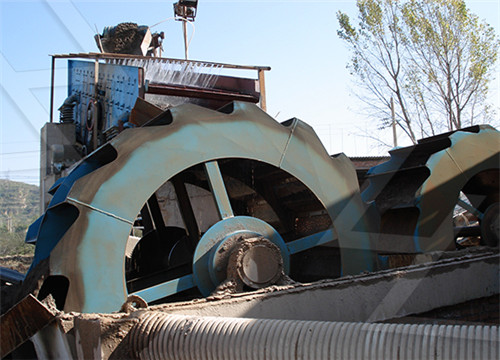
Fulltext 01 13 More details on chem Development of a Process
Crude ore Additives Sorted ore Iron ore pellet Slurry Water Bi-products Iron ore pellet sections handling the magnetite flow and one section handle the hematite flow. Together with the hematite flow, a small amount of magnetite is included, so before further processing, the magnetite needs to be separated from the hematite.
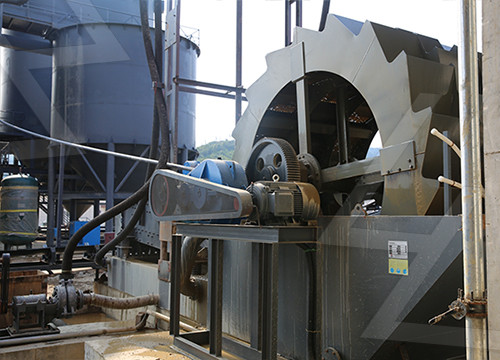
Iron Ore: From Mining to Processing to Dust Control
Iron ore is a rock or mineral from which metallic iron can be extracted economically. It constitutes 5% of the earth’s crust. Viable forms of ore contain between 25% and 60% iron. Ore greater than 60% iron is known as natural ore or direct shipping ore, meaning it can be fed directly into iron-making blast furnaces.
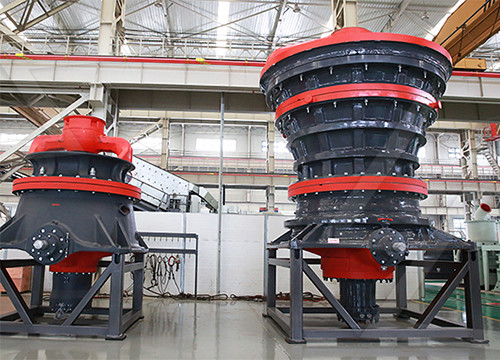
Iron processing Iron making Britannica
This is any process in which iron is extracted from ore at a temperature below the melting points of the materials involved. Gangue remains in the spongelike product, known as direct-reduced iron, or DRI, and must be
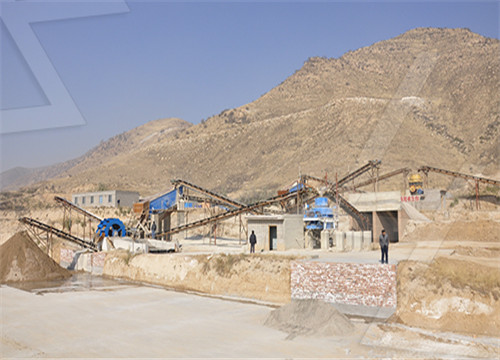
Blast furnace Definition, Temperature, Diagrams,
2023年1月31日The iron oxides in the ore are chemically reduced to molten iron by carbon and carbon monoxide from the coke. The slag formed consists of the limestone flux, ash from the coke, and substances formed
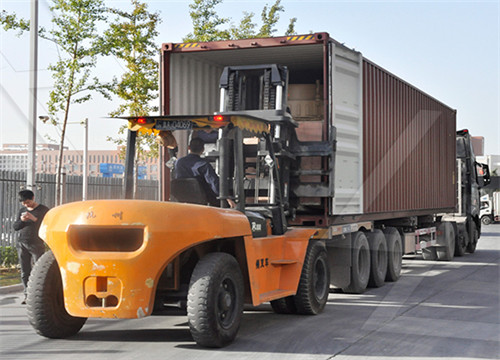
Sintering: A Step Between Mining Iron Ore and
2019年6月11日The USGS defines iron ore as a mineral substance which, when heated in the presence of a reductant, will yield metallic iron (Fe). It almost always consists of iron oxides, the primary forms of which are
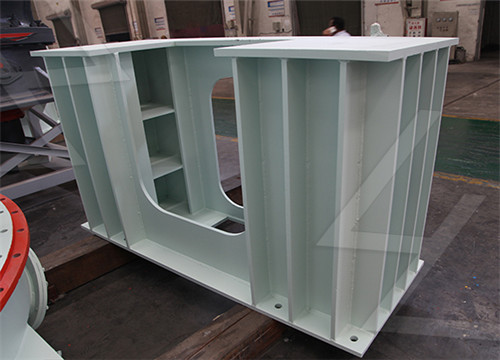
Making steel ArcelorMittal
Making steel Steel is made from iron ore, a compound of iron, oxygen and other minerals that occurs in nature. The raw materials for steelmaking are mined and then transformed into steel using two different processes: the blast furnace/basic oxygen furnace route, and the electric arc furnace route.
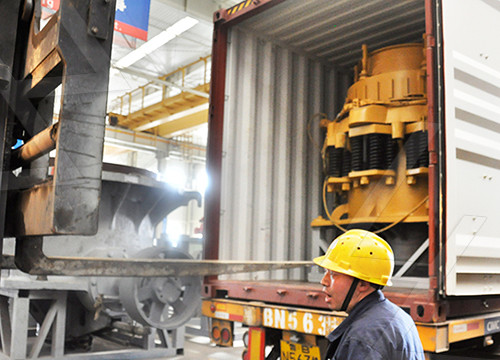
Iron Ore an overview ScienceDirect Topics
Iron ore production by ore type since 1965 is illustrated in Fig. 22.8. Since 1970s, total iron ore production has grown, whereas the production of Premium BM ore has remained steady since 1973. The development of MM and CID can also be clearly distinguished at an increasing rate up to present.
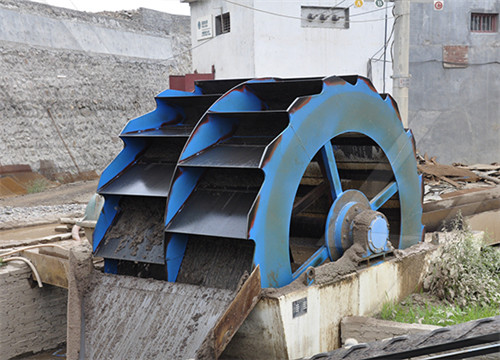
Blast furnace Simple English Wikipedia, the free encyclopedia
The process of making iron is simple. Iron ore is basically iron oxide. Iron is made by removing the oxygen. This leaves crude iron called pig iron. This process of removing oxygen is called smelting. Carbon is used in the reduction process, with the ore heated to a high temperature. Carbon easily takes the oxygen off the ore in high temperatures.
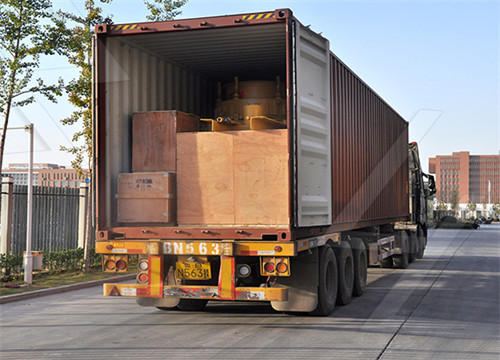
The six main steps of iron ore processing Multotec
The six main steps of iron ore processing When iron ore is extracted from a mine, it must undergo several processing stages. Six steps to process iron ore 1. Screening We recommend that you begin by screening the iron ore to separate fine particles below the crusher’s CSS before the crushing stage.
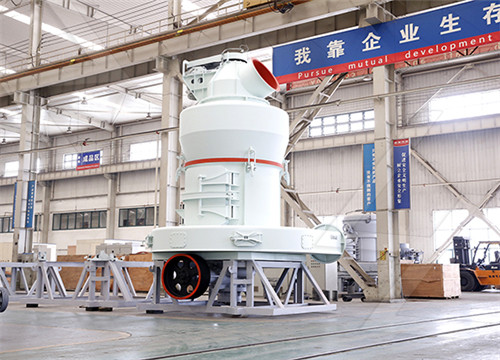
Iron Ore ScienceDirect
Iron ore is the primary raw material from which metallic iron is extracted to make steel. The rapid increase in crude steel production in the last decade has seen major expansions in world iron ore production from around 1 billion tonnes (Bt) in 2001 to over 2.9 Bt in 2012.
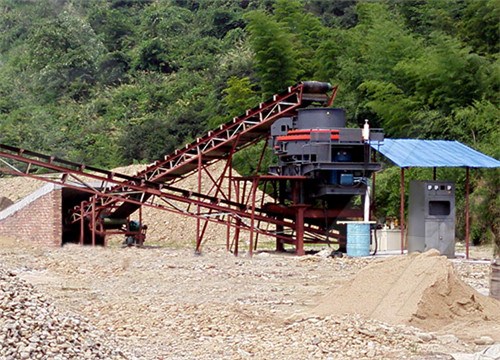
Iron Ore production in the Pilbara Rio Tinto
Process Processing of the ore ranges from simple crushing and screening to a standard size, through to processes that beneficiate or upgrade the quality of the iron ore products. This is done by physical processes, which remove impurities by differences in particle density or size gravity or size separation. Processing may be wet or dry.
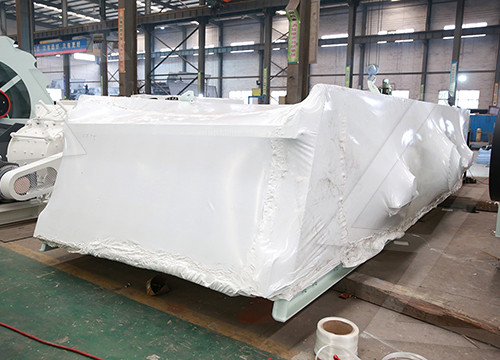
Dry beneficiation of iron ore Mineral Processing
The haematite ore in South Africa is processed in a dry process to a HQ lump ore with 64 % iron content and a sintered fine ore with 63.5 % iron content. For fine ore beneficiation, wet processes are used. Capacity at the Minas Rio is to be increased from 26.5 Mta capacity to 28 Mta in the forthcoming years.
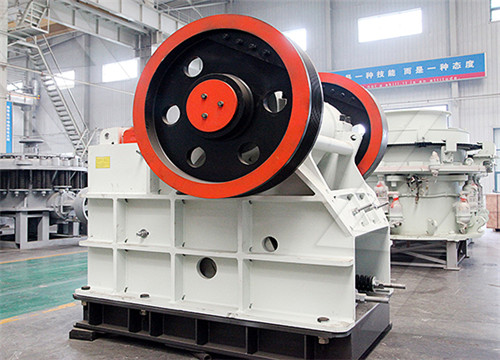
Deep Learning Approach at the Edge to Detect Iron Ore Type
There is a constant risk of iron ore collapsing during its transfer between processing stages in beneficiation plants. Existing instrumentation is not only expensive but also complex and challenging to maintain. In this research, we propose using edge artificial intelligence for early detection of landslide risk based on images of iron ore transported

Mining of Iron Ores IspatGuru
2014年3月14日Processing of the ore ranges from simple crushing and screening and separating various size fractions of the ore to the processes that beneficiate or upgrade the quality of the iron ore products. This is done by physical processes, which remove impurities by difference in particle density or size gravity or size separation.
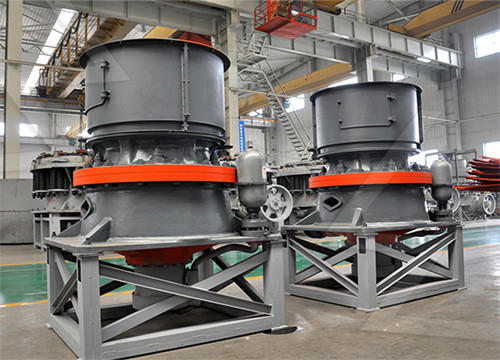
Iron Ore: From Mining to Processing to Dust Control
Iron ore is a rock or mineral from which metallic iron can be extracted economically. It constitutes 5% of the earth’s crust. Viable forms of ore contain between 25% and 60% iron. Ore greater than 60% iron is known as natural ore or direct shipping ore, meaning it can be fed directly into iron-making blast furnaces.
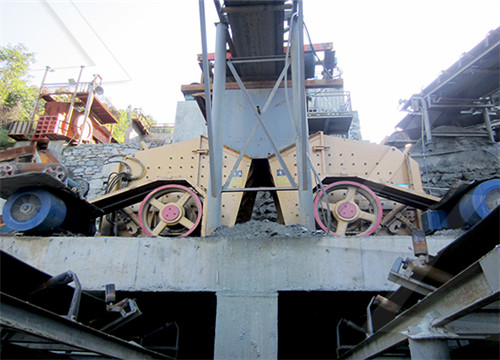
Fulltext 01 13 More details on chem Development of a Process
Crude ore Additives Sorted ore Iron ore pellet Slurry Water Bi-products Iron ore pellet sections handling the magnetite flow and one section handle the hematite flow. Together with the hematite flow, a small amount of magnetite is included, so before further processing, the magnetite needs to be separated from the hematite.