Iron Ore Secondary Thickeners Particle Size
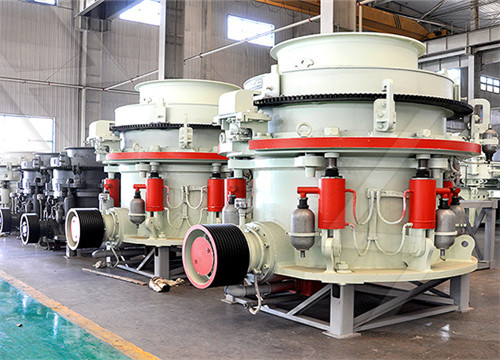
Specifications guide Iron ore S&P Global
Granular size of up to 10 mm for up to 90% of cargo min 50,000 mt CFR Qingdao, China 14-56 days forward L/C at sight $/dmt TSI Iron Ore Fines 62% Fe CFR China TS01021 TSMAU03 TSMBY03 Assessment Daily Iron Ore Silica Differential per 1% with 4.5
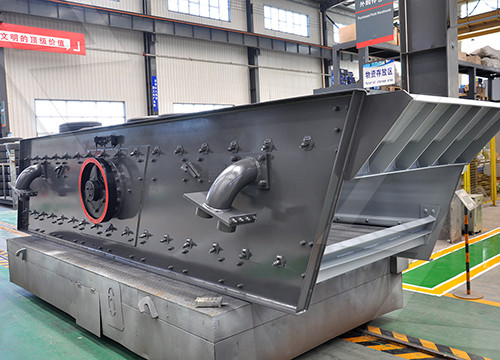
进一步探索
Specifications of iron ores required by steel plants for ironSpecifications Guide Global Iron Ore根据热度为您推荐•反馈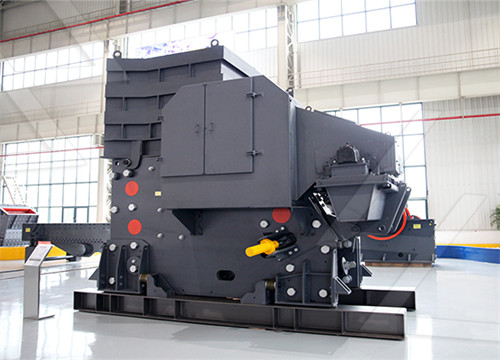
Beginners guide to thickeners Metso Outotec
根据热度为您推荐•反馈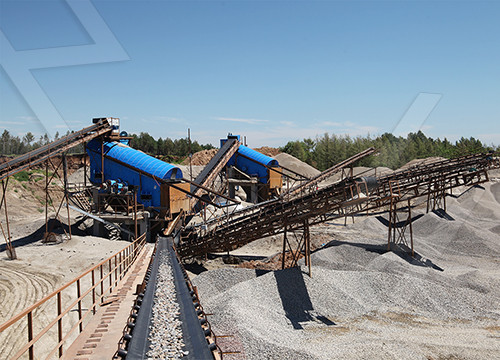
Iron Ore Concentrate Particle Size Controlling Through
2018年10月8日Nowadays, the HPGR (high-pressure grinding rolls) is an intermediate step between filtering and balling in the most modern iron ore pelletizing operation. The operation debottlenecks filtering process and reduces pressure over the typical milling
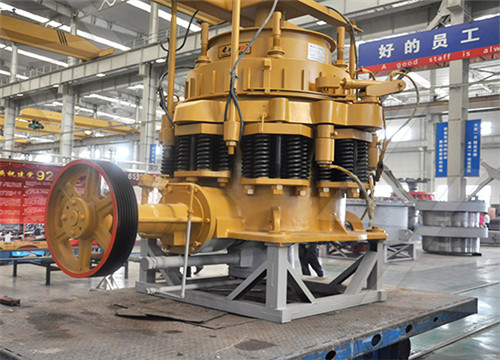
Improving flocculation and dewatering performance of
2019年10月1日In this plant 700 t/h ore (containing 51% iron) is treated to produce 350–400 t/h concentrate with iron contents of 63%. The tailing of the iron ore beneficiation plant (containing 17% iron) at a mass flow rate of 300–350 t/h in slurry form with 5–8%
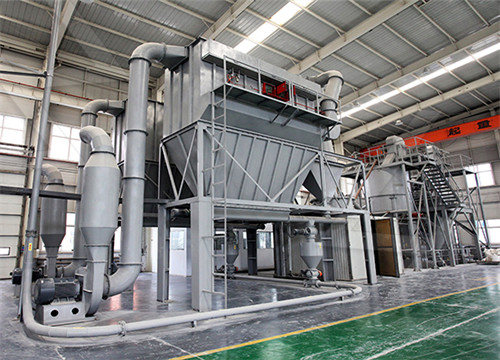
Effects of Particle Size and Particle Loading on the
2017年1月12日Figures 4a, b, and c show results of the tensile strength versus the volume content of iron ore tailings in PP at particle sizes of 150, 212, and 300 μm, respectively. It can be seen in Figs. 4a, b, and c that there was a decrease in the theoretical tensile
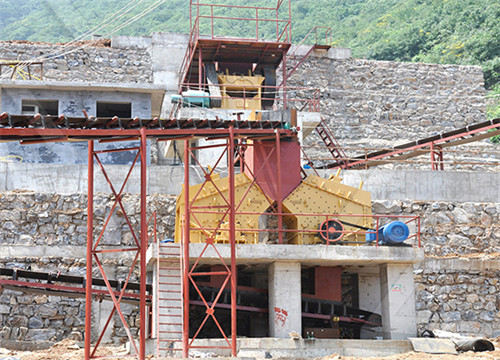
Specifications guide Iron ore S&P Global
Granular size of up to 10 mm for up to 90% of cargo min 50,000 mt CFR Qingdao, China 14-56 days forward L/C at sight $/dmt TSI Iron Ore Fines 62% Fe CFR China TS01021 TSMAU03 TSMBY03 Assessment Daily Iron Ore Silica Differential per 1% with 4.5-6.5% (60-63.5% Fe Fines) IOPPS10 Assessment Daily PMA1105 1% silica within 4.5-6.5%
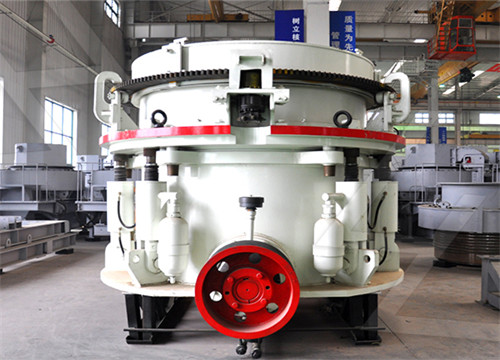
Improving flocculation and dewatering performance of iron
2019年10月1日The mineralogical analysis shows that the major iron-bearing minerals are hematite followed by goethite. The main gangue minerals identified are quartz, chlorite, calcite and dolomite. The particle size analysis showed that d80, d 50, and d 20 of the sample are 31, 16 and 6.5 μm, respectively. Table 2.
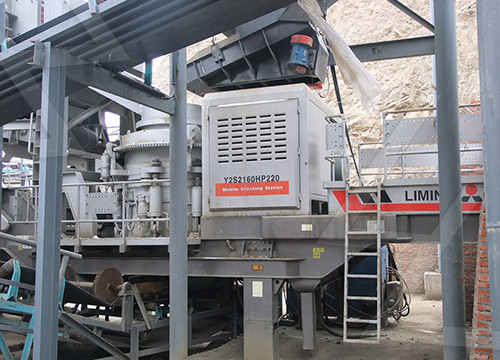
Effects of Particle Size and Particle Loading on the SpringerLink
2017年1月12日Figures 4a, b, and c show results of the tensile strength versus the volume content of iron ore tailings in PP at particle sizes of 150, 212, and 300 μm, respectively. It can be seen in Figs. 4a, b, and c that there was a decrease in the theoretical tensile strength with increasing content of iron ore tailings. In the case of the Pukánszky curve, a
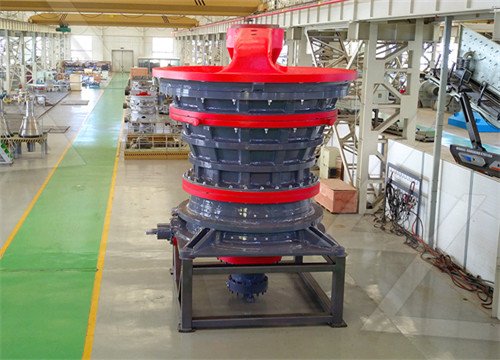
Iron Ore Concentrate Particle Size Controlling Through
2018年10月8日Nowadays, the HPGR (high-pressure grinding rolls) is an intermediate step between filtering and balling in the most modern iron ore pelletizing operation. The operation debottlenecks filtering process and reduces pressure over the typical milling process to control particle size to the balling. The present study evaluated aspects of
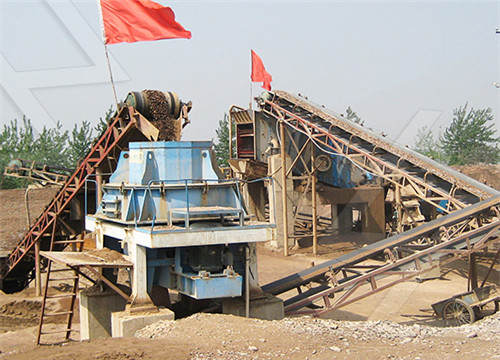
The particle size distribution analysis of the iron ore
The particle size has a significant influence on the rate of reduction. Industrial iron ore concentrate should have a maximum particle size of 106 microns [28], providing a minimum surface area of
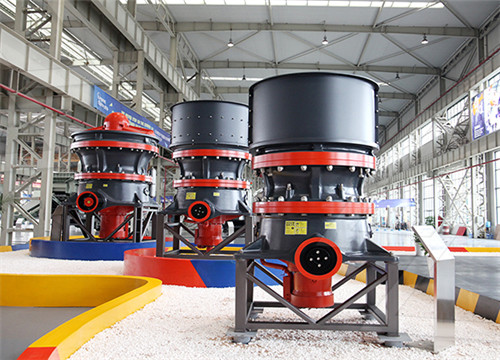
Effect of particle size, blend ratio and some selective
The average true density of the iron ore sample determined by laboratory tests was found to be 4,508 kg/m3. Three representative iron ore samples with monomodal, bimodal and multimodal characteristics were prepared from the aforementioned three distinct particle size ranges and labelled as S-1, S-2 and S-3.
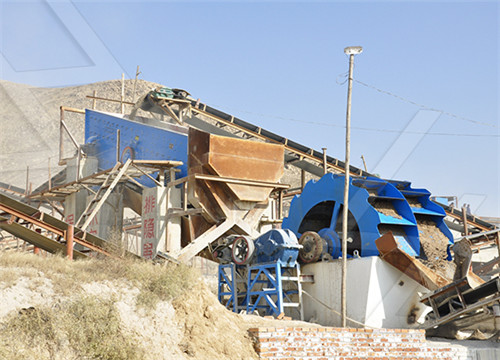
The effect of particle size on green pellet properties
2017年1月1日Effect of particle size on pellet quality during pellet making has also been aimed and studied along with the development of flowsheet for beneficiation of low grade iron ore. SEM analysis
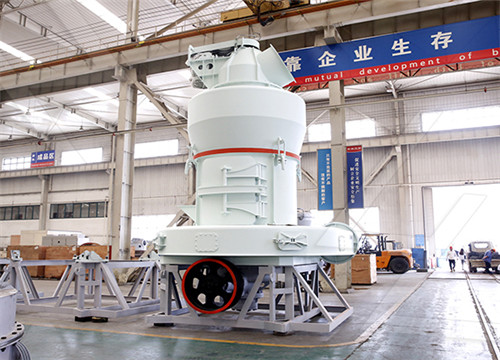
Some opportunities to increase performance of tailing
1.2. Tailing dewatering of Gol-E-Gohar Iron Complex (line 5, 6, 7) Thickeners with a diameter of 28m are used for the dewatering of tailings. Thickener overflow water is used as recycled water in the plant, thickener underflow stream is
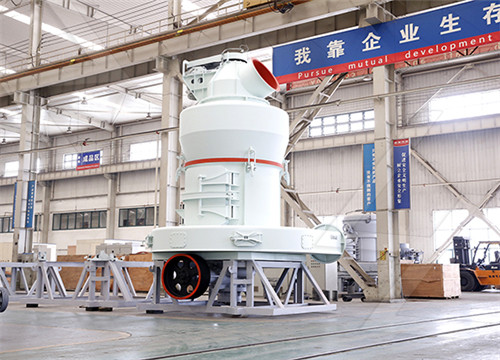
Compression settlement method for promoting accelerated
The invention provides a compression settlement method for promoting accelerated settlement of iron ore tailings, and is applied to the settlement clarification process of the iron ore tailings. Whenthe iron ore tailings settle in a thickener, superfine tailings particles form floccules and settle down under the action of a flocculating agent, the density of the
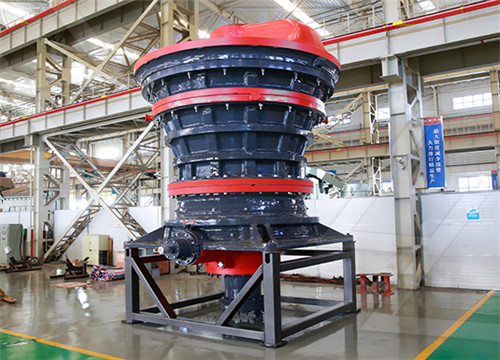
Automated Optical Image Analysis of Iron Ore Sinter
Sinter quality is a key element for stable blast furnace operation. Sinter strength and reducibility depend considerably on the mineral composition and associated textural features. During sinter optical image analysis (OIA), it is important to distinguish different morphologies of the same mineral such as primary/secondary hematite, and types of
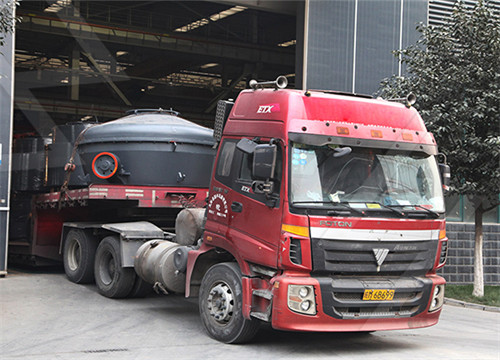
Paste Thickening Iron Ore Tailings PDF Particle Size Scribd
Pilot scale paste thickener tests on iron ore tailings produced underflow solids ranging from 55 to 80 wt% depending on the particle size distribution of the solids and thickener operating conditions. Deposition tests produced non-settling tailings with slopes ranging from 2
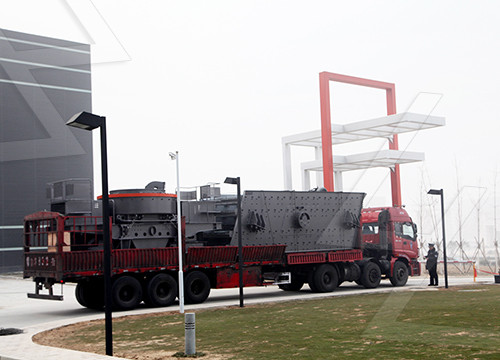
Thickeners Solid Liquid Separation
The high time for thickeners was in the 60's when the metallurgical industries were booming and sizes of up to 150 m diameter were constructed. Such jumbo thickeners, when centrally driven, require for most demanding applications extra heavy duty drive heads some of which reach a continuous operating torque of 3.300.000 Nm.
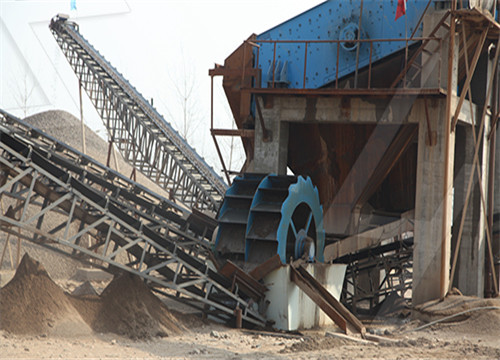
THE EFFECT OF PARTICLE SIZE ON GREEN PELLET
absorption of 0.03 at a particle size range of 0.02 µm to 2000 µm. The particle size of iron ore concentrate (pellet feed) were carried out by particle size analyzer, are given in Figure 5. Figure 5. Particle size analysis of pellet feed The results indicate that the 100 % passing size of this sample is 75 µm. More than 90%
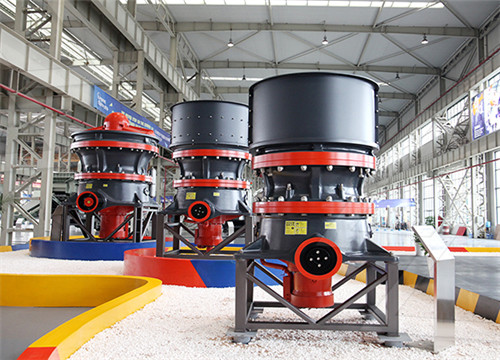
Effect of particle shape on the filtration rate in an industrial iron
2008年8月1日Studies were carried out to determine whether filtration rate changes observed in an iron ore concentrator were due to variations in particle shape. It was confirmed that ores mined from different locations differed in filtration rates by as much as 60%. However, when image analysis was used to quantify the shapes of the individual
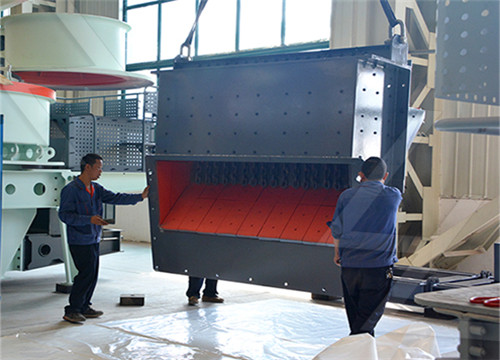
Specifications guide Iron ore S&P Global
Granular size of up to 10 mm for up to 90% of cargo min 50,000 mt CFR Qingdao, China 14-56 days forward L/C at sight $/dmt TSI Iron Ore Fines 62% Fe CFR China TS01021 TSMAU03 TSMBY03 Assessment Daily Iron Ore Silica Differential per 1% with 4.5-6.5% (60-63.5% Fe Fines) IOPPS10 Assessment Daily PMA1105 1% silica within 4.5-6.5%
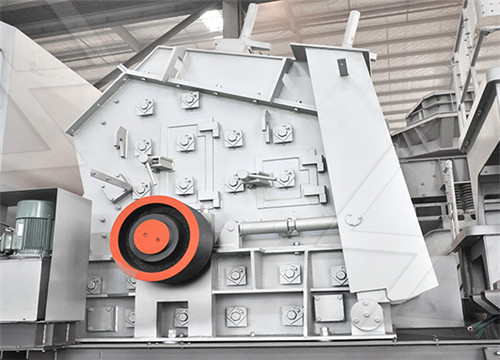
Iron Ore Concentrate Particle Size Controlling Through
2018年10月8日The particle size distribution was performed with a Mastersizer 2000E, capable of analyzing particles between 0.02–1000 μm. Parameters were fixed at a pump speed of 3000 rpm, the measurement time of 6.5 min and pulp concentration of 0.01% w/w. The sample was prepared in distilled water. Specific Surface Area
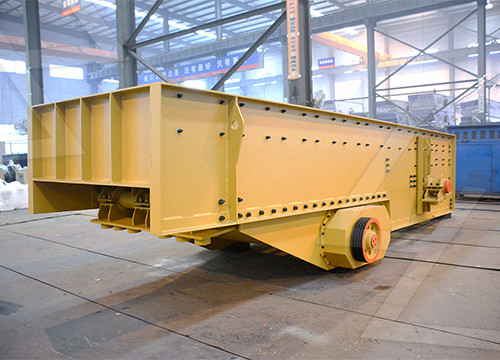
Effects of Particle Size and Particle Loading on the SpringerLink
2017年1月12日Figures 4a, b, and c show results of the tensile strength versus the volume content of iron ore tailings in PP at particle sizes of 150, 212, and 300 μm, respectively. It can be seen in Figs. 4a, b, and c that there was a decrease in the theoretical tensile strength with increasing content of iron ore tailings. In the case of the Pukánszky curve, a
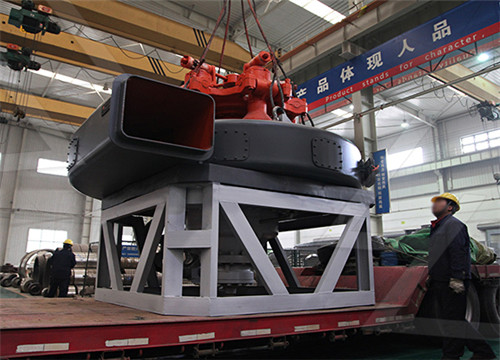
Effect of particle size, blend ratio and some selective
The average true density of the iron ore sample determined by laboratory tests was found to be 4,508 kg/m3. Three representative iron ore samples with monomodal, bimodal and multimodal characteristics were prepared from the aforementioned three distinct particle size ranges and labelled as S-1, S-2 and S-3.
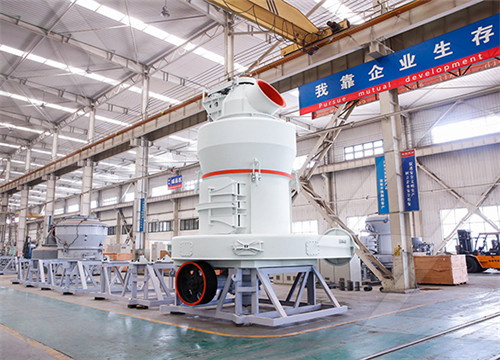
The particle size distribution analysis of the iron ore
The particle size has a significant influence on the rate of reduction. Industrial iron ore concentrate should have a maximum particle size of 106 microns [28], providing a minimum surface area of
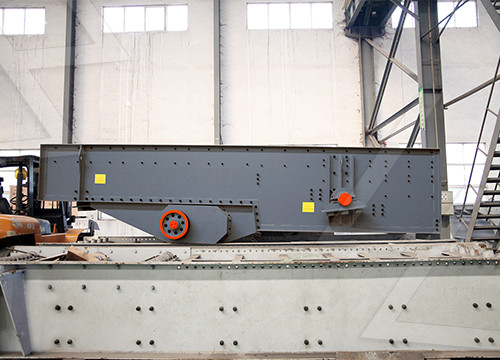
Automated Optical Image Analysis of Iron Ore Sinter
Sinter quality is a key element for stable blast furnace operation. Sinter strength and reducibility depend considerably on the mineral composition and associated textural features. During sinter optical image analysis (OIA), it is important to distinguish different morphologies of the same mineral such as primary/secondary hematite, and types of
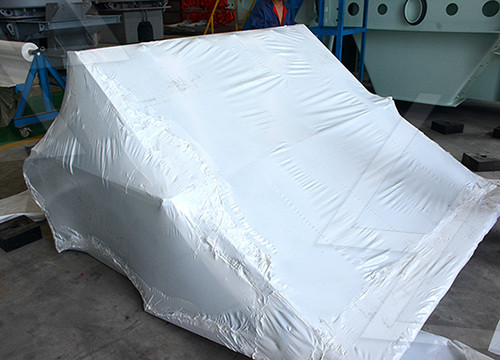
The effect of particle size on green pellet properties
2017年1月1日Effect of particle size on pellet quality during pellet making has also been aimed and studied along with the development of flowsheet for beneficiation of low grade iron ore. SEM analysis
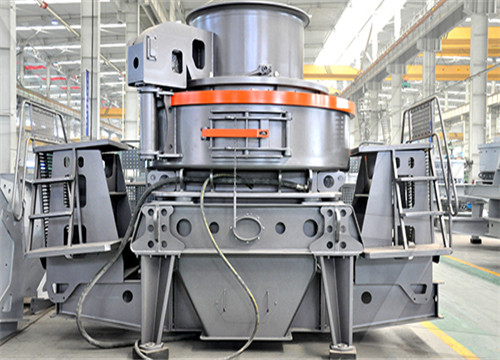
Some opportunities to increase performance of tailing
1.2. Tailing dewatering of Gol-E-Gohar Iron Complex (line 5, 6, 7) Thickeners with a diameter of 28m are used for the dewatering of tailings. Thickener overflow water is used as recycled water in the plant, thickener underflow stream is
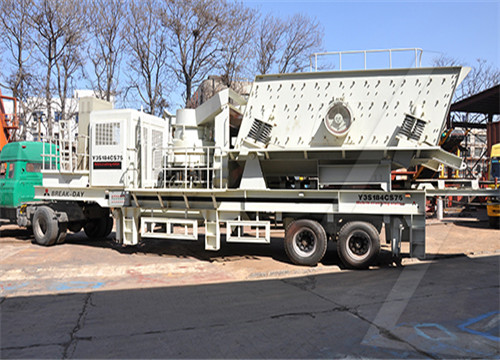
Compression settlement method for promoting accelerated
The invention provides a compression settlement method for promoting accelerated settlement of iron ore tailings, and is applied to the settlement clarification process of the iron ore tailings. Whenthe iron ore tailings settle in a thickener, superfine tailings particles form floccules and settle down under the action of a flocculating agent, the density of the
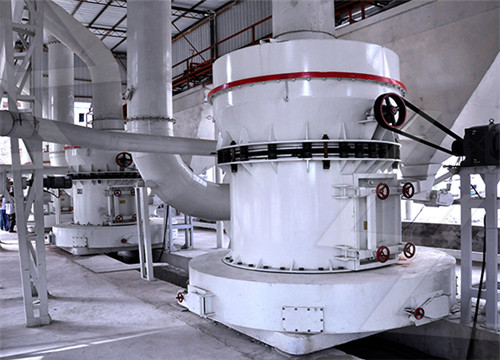
Paste Thickening Iron Ore Tailings PDF Particle Size Scribd
Pilot scale paste thickener tests on iron ore tailings produced underflow solids ranging from 55 to 80 wt% depending on the particle size distribution of the solids and thickener operating conditions. Deposition tests produced non-settling tailings with slopes ranging from 2
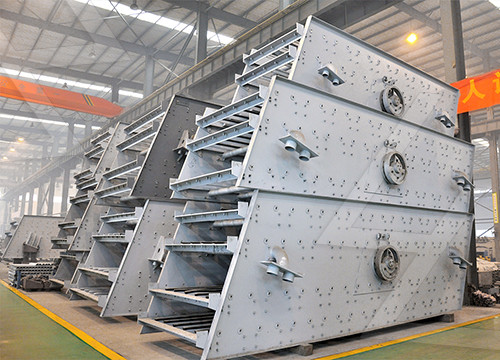
Thickeners Solid Liquid Separation
The high time for thickeners was in the 60's when the metallurgical industries were booming and sizes of up to 150 m diameter were constructed. Such jumbo thickeners, when centrally driven, require for most demanding applications extra heavy duty drive heads some of which reach a continuous operating torque of 3.300.000 Nm.
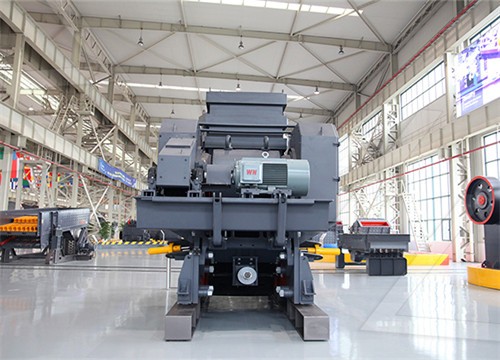
THE EFFECT OF PARTICLE SIZE ON GREEN PELLET
absorption of 0.03 at a particle size range of 0.02 µm to 2000 µm. The particle size of iron ore concentrate (pellet feed) were carried out by particle size analyzer, are given in Figure 5. Figure 5. Particle size analysis of pellet feed The results indicate that the 100 % passing size of this sample is 75 µm. More than 90%
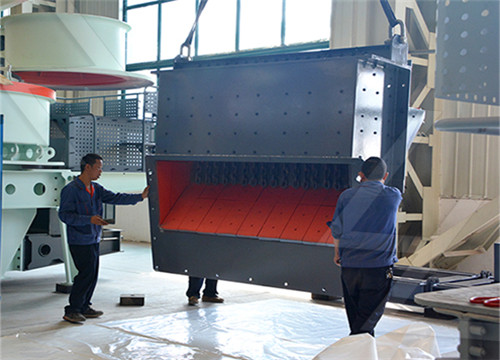
Effect of particle shape on the filtration rate in an industrial iron
2008年8月1日Studies were carried out to determine whether filtration rate changes observed in an iron ore concentrator were due to variations in particle shape. It was confirmed that ores mined from different locations differed in
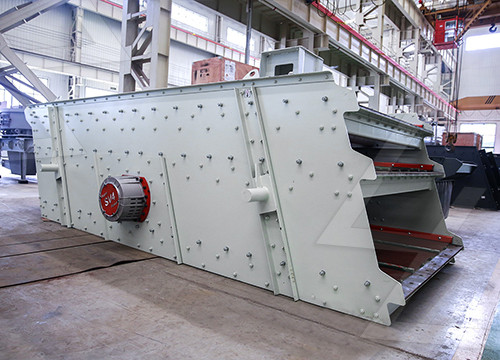
Steel Balls ConsumptionBall Mill Effect JXSC Machine
The ball mill must fully consider the diameter of the ball grinding surface, the strength of the iron ore, the particle size distribution of the iron ore entering the ball mill, the compressive strength of the bearing steel balls, and the speed of the ball mill. Gold Mining Equipment. Chat on WhatsApp; Email Sales Team; Menu.