Iron And Steel Mill Layout Schematics
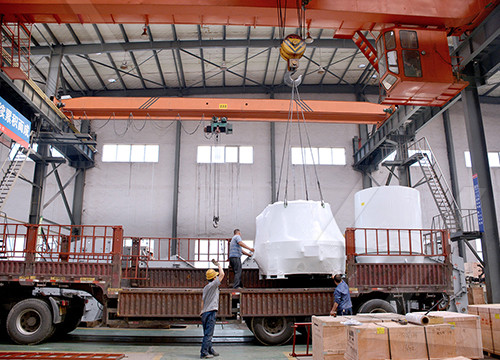
Steel Manufacturing Process AIST
The process starts in the center of the wheel with the three main ingredients of iron in the form of iron ore, coke and lime, which are fed into a blast furnace to produce molten
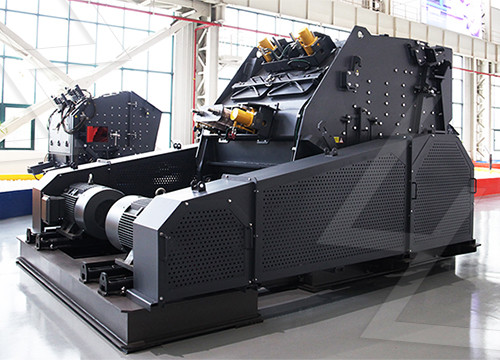
Schematic representation of an Iron and Steel mill.
The iron and steel sector is one of the dominant drivers behind economic and social progress, but it is also very energy-intensive and hard-to-abate, making it a major cause of global warming.
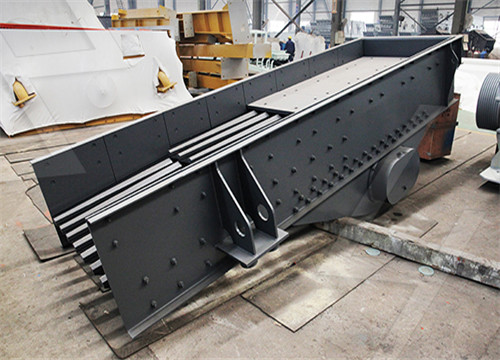
(PDF) iron-steel making From start to finish ResearchGate
2019年12月27日General flow diagram of Iron Steel making process : THEIS range of 0.05 mm to 4.0 mm in verities of steel grades. Hot
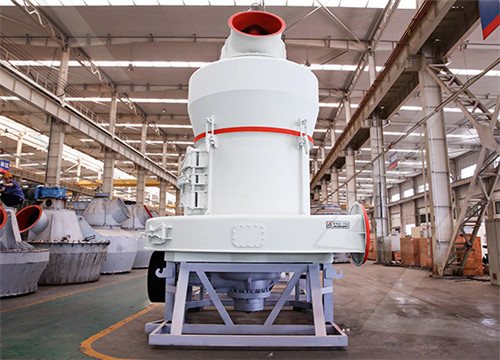
AMIT 135: Lesson 7 Ball MillsCircuits Mining Mill
Mill Type Overview. Three types of mill design are common. The Overflow Discharge mill is best suited for fine grinding to 75 106 microns. The Diaphram or Grate Discharge mill keeps coarse particles within the mill
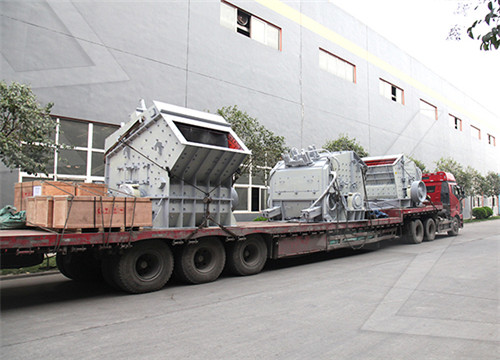
Systematic Planning of General layout of a steel plant
2013年4月1日There are several methods being used for the design of the plant general layout. These include (i) systematic layout planning (SLP), (ii) algorithms, and (iii) arena simulation. SLP method of designing the
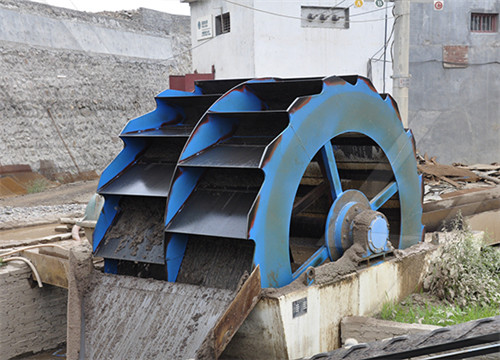
STRUCTURAL STEEL TERMS/ LAYOUT AND
Figure 3-2.—Structural shapes. the S-shape is in the design of the inner surfaces of the flange. The W-shape has parallel inner and outer flange surfaces with a constant
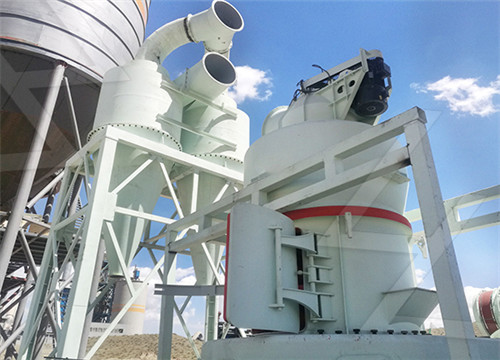
12.5 Iron And Steel Production US EPA
The production of steel at an integrated iron and steel plant is accomplished using several interrelated processes. The major operations are: (1) coke production, (2) sinter
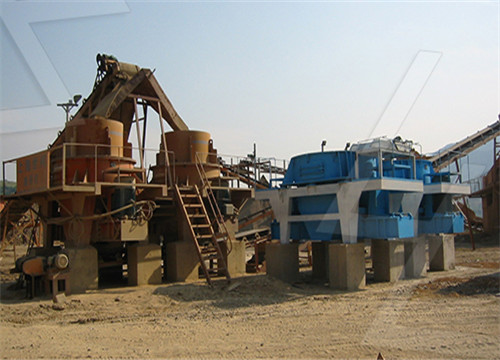
steel mill arrangement Model Railroader Magazine Trains
2010年2月17日My steel mill is based on the origianl four Walthers steel mill kits. The coke oven was modfied to include additional structures, and it is separated from the rest of the
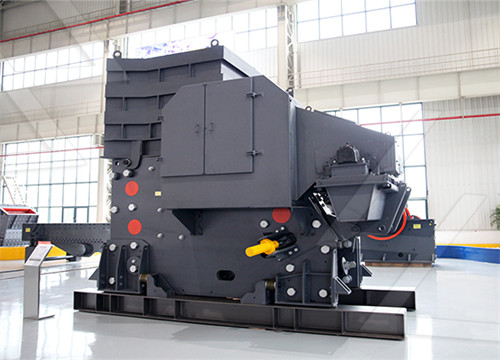
Steel Making Process Complete Overview with
The Bessemer Process. The Bessemer steel making process consists of blowing air through molten pig iron contained in a special furnace known as a converter which shaped like a huge concrete mixer (Fig. 4.2). The
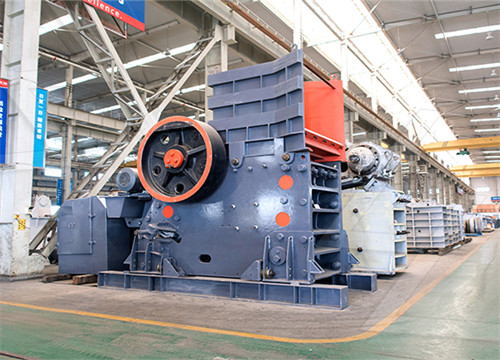
Steel Manufacturing Process AIST
The process starts in the center of the wheel with the three main ingredients of iron in the form of iron ore, coke and lime, which are fed into a blast furnace to produce molten iron. The molten iron is mixed with recycled steel scrap and further processed in a basic oxygen furnace to make steel.
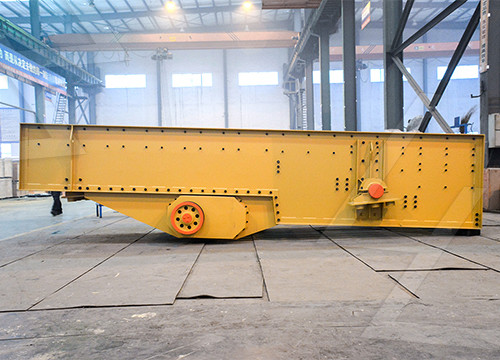
Schematic representation of an Iron and Steel mill.
In the STEPWISE project, the Sorption Enhanced Water-Gas Shift (SEWGS) technology for CO2 capture is brought to TRL6 by means of design, construction, operation and modelling a pilot installation...
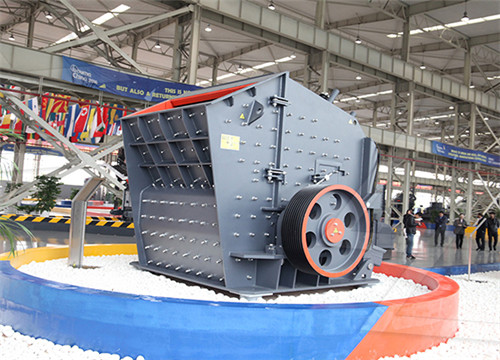
STRUCTURAL STEEL DESIGN AND CONSTRUCTION
Structural Shapes standard steel configurations produced by steel mills such as wide flanges, channels, angles, pipe, tubes, etc. Structural Steel the structural elements that make up the frame that are essential to supporting the design loads, e.g. beams, columns, braces, plate, trusses, and fasteners. It does not include for example
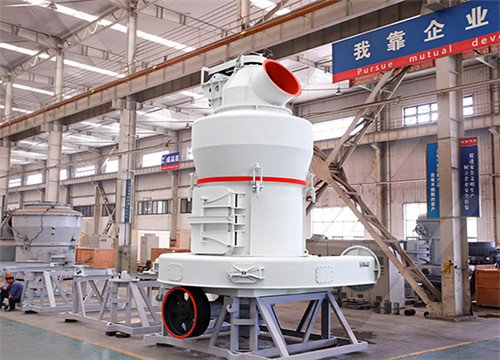
(PDF) iron-steel making From start to finish
2019年12月27日(PDF) iron-steel making From start to finish iron-steel making From start to finish Authors: Mr. Bhavesh R Rana LT Defence 20+ million members 135+ million publications 700k+ research...
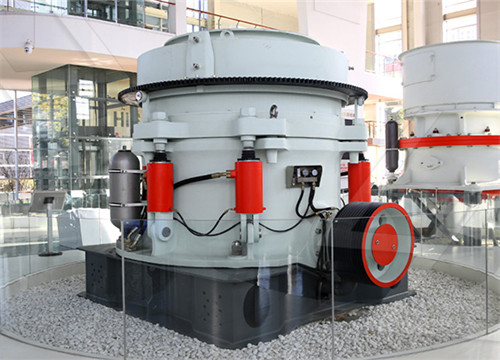
12.5 Iron And Steel Production US EPA
The sintering process converts fine-sized raw materials, including iron ore, coke breeze, limestone, mill scale, and flue dust, into an agglomerated product, sinter, of suitable size for charging General flow diagram for the iron and steel industry. 12.5-2 EMISSION FACTORS (Reformatted 1/95) 10/86. pit. At the conclusion of the cast, the
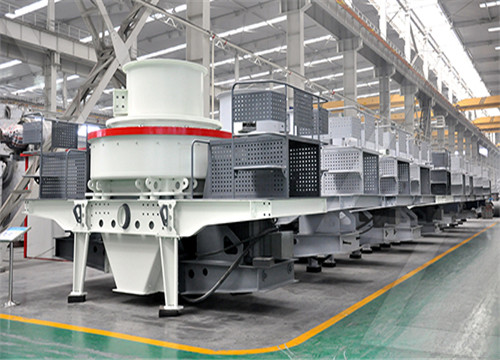
AMIT 135: Lesson 7 Ball MillsCircuits Mining
Mill Type Overview. Three types of mill design are common. The Overflow Discharge mill is best suited for fine grinding to 75 106 microns.; The Diaphram or Grate Discharge mill keeps coarse particles within the mill
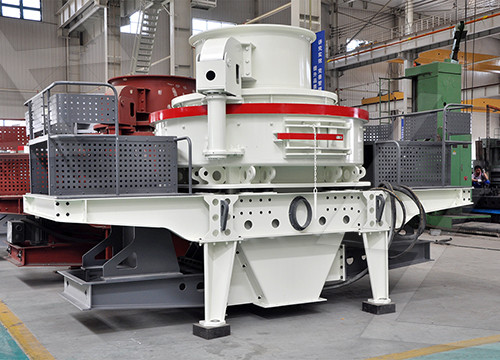
STRUCTURAL STEEL TERMS/ LAYOUT AND FABRICATION OF
Figure 3-10.—Girder span on pipe columns. Figure 3-11.—Built-up column section. such that the joints or splices are 1 1/2 to 2 feet above the second and succeeding story levels.
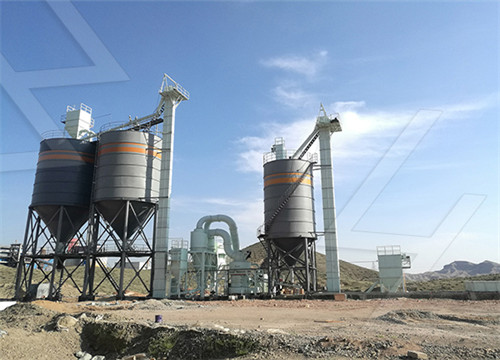
IRON AND STEEL INDUSTRY Case Western Reserve University
In 1979 U.S. Steel abandoned its historic Central Furnaces plant, established by the Cleveland Rolling Mill Co. in 1881 for the production of pig iron. Five years later, the steel giant closed 6 plants, including its Cuyahoga Works in Cuyahoga Heights, after the United Steelworkers of America rejected concessions demanded by the company.
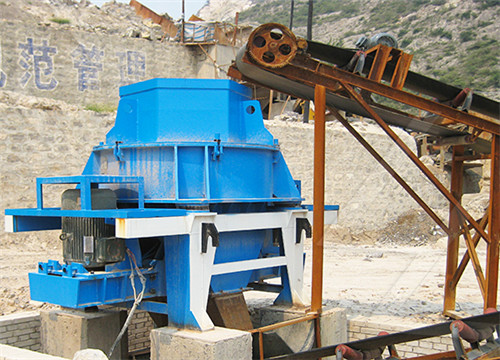
Steel Pickling: The Essential Guide MachineMfg
2023年3月4日Fig.2 Production line layout diagram of full continuous pickling unit. As people’s living standards improve, the demand for a cleaner environment is increasing. 2013, with the roll-free pickling coil being

Iron and Steel Manufacturing International Finance
steel plants. See also Coke Manufacturing. In the BOF process, coke making and iron making precede steel making; these steps are not necessary with an EAF. Pig iron is manufactured from sintered, pelletized, or lump iron ores us-ing coke and limestone in a blast furnace. It is then fed to a BOF in molten form along with scrap metal, fluxes
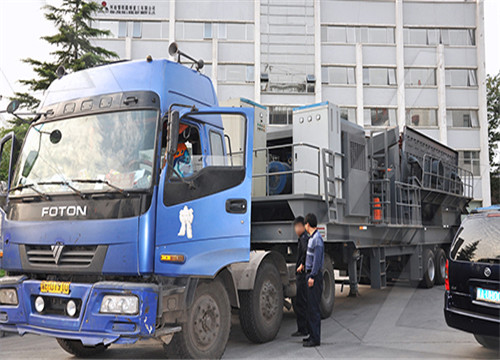
The Use of Hydrogen in the Iron and Steel Industry Energy
decline of the BF method of making iron. • Although still the base source of virgin iron, new blast furnaces have not been built in the U.S. in decades and there are no plans to build one anytime soon. The U.S. steel industry is currently undergoing transformation. 5 THE USE OF HYDROGEN IN THE IRON AND STEEL INDUSTRY BLAST FURNACE
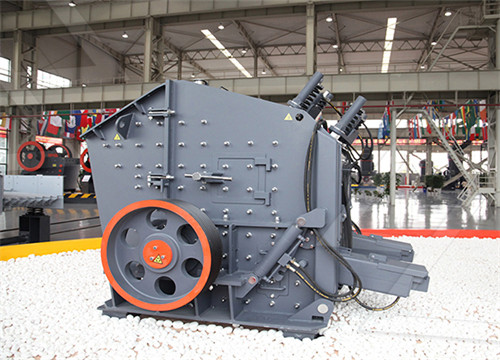
Steel Production American Iron and Steel Institute
Steel Flowlines How Steel Is Made Steel is primarily produced using one of two methods: Blast Furnace or Electric Arc Furnace. The blast furnace is the first step in producing steel from iron oxides. The first blast furnaces appeared in
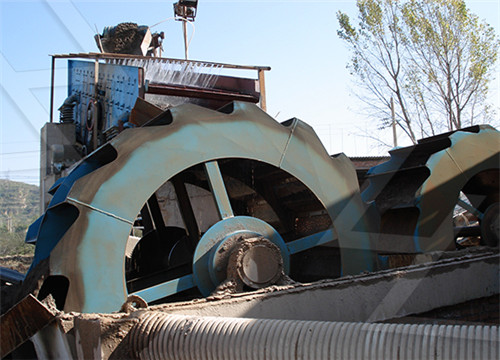
Rolling of Steel in a Modern Long Product Rolling Mill
2017年6月19日Wire rod mills produces steel wire rods of diameters 5 mm to 12.5 mm in coil form with the weight of the coil upto 2.5 tons. The qualities of steels being rolled in these mills can range from low carbon, mild steel, medium carbon, high carbon, and micro and low alloyed steels.
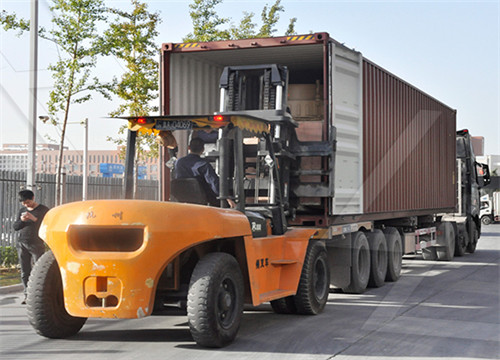
Final Integrated Steel Mills International Finance
INTEGRATED STEEL MILLS APRIL 30, 2007 2 WORLD BANK GROUP 1.0 Industry-Specific Impacts and Management heating furnaces (depending of type of fuels used); mechanical The following section provides a summary of EHS issues associated with steel manufacturing, which occur during the operational phase, along with recommendations
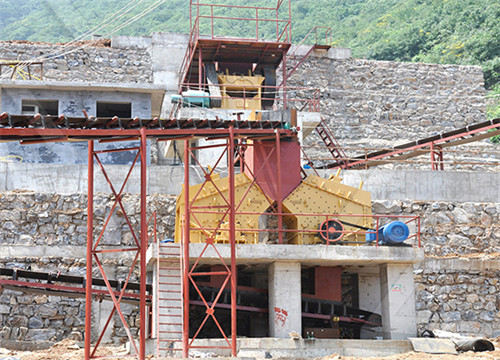
STRUCTURAL STEEL DESIGN AND CONSTRUCTION
Structural Shapes standard steel configurations produced by steel mills such as wide flanges, channels, angles, pipe, tubes, etc. Structural Steel the structural elements that make up the frame that are essential to supporting the design loads, e.g. beams, columns, braces, plate, trusses, and fasteners. It does not include for example
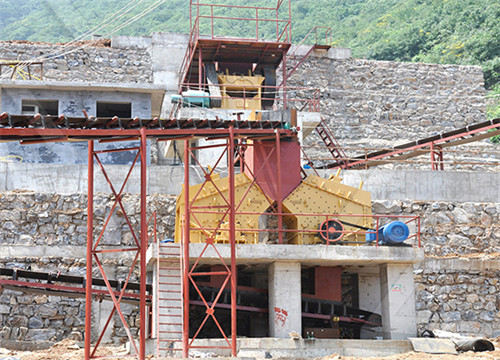
Iron and Steel Manufacturing International Finance
steel plants. See also Coke Manufacturing. In the BOF process, coke making and iron making precede steel making; these steps are not necessary with an EAF. Pig iron is manufactured from sintered, pelletized, or lump iron ores us-ing coke and limestone in a blast furnace. It is then fed to a BOF in molten form along with scrap metal, fluxes
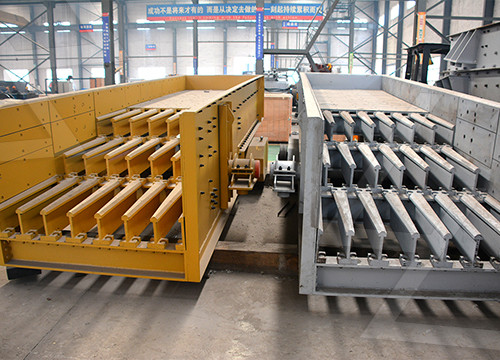
AMIT 135: Lesson 7 Ball MillsCircuits Mining
Mill Type Overview. Three types of mill design are common. The Overflow Discharge mill is best suited for fine grinding to 75 106 microns.; The Diaphram or Grate Discharge mill keeps coarse particles within the mill
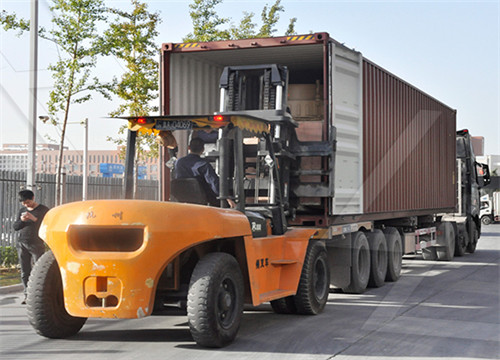
Prefabricated Metal Buildings for Steel Mills Steel
Whether you are producing steel from scrap metal in electric furnaces or hot rolling it for the use in buildings, cars, and appliances, our customizable metal building kits can meet your needs. In addition to being the most
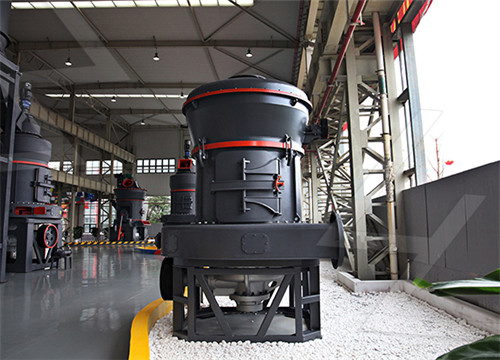
STRUCTURAL STEEL TERMS/ LAYOUT AND FABRICATION OF
Figure 3-10.—Girder span on pipe columns. Figure 3-11.—Built-up column section. such that the joints or splices are 1 1/2 to 2 feet above the second and succeeding story levels.
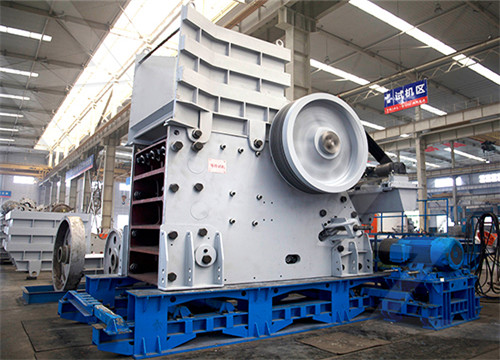
Schematic process layout of the SSAB steel mill.
Schematic process layout of the SSAB steel mill. Process gases and main material used in the system. Energy flows indicated on yearly basis (2006). Source publication Methanol production at...
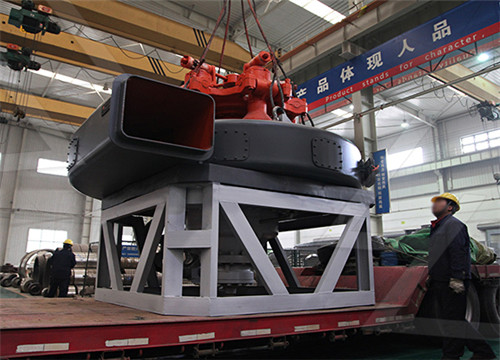
Final Integrated Steel Mills International Finance
INTEGRATED STEEL MILLS APRIL 30, 2007 2 WORLD BANK GROUP 1.0 Industry-Specific Impacts and Management heating furnaces (depending of type of fuels used); mechanical The following section provides a summary of EHS issues associated with steel manufacturing, which occur during the operational phase, along with recommendations
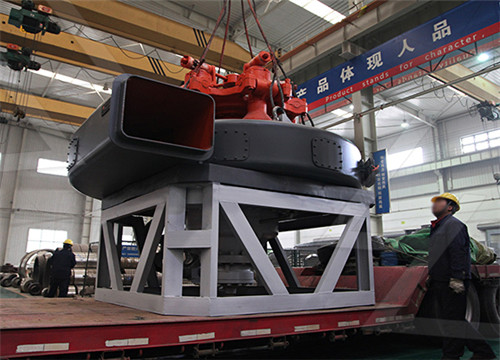
Steel Production American Iron and Steel Institute
Steel Flowlines How Steel Is Made Steel is primarily produced using one of two methods: Blast Furnace or Electric Arc Furnace. The blast furnace is the first step in producing steel from iron oxides. The first blast furnaces
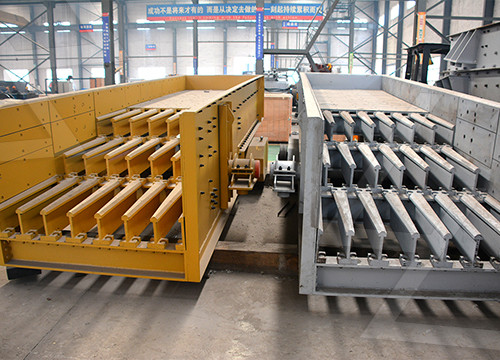
Steel Pickling: The Essential Guide MachineMfg
2023年3月4日At present, there are three main methods for pickling steel in the world: Single-piece steel pickling (steel pickling, single coil pickling, single bundle wire pickling) Continuous pickling Semi-continuous pickling
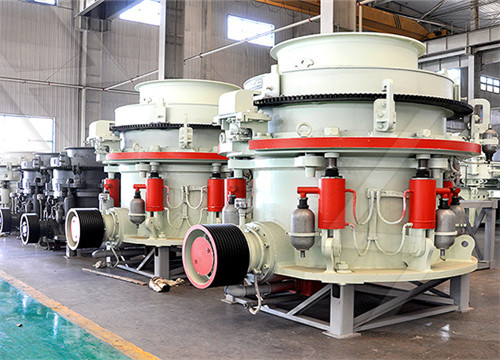
The Use of Hydrogen in the Iron and Steel Industry Energy
decline of the BF method of making iron. • Although still the base source of virgin iron, new blast furnaces have not been built in the U.S. in decades and there are no plans to build one anytime soon. The U.S. steel industry is currently undergoing transformation. 5 THE USE OF HYDROGEN IN THE IRON AND STEEL INDUSTRY BLAST FURNACE
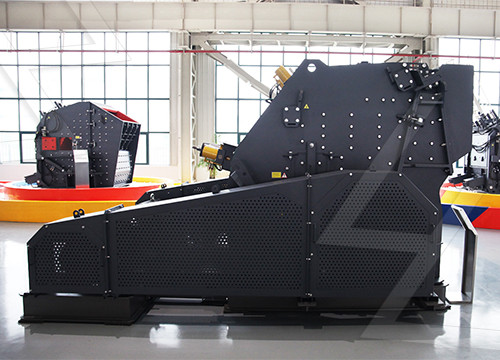
Iron and Steel Mills MCR Safety
The former US president was spot on with this statement. Blast furnaces in steelmaking reach temperatures of 1600°F to 2300°F. For steel to exist, it truly most go through the hottest fire. Steelmaking is the process of
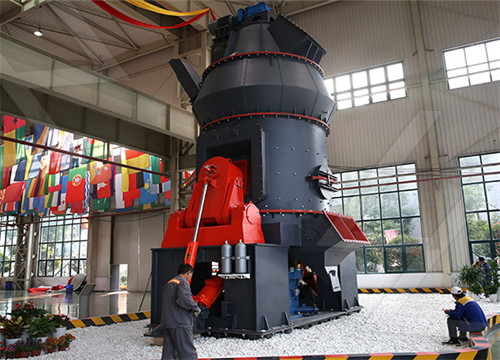
ACT NOx Emissions from IronSteel Mills US EPA
3-2 Schematic representation of progress of refining in a top-blown basic-lined BOF . . . . 3-21 Iron and steel mills have been identified as a stationary source category with emission sources that emit more than 25 tons of nitrogen oxides (NO x ) per year. This alternative control
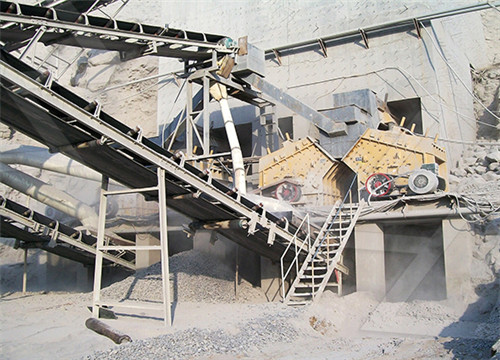
Infographic: the Iron and Steel Manufacturing
2015年6月4日An Infographic of the Iron and Steel Manufacturing Process. Steel production is a 24-hour-a-day, 365-day-a-year process, dependent on a consistent supply of raw materials and huge amounts of
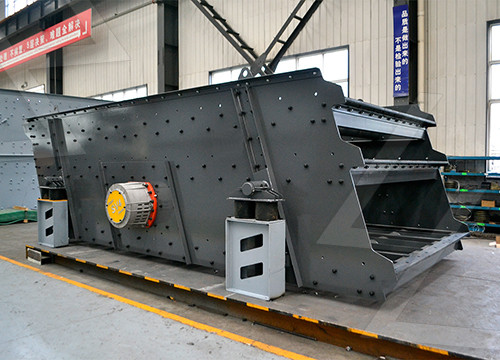
Low-Carbon Production of IronSteel: Technology Options
2021年3月8日A globally traded commodity, iron and steel production has tripled production since 2000, with 2018 seeing $2.5 trillion in sales [(Worldsteel Association, 2019)]. It is also an enormous source of greenhouse gases: today’s iron and steel industry generates roughly 6% of global CO2 emissions (see table 2).