Ball Size For Miling Ore Stirred Ball Mill Of Beneficiation Equipmen
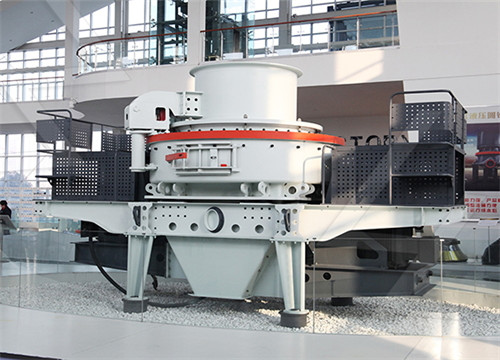
Impact of ball filling rate and stirrer tip speed on milling
2021年1月22日In the size fractions with identical P80, the degree of liberation of the magnetites in the products of stirred milling is greater than that of ball milling, with the
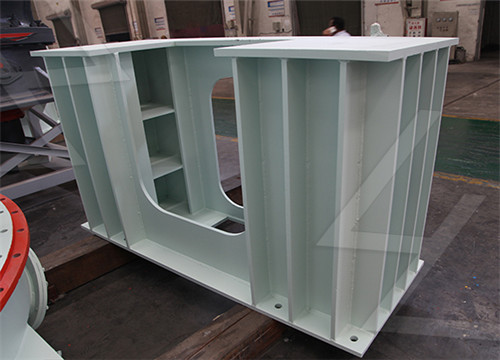
Calculate and Select Ball Mill Ball Size for Optimum Grinding
2013年8月2日Based on his work, this formula can be derived for ball diameter sizing and selection: Dm <= 6 (log dk) * d^0.5 where D m = the
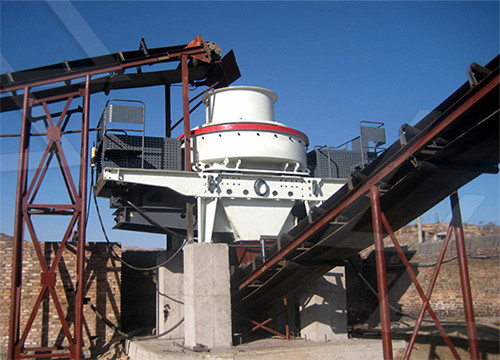
The Effect of Ball Size Diameter on Milling Performance
An investigation was conducted to determine the effect of the ball diameter sizes on milling operation. A laboratory size ball mill was used with ball media of sizes 10 mm, 20 mm
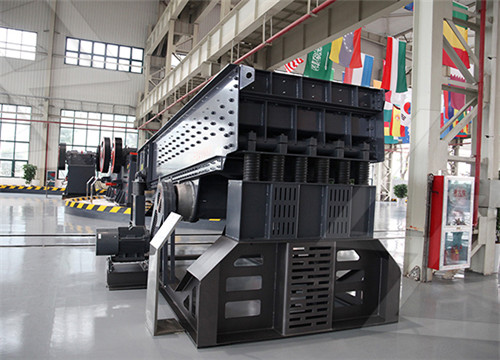
High Energy Ball Milling Union Process
The savings in energy and the increase in grinding efficiency provided by Attritors are substantial. The graph below compares various mills during the high energy ball milling process. Select a link to learn more about these
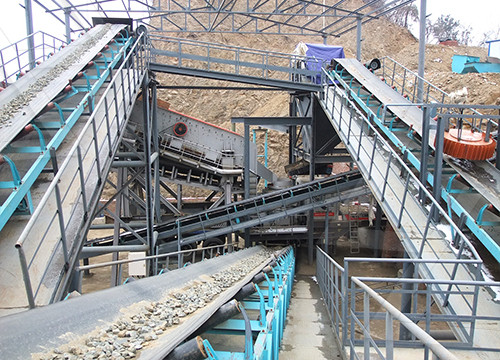
Calculate Top Ball Size of Grinding Media Equation
2015年9月5日Calculate Top Ball Size of Grinding Media -FRED C. BOND EquationMethod. Although it was developed nearly 50 years ago, Bond ‘s method is still useful for calculating necessary mill sizes and power
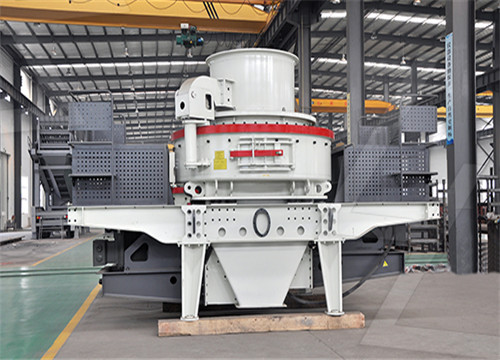
Stirred Milling Technology A New Concept in Fine Grinding
al., 2005). In stirred mills there are no free-falling possibilities for grinding media, meaning that impact action does not occur. The bead size is small, typically 1 to 6 mm which
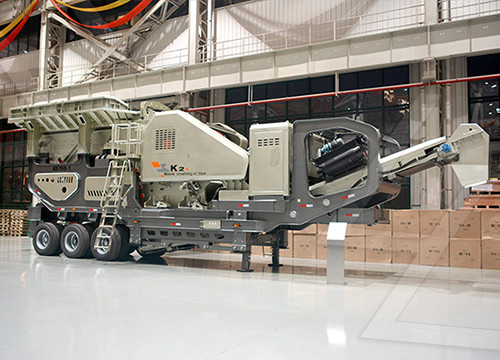
Vertical Stirred Ball Mills is for high efficiency ultrafine ore grinding
The technical features of JM stirred ball mill 1.1, high ability of fine grinding, to grinding the material to be 1μm or more fine 1.2, High efficiency and energy saving, more than 50%
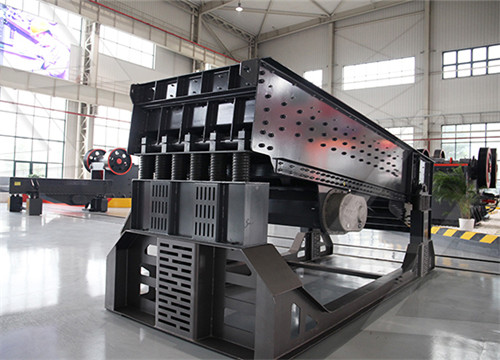
(PDF) Empirical and scale-up modeling in stirred ball mills
2011年4月1日Stirred ball mills are frequently used for ultrafine- and nanogrinding in , pharmaceutical and chemical industry, but only few investigations have been published on empirical or scale-up...
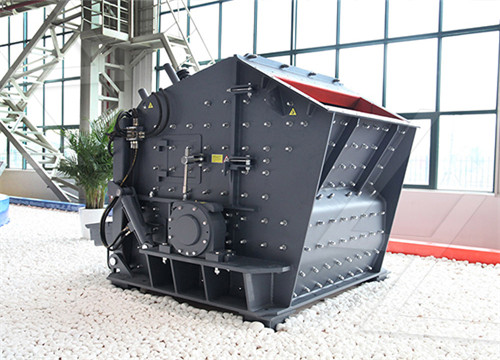
Surface modification of calcite by wet-stirred ball milling and its
DOI: 10.1016/J.POWTEC.2011.07.032 Corpus ID: ; Surface modification of calcite by wet-stirred ball milling and its properties @article{Yourtcuolu2011SurfaceMO,
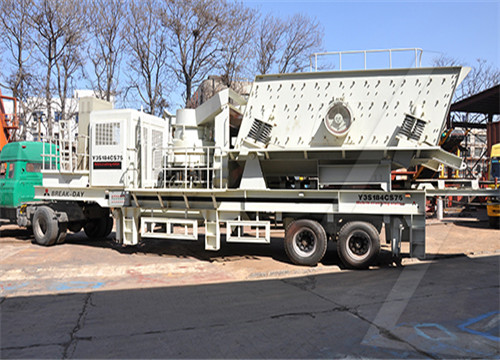
Impact of ball filling rate and stirrer tip speed on milling iron ore
2021年1月22日Xiao et al. [2] investigated the iron grade and recovery of fine grained magnetite ground by a stirred mill and ball mill. They found that the stirred mill was more beneficial for grinding P80 10–30 μm minerals to liberate more valuable minerals and the grade of iron concentrate was 5.2% higher than that of ball mill.
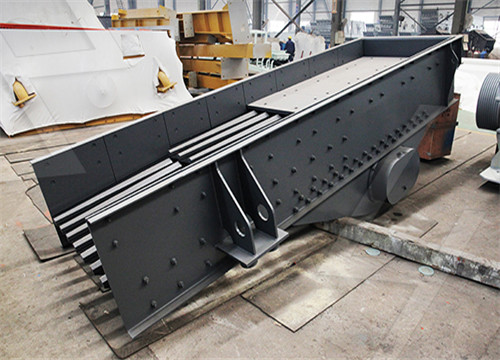
Energy Use of Fine Grinding in Mineral Processing SpringerLink
2013年12月18日In contrast to laboratory-scale testing for ball mills and AG/SAG mills, test work results for stirred mills can be used for sizing full-size equipment with a scale-up factor close to one. Larson et al .[ 19,20 ] found a scale-up factor for the Isamill of exactly 1, while Gao et al .[ 8 ] imply that the scale-up factor for SMDs is 1.25.
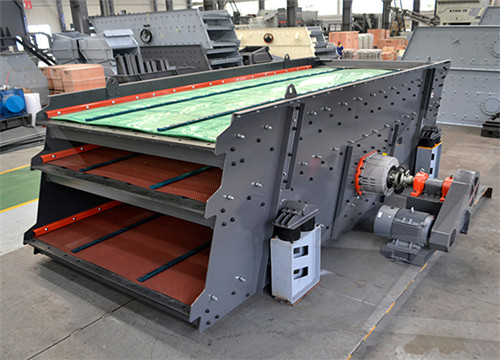
Stirred media mills in the mining industry: Material grindability
2020年6月1日The present work takes advantage of a mechanistic mill model originally developed for ball mills and the discrete element method (DEM) to simulate breakage in a vertical stirred mill. Data from a batch mill, in which two materials were tested (copper ore and limestone), served as the basis for fitting selected material parameters, whereas the
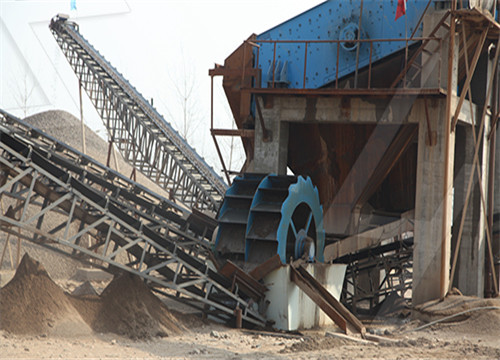
Calculate Top Ball Size of Grinding Media EquationMethod
2015年9月5日Calculate Top Ball Size of Grinding Media -FRED C. BOND EquationMethod. Although it was developed nearly 50 years ago, Bond ‘s method is still useful for calculating necessary mill sizes and power consumption for ball and rod mills. This stone discusses the basic development of the Bond method, the determination of the efficiency
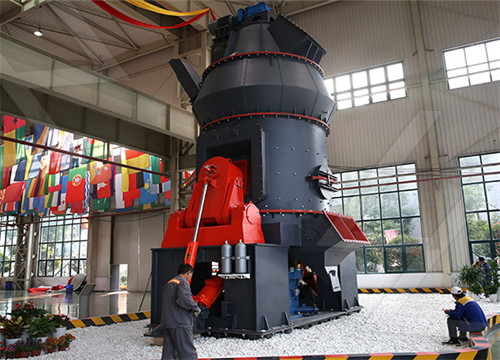
Economic and Socio-Environmental Benefits of Dry Beneficiation
2020年10月26日A study by Palaniandy and Ishikawa showed that TowerMill is 30 to 35% more energy-efficient than ball mill in fine grinding duties below 100 µm. Moreover, the specific energy requirement of the TowerMill is estimated to be 30 to 48% lower than that of a ball mill . Although the introduction of ultrafine milling increases comminution energy
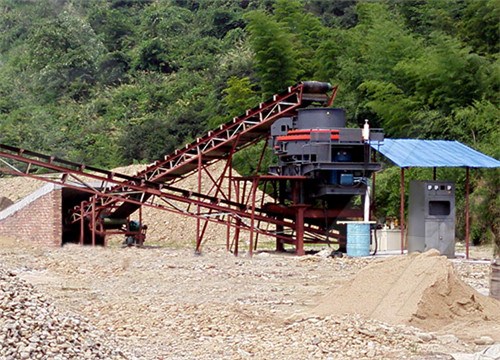
Stirred Milling Technology A New Concept in Fine
al., 2005). In stirred mills there are no free-falling possibilities for grinding media, meaning that impact action does not occur. The bead size is small, typically 1 to 6 mm which means a large amount of contacts and high grinding efficiency especially in the finest range, where ball mills are not effective or cannot reach P80 10 to 40 µm.
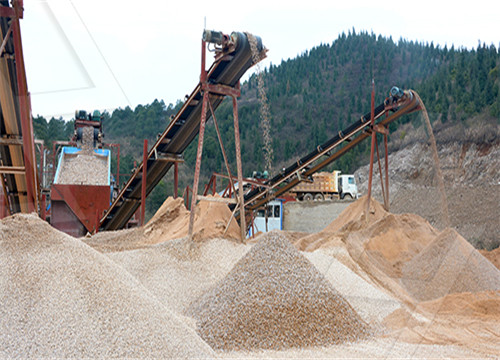
Variables Affecting the Fine Grinding of Minerals Using Stirred Mills
2003年4月1日It was found that the ball mill consumed 54.67 kWh/t energy to reduce the F 80 feed size of 722.2 lm to P 80 product size of 275.4 lm while stirred mill consumed 32.45 kWh/t of energy to produce
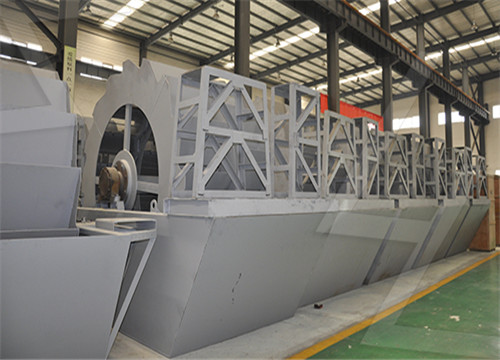
High Energy Ball Milling Union Process
The savings in energy and the increase in grinding efficiency provided by Attritors are substantial. The graph below compares various mills during the high energy ball milling process. Select a link to learn more about these Attritor-style stirred ball mills: Dry Grinding Continuous or Batch Mode. Dry Grinding Continuous Mode.
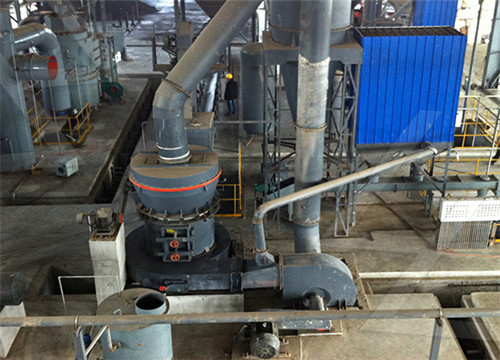
(PDF) Empirical and scale-up modeling in stirred ball mills
2011年4月1日Stirred ball mills are frequently used for ultrafine- and nanogrinding in , pharmaceutical and chemical industry, but only few investigations have been published on empirical or scale-up...
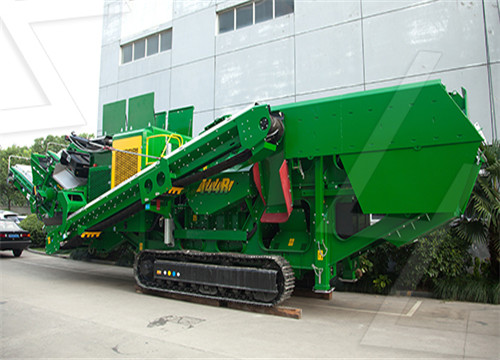
Performance Comparison of the Vertical and Horizontal Oriented Stirred
2023年1月31日Varied types/geometries of stirred mills have been produced by different manufacturers, and the comparison task has been accomplished for some of the technologies, i.e., Tower mill vs IsaMill. However, the main drawbacks of these comparisons were the uncommon characteristics of the milling environment, such as media size. In
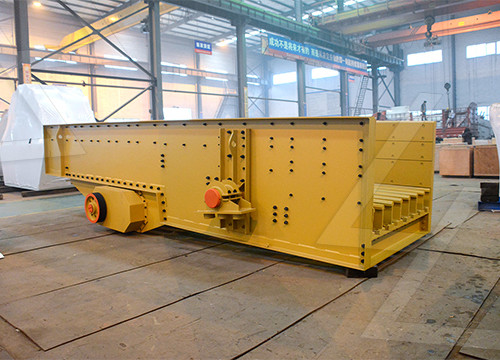
Surface modification of calcite by wet-stirred ball milling and its
Surface modification of calcite by wet-stirred ball milling and its properties @article{Yourtcuolu2011SurfaceMO, title={Surface modification of calcite by wet-stirred ball milling and its properties}, author={Emine Yoğurtcuoğlu and Metin Uçurum}, journal={Powder Technology}, year={2011}, volume={214}, pages={47-53} }
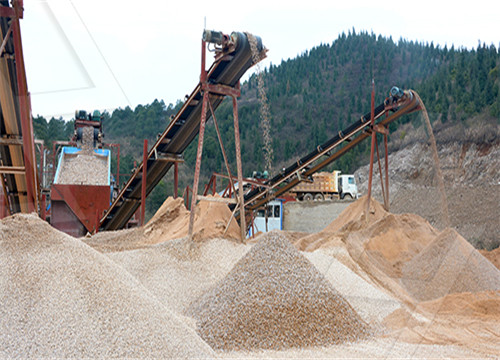
Hao Xiaofei 8 Publications 48 Citations Related Authors
Hao Xiaofei is an academic researcher. The author has contributed to research in topic(s): FeldsparEnvironmental pollution. The author has an hindex of 4, co-authored 8 publication(s) receiving 48 citation(s).
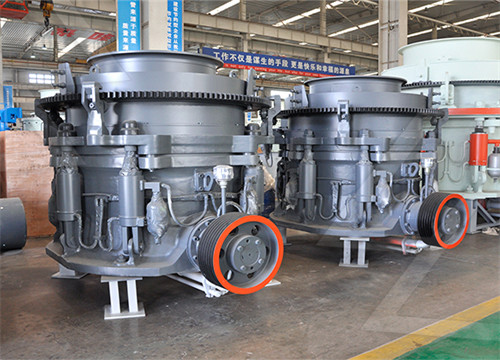
Size reduction performance evaluation of HPGR/ball mill and
2023年1月1日For this purpose, performance of two iron ore beneficiation plants with the same equipment and feed Expand 5 Effect of ball and feed particle size distribution on the milling efficiency of a ball mill: An attainable region approach N. Hlabangana, G. Danha, E. Muzenda Materials Science South African Journal of Chemical Engineering
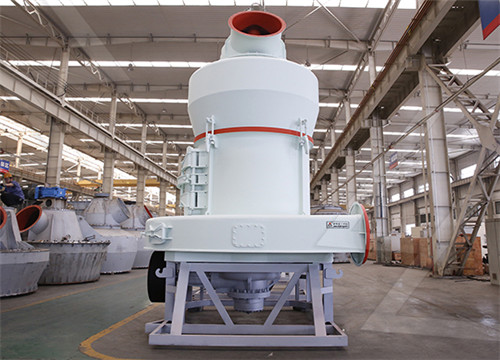
Mining ball mill-Baichy Machinery
Ball mill, also called grinding mill, ball grinding mill, is the key equipment to grind crushed materials into fine powder 20-75 micrometer. It has grate type and overflow type. ≤25mm Feed Size 18.5-800KW Motor Power 0.62–90 t/h Processing capacity Get Quotes Leave Message 60S Quick response 30 min Technical reply 24h design proposal
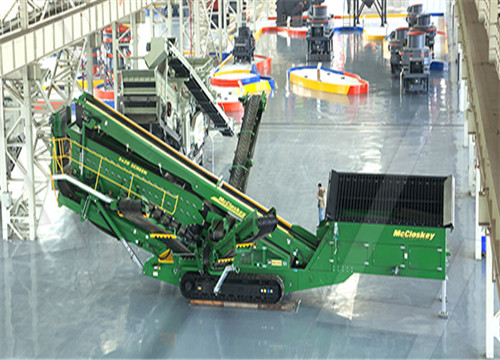
Energy Use of Fine Grinding in Mineral Processing SpringerLink
2013年12月18日In contrast to laboratory-scale testing for ball mills and AG/SAG mills, test work results for stirred mills can be used for sizing full-size equipment with a scale-up factor close to one. Larson et al .[ 19,20 ] found a scale-up factor for the Isamill of exactly 1, while Gao et al .[ 8 ] imply that the scale-up factor for SMDs is 1.25.
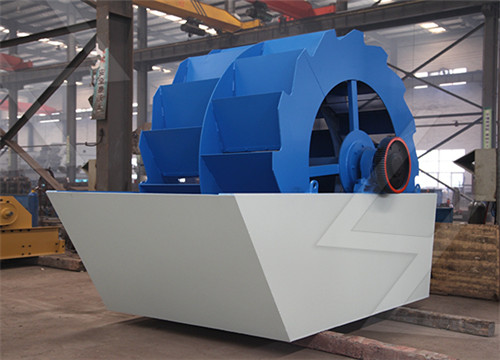
Stirred media mills in the mining industry: Material grindability
2020年6月1日The present work takes advantage of a mechanistic mill model originally developed for ball mills and the discrete element method (DEM) to simulate breakage in a vertical stirred mill. Data from a batch mill, in which two materials were tested (copper ore and limestone), served as the basis for fitting selected material parameters, whereas the
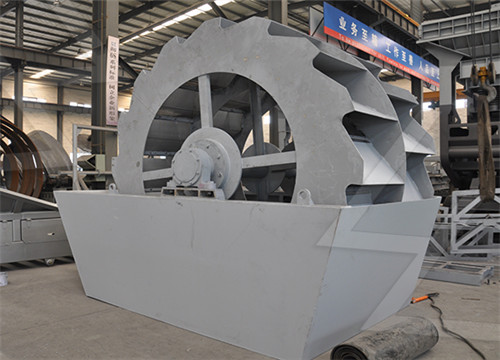
Impact of ball filling rate and stirrer tip speed on milling iron ore
2021年1月22日Xiao et al. [2] investigated the iron grade and recovery of fine grained magnetite ground by a stirred mill and ball mill. They found that the stirred mill was more beneficial for grinding P80 10–30 μm minerals to liberate more valuable minerals and the grade of iron concentrate was 5.2% higher than that of ball mill.
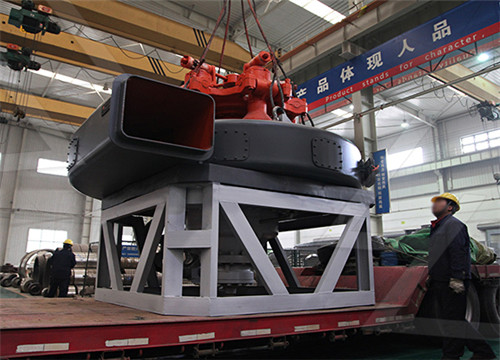
Calculate Top Ball Size of Grinding Media EquationMethod
2015年9月5日Calculate Top Ball Size of Grinding Media -FRED C. BOND EquationMethod. Although it was developed nearly 50 years ago, Bond ‘s method is still useful for calculating necessary mill sizes and power consumption for ball and rod mills. This stone discusses the basic development of the Bond method, the determination of the efficiency
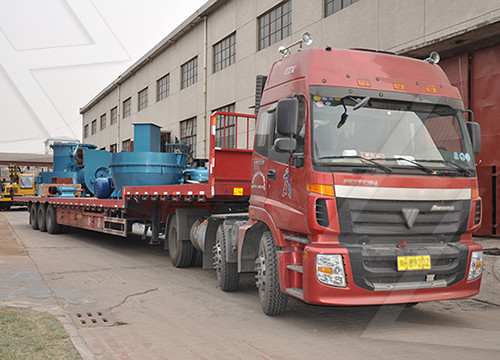
Stirred Milling Technology A New Concept in Fine
al., 2005). In stirred mills there are no free-falling possibilities for grinding media, meaning that impact action does not occur. The bead size is small, typically 1 to 6 mm which means a large amount of contacts and high grinding efficiency especially in the finest range, where ball mills are not effective or cannot reach P80 10 to 40 µm.
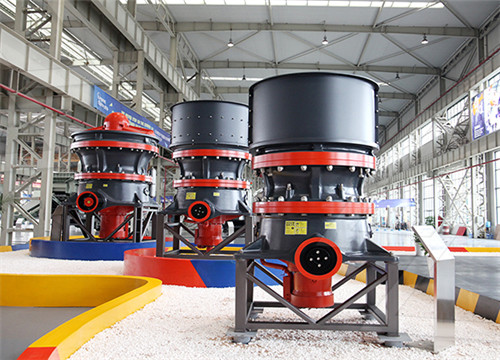
Economic and Socio-Environmental Benefits of Dry Beneficiation
2020年10月26日A study by Palaniandy and Ishikawa showed that TowerMill is 30 to 35% more energy-efficient than ball mill in fine grinding duties below 100 µm. Moreover, the specific energy requirement of the TowerMill is estimated to be 30 to 48% lower than that of a ball mill . Although the introduction of ultrafine milling increases comminution energy
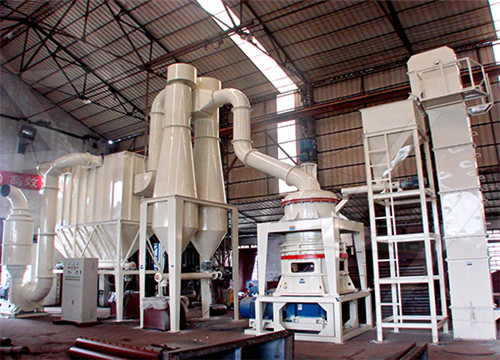
Variables Affecting the Fine Grinding of Minerals Using Stirred Mills
2003年4月1日Jankovic [6, 7] investigated the effect of grinding media in a vertical stirred pilot mill and found that 6.8 mm steel grinding media were more effective than coarser (12 mm) grinding media...
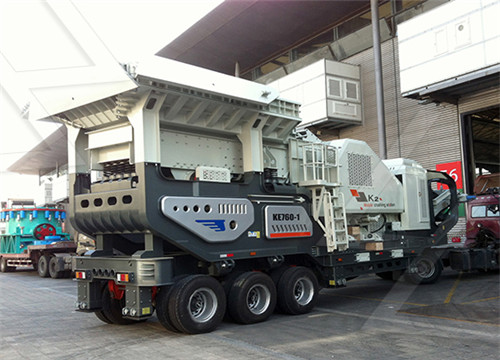
High Energy Ball Milling Union Process
The savings in energy and the increase in grinding efficiency provided by Attritors are substantial. The graph below compares various mills during the high energy ball milling process. Select a link to learn more about these Attritor-style stirred ball mills: Dry Grinding Continuous or Batch Mode. Dry Grinding Continuous Mode.
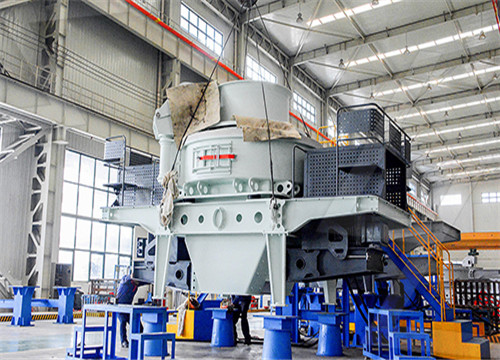
(PDF) Empirical and scale-up modeling in stirred ball mills
2011年4月1日Stirred ball mills are frequently used for ultrafine- and nanogrinding in , pharmaceutical and chemical industry, but only few investigations have been published on empirical or scale-up...
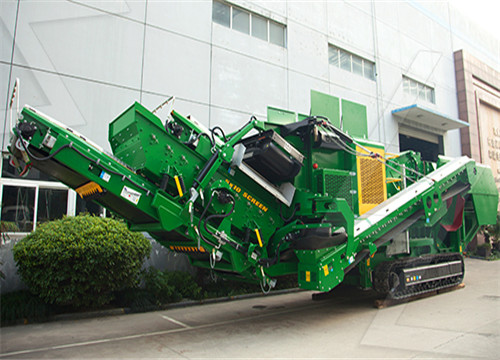
Performance Comparison of the Vertical and Horizontal Oriented Stirred
2023年1月31日Varied types/geometries of stirred mills have been produced by different manufacturers, and the comparison task has been accomplished for some of the technologies, i.e., Tower mill vs IsaMill. However, the main drawbacks of these comparisons were the uncommon characteristics of the milling environment, such as media size. In
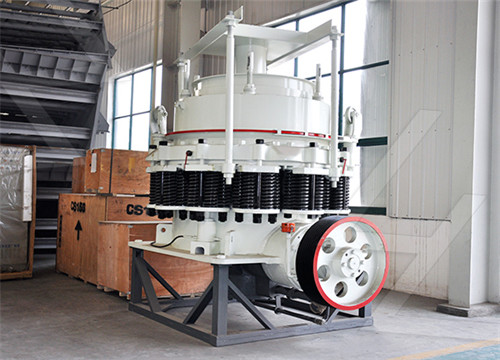
Size reduction performance evaluation of HPGR/ball mill and
2023年1月1日For this purpose, performance of two iron ore beneficiation plants with the same equipment and feed Expand 5 Effect of ball and feed particle size distribution on the milling efficiency of a ball mill: An attainable region approach N. Hlabangana, G. Danha, E. Muzenda Materials Science South African Journal of Chemical Engineering
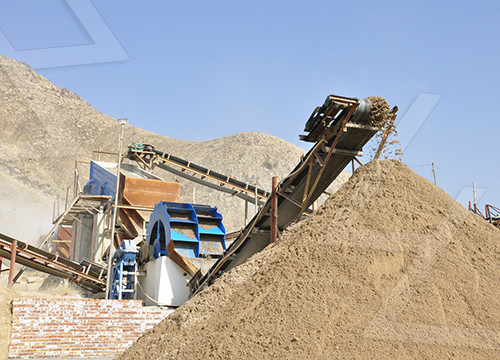
Surface modification of calcite by wet-stirred ball milling and its
Surface modification of calcite by wet-stirred ball milling and its properties @article{Yourtcuolu2011SurfaceMO, title={Surface modification of calcite by wet-stirred ball milling and its properties}, author={Emine Yoğurtcuoğlu and Metin Uçurum}, journal={Powder Technology}, year={2011}, volume={214}, pages={47-53} }
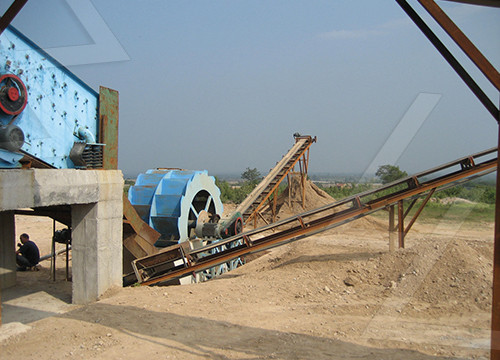
Hao Xiaofei 8 Publications 48 Citations Related Authors
Hao Xiaofei is an academic researcher. The author has contributed to research in topic(s): FeldsparEnvironmental pollution. The author has an hindex of 4, co-authored 8 publication(s) receiving 48 citation(s).
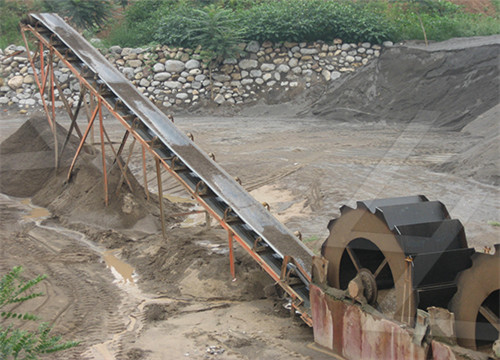
Ultrafine Grinding of Kokaksu Bauxite ore via Stirred Mill
In this study, the performances of stirred and ball mills for fine and ultrafine grinding of bauxite ore were investigated. 2. Materials and Methods. 2.1 Stirred Mill and Ball Mill . Laboratory scale stirred mill uses a grinding pot filled with small balls whereby grinding takes place by attrition between the balls.