Nickel Copper Ore Smelter Plant Waste Heat Industrial Milling
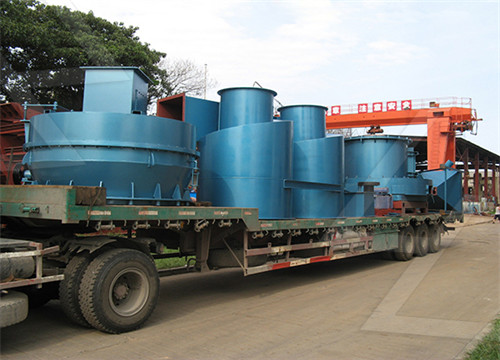
Nickel processing Extraction and refining Britannica
Nickel concentrates may be leached with sulfuric acid or ammonia, or they may be dried and smelted in flash and bath processes, as is the case with copper. Nickel requires
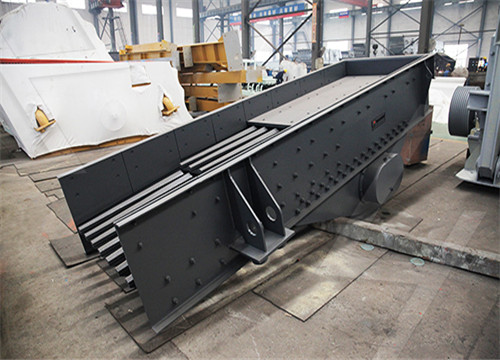
进一步探索
Nickel and its extraction SlideShare(PDF) Advanced Review on Extraction of Nickel from Prim(PDF) Nickel extraction from nickel matte ResearchGateNickel Extraction and Purification Mond ProcessNickel Ore Mining Process,Processing Nickel Ores,Nickel 根据热度为您推荐•反馈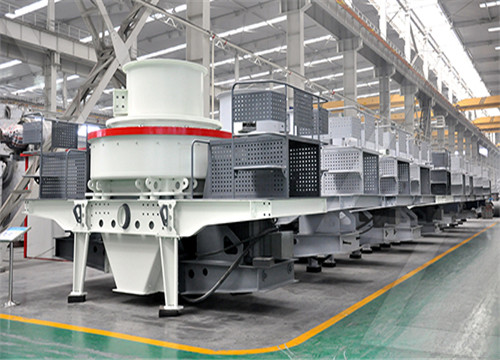
Rock Smelting of Copper Ores with Waste Heat Recovery
2013年1月1日A life cycle assessment study was carried out to assess the potential energy and greenhouse gas benefits of a conceptual flowsheet of the rock smelting process, using copper ore as an example
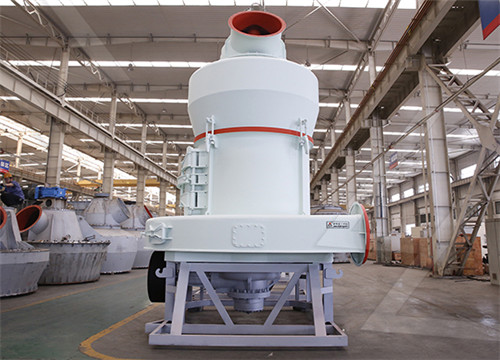
Nickel Smelting and Refining International Finance
and volatiles. Older nickel-smelting processes, such as blast or reverberatory furnaces, are no longer acceptable because of low energy efficien-cies and environmental concerns. In
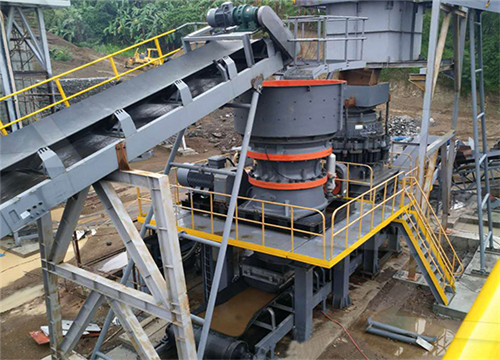
Down on the Farm That Harvests Metal From Plants
2020年2月26日Currently, the most common way to extract nickel for electronics requires intense energy — often derived from coal and diesel
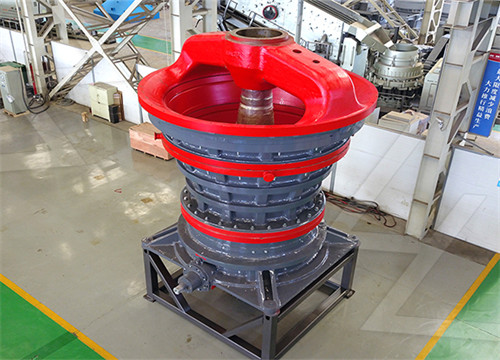
Smelting Wikipedia
OverviewEnvironmental and occupational health impactsProcessHistoryBase metalsSee alsoBibliography
Smelting has serious effects on the environment, producing wastewater and slag and releasing such toxic metals as copper, silver, iron, cobalt, and selenium into the atmosphere. Smelters also release gaseous sulfur dioxide, contributing to acid rain, which acidifies soil and water. The smelter in Flin Flon, Canada was one of the largest point sources of mercury in North America in the 20th century. Even after smelter releases were drastically reduced, landscape re-emission continued
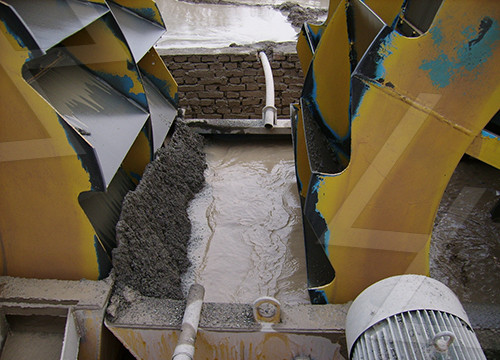
TENORM: Copper Mining and Production Wastes US EPA
2023年2月16日Smelting: Then, copper concentrates are mixed with silica (sand) and limestone and heated in a furnace to form two naturally-separating layers. One layer is a
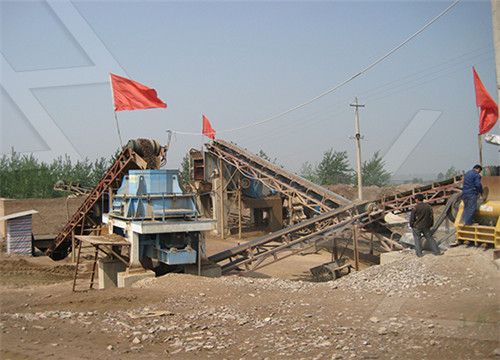
Copper Mining and Processing: Processing Copper Ores
At the smelter, high temperatures are used to further purify the ore in a series of smelting steps. The copper concentrate is first sent through the smelting furnace to be heated up to 2,300 °F and converted into molten
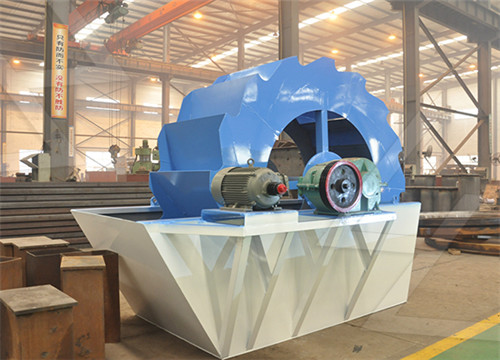
Boliden Harjavalta Boliden
One of the most efficient copper and nickel producers in the world. Boliden Harjavalta is located in south west Finland, close to the port on the Baltic Sea. The smelter’s main products are copper, nickel, gold and silver,
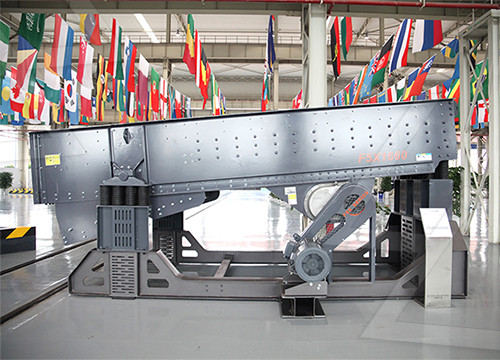
Norilsk Division Nornickel
Norilsk Concentrator processes all disseminated ores from the Norilsk-1 deposit, cuprous and disseminated ores from the Oktyabrskoye and Talnakhskoye deposits, and low
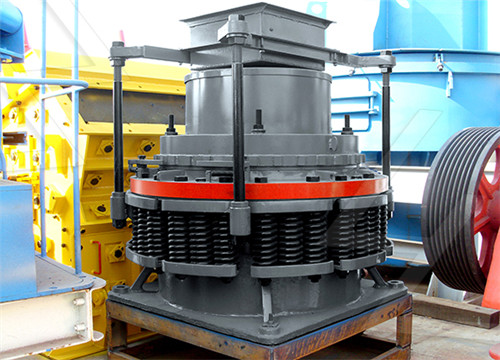
12.3 Primary Copper Smelting US EPA
In the smelting process, either hot calcine from the roaster or raw unroasted concentrate is melted with siliceous flux in a smelting furnace to produce copper matte. The required
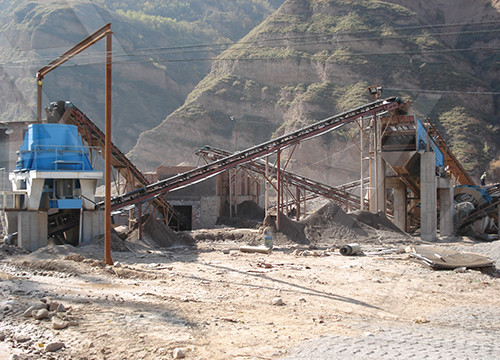
Indonesia’s Nickel Industrial Strategy Center for Strategic and
2021年12月8日When the mining companies had not built smelters in time and the nickel ore exports reached an all-time high (65 million metric tons in 2013, with 90 percent of them going to China), the government imposed, relaxed, and reimposed an export ban on the unprocessed nickel ore: Indonesia first imposed an export ban on nickel ore in January
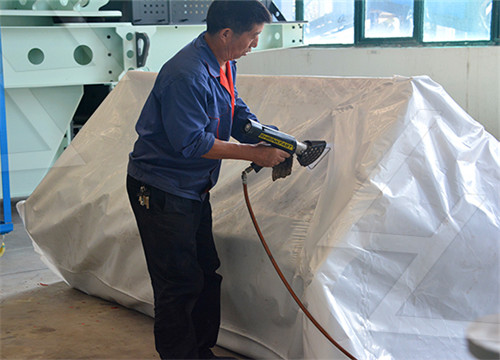
Down on the Farm That Harvests Metal From Plants
2020年2月26日Currently, the most common way to extract nickel for electronics requires intense energy — often derived from coal and diesel — and creates heaps of acidic waste. A typical smelter costs
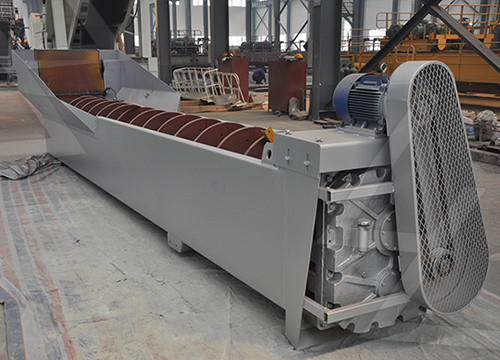
Chapter 7 Energy Use in the Copper Industry Princeton
also use diesel fuel for surface hauling of ore to the mill. Approximately 155 pounds of explosives are used for every short ton of copper produced in underground mines.s The average grade of the ore mined, the ratio of overlying dirt and rock (overburden) to the ore body (stripping ratio), and the depth of the pit 5Gaines, supra note 3.
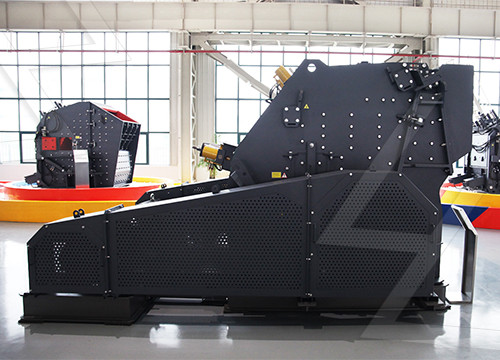
Nickel Smelting and Refining International Finance
and volatiles. Older nickel-smelting processes, such as blast or reverberatory furnaces, are no longer acceptable because of low energy efficien-cies and environmental concerns. In flash smelting, dry sulfide ore containing less than 1% moisture is fed to the furnace along with preheated air, oxygen-enriched air (30–40% oxygen), or pure oxygen.
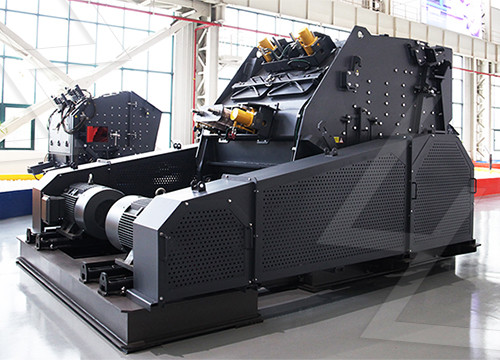
First Quantum Minerals Ltd. Our Operations
The process plant is designed to treat 55 million tonnes per annum of copper ore from Sentinel mine, with a separate 4 million tonnes per annum circuit designed to process nickel ore feed from the Enterprise project or additional copper ore feed from Sentinel. Technical Report. Trident’s most recent NI 43-101 Technical Report.

Copper Smelting International Finance Corporation
Modern plants using good industrial practices should set as targets total dust releases of 0.5–1.0 kg/t of copper and SO. 2 . discharges of 25 kg/t of copper. A double-contact, double-absorption plant should emit no more than 0.2 kg of sulfur dioxide per ton of sulfuric acid produced (based on a conversion efficiency of 99.7%). Emissions
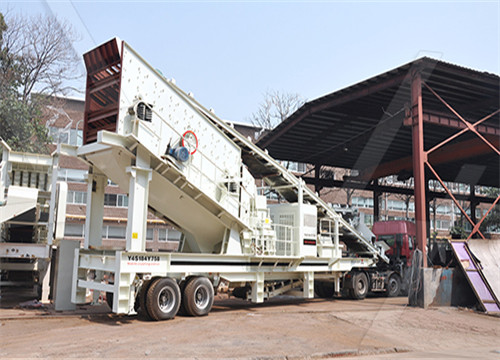
Boliden Harjavalta Boliden
One of the most efficient copper and nickel producers in the world. Boliden Harjavalta is located in south west Finland, close to the port on the Baltic Sea. The smelter’s main products are copper, nickel, gold and silver, as well as by-products such as sulphuric acid. Boliden Harjavalta is unique our smelter is the only nickel smelter in

Nickel processing Britannica
Nickel has a relatively high melting point of 1,453 °C (2,647 °F) and a face-centred cubic crystal structure, which gives the metal good ductility. Nickel alloys exhibit a high resistance to corrosion in a wide variety of media and have the ability to withstand a range of high and low temperatures.
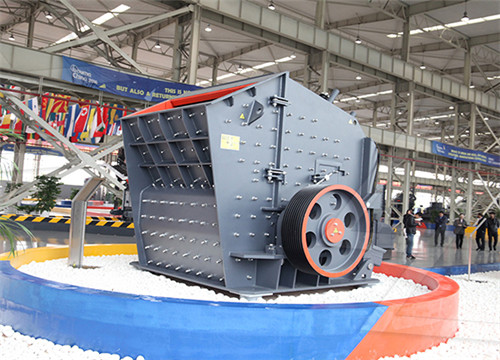
Extraction and Refining of the Platinum Metals
Ground nickel matte is fed through a hopper on to the top hearth which is kept at a low temperature; it then falls through to the lower hearth which is kept at 900° to 950°C. After cooling, the resultant nickel oxide is briquetted with anthracite coal and sand.
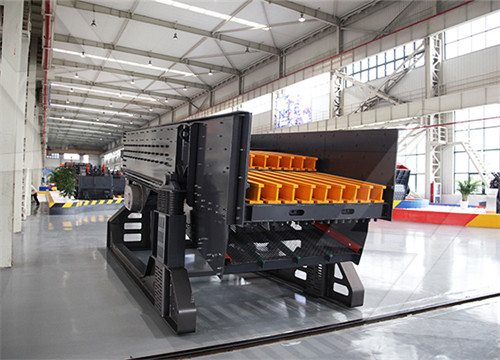
Clean Air Act Standards and Guidelines for the Metals
2022年7月22日Clean Air Act Standards and Guidelines for the Metals Production Industry The following are the stationary sources of air pollution for metal production industries, and their corresponding air pollution regulations. National Emission Standards for Hazardous Air Pollutants NESHAP New Source Performance Standards NSPS
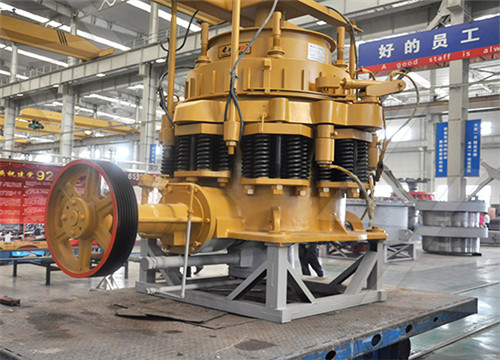
IOP Conference Series: Materials Science and Engineering
2019年10月16日Enhanced Recycling of Waste Copper Smelter Dust from Existing and Proposed Smelter Plant at the Palabora Copper (pty) ltd, impopo, South Africa To cite this article: Daniel O. Okanigbe et al 2018 IOP Conf. Ser.: Mater. Sci. Eng. 391 012006 View the article online for updates and enhancements. Related content The Study and Application of
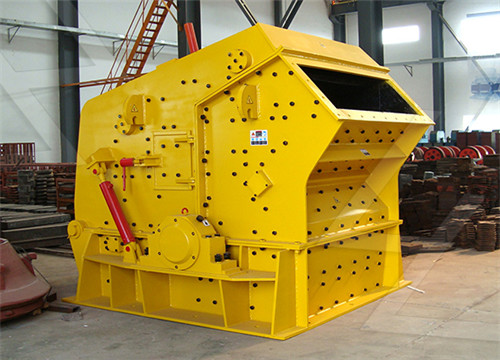
12.3 Primary Copper Smelting US EPA
In the smelting process, either hot calcine from the roaster or raw unroasted concentrate is melted with siliceous flux in a smelting furnace to produce copper matte. The required heat comes from partial oxidation of the sulfide charge and from burning external fuel. Most of the iron and 10/86 (Reformatted 1/95) Metallurgical Industry 12.3-1
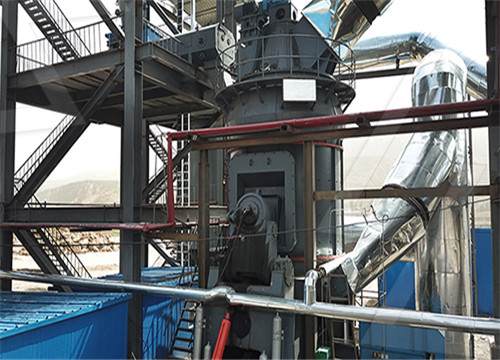
A case study comparison of a sulphuric acid plant with and
2022年4月8日Purpose Metal ore smelters have significant environmental footprints due to very high energy consumption and the resulting large quantities of waste heat. The industry recognizes, therefore, the need for implementation of changes to improve process economics by reducing primary energy consumption through recovery and repurposing
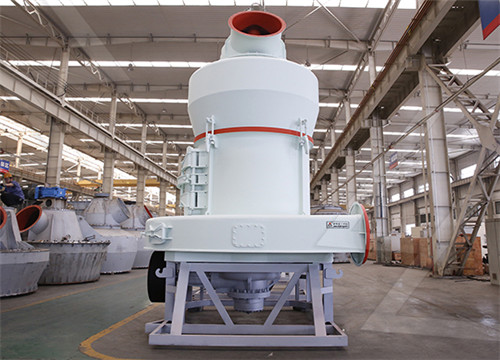
Copper Smelting an overview ScienceDirect Topics
Copper Production. Hong Yong Sohn, Bart Blanpain, in Treatise on Process Metallurgy: Industrial Processes, 2014. 2.1.1.6.1 FeO–Fe 2 O 3 –SiO 2 Slags. It has been customary since early times in copper smelting, when acid refractories were used universally, to add SiO 2 to form a slag with the iron that has been oxidized. This is still the most common

Indonesia’s Nickel Industrial Strategy Center for Strategic and
2021年12月8日When the mining companies had not built smelters in time and the nickel ore exports reached an all-time high (65 million metric tons in 2013, with 90 percent of them going to China), the government imposed, relaxed, and reimposed an export ban on the unprocessed nickel ore: Indonesia first imposed an export ban on nickel ore in January
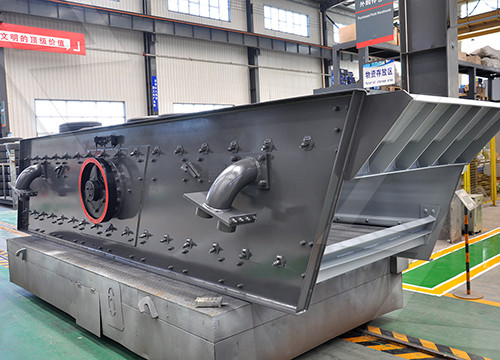
A case study comparison of a sulphuric acid plant with and
2022年4月8日Purpose Metal ore smelters have significant environmental footprints due to very high energy consumption and the resulting large quantities of waste heat. The industry recognizes, therefore, the need for implementation of changes to improve process economics by reducing primary energy consumption through recovery and repurposing
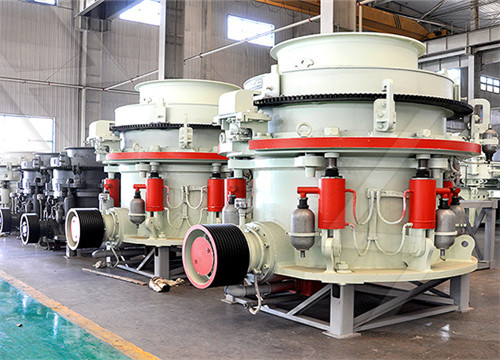
Down on the Farm That Harvests Metal From Plants
2020年2月26日Currently, the most common way to extract nickel for electronics requires intense energy — often derived from coal and diesel — and creates heaps of acidic waste. A typical smelter costs
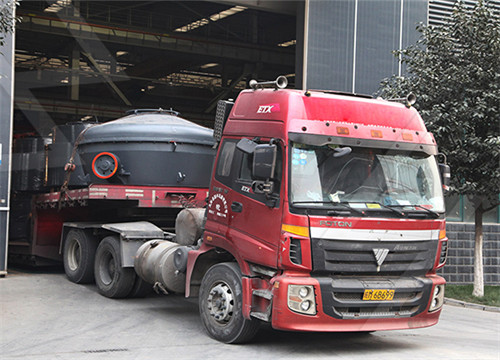
Chapter 7 Energy Use in the Copper Industry Princeton
also use diesel fuel for surface hauling of ore to the mill. Approximately 155 pounds of explosives are used for every short ton of copper produced in underground mines.s The average grade of the ore mined, the ratio of overlying dirt and rock (overburden) to the ore body (stripping ratio), and the depth of the pit 5Gaines, supra note 3.
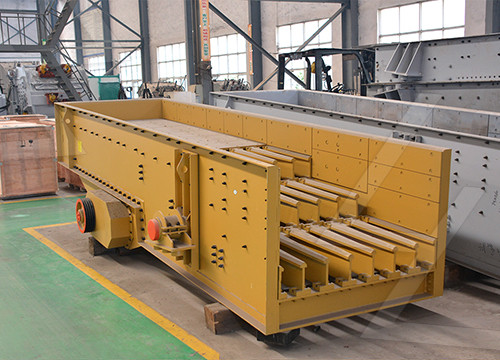
Nickel Smelting and Refining International Finance
and volatiles. Older nickel-smelting processes, such as blast or reverberatory furnaces, are no longer acceptable because of low energy efficien-cies and environmental concerns. In flash smelting, dry sulfide ore containing less than 1% moisture is fed to the furnace along with preheated air, oxygen-enriched air (30–40% oxygen), or pure oxygen.

First Quantum Minerals Ltd. Our Operations
The process plant is designed to treat 55 million tonnes per annum of copper ore from Sentinel mine, with a separate 4 million tonnes per annum circuit designed to process nickel ore feed from the Enterprise project or additional copper ore feed from Sentinel. Technical Report. Trident’s most recent NI 43-101 Technical Report.
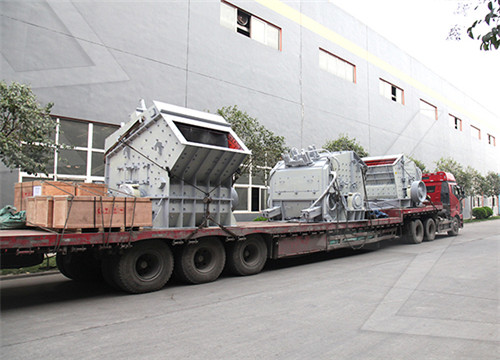
Smelters Boliden
Boliden develops its own methods for waste disposal. The smelting plant at Odda disposes waste in an underground cavity and Rönnskär is building a unique storage around 350 metres underground that will begin use during 2021. Underground storage is a long-term, sustainable solution for final disposal of smelter waste. Find out more.
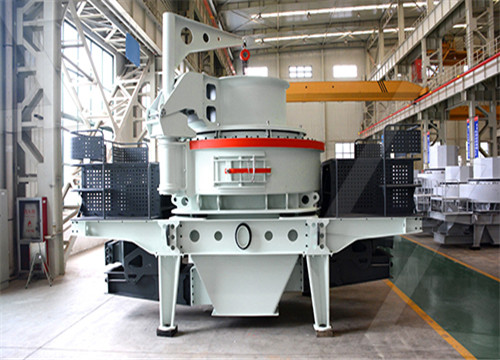
Copper Smelting International Finance Corporation
Modern plants using good industrial practices should set as targets total dust releases of 0.5–1.0 kg/t of copper and SO. 2 . discharges of 25 kg/t of copper. A double-contact, double-absorption plant should emit no more than 0.2 kg of sulfur dioxide per ton of sulfuric acid produced (based on a conversion efficiency of 99.7%). Emissions
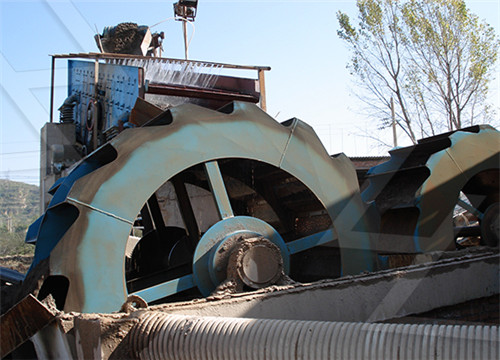
Boliden Harjavalta Boliden
Smelters One of the most efficient copper and nickel producers in the world Boliden Harjavalta is located in south west Finland, close to the port on the Baltic Sea. The smelter’s main products are copper, nickel, gold and silver, as
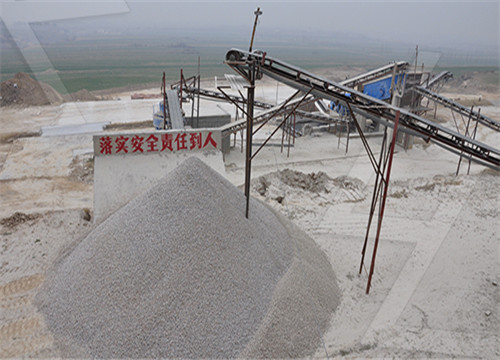
:: WorstPolluted : Projects Reports
Metal processing plants and smelters are facilities that extract various metals from ore to create more refined metal products. Metals include copper, nickel, lead, zinc, silver, cobalt, gold, cadmium, etc. Smelting specifically involves heating the ore with a reducing agent such as coke, charcoal or other purifying agents.
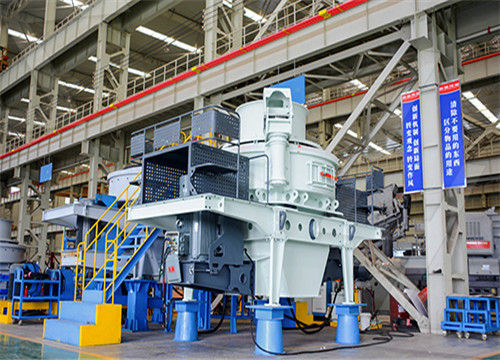
IOP Conference Series: Materials Science and Engineering
2019年10月16日Enhanced Recycling of Waste Copper Smelter Dust from Existing and Proposed Smelter Plant at the Palabora Copper (pty) ltd, impopo, South Africa To cite this article: Daniel O. Okanigbe et al 2018 IOP Conf. Ser.: Mater. Sci. Eng. 391 012006 View the article online for updates and enhancements. Related content The Study and Application of

12.3 Primary Copper Smelting US EPA
In the smelting process, either hot calcine from the roaster or raw unroasted concentrate is melted with siliceous flux in a smelting furnace to produce copper matte. The required heat comes from partial oxidation of the sulfide charge and from burning external fuel. Most of the iron and 10/86 (Reformatted 1/95) Metallurgical Industry 12.3-1

Copper Smelting an overview ScienceDirect Topics
Copper Production. Hong Yong Sohn, Bart Blanpain, in Treatise on Process Metallurgy: Industrial Processes, 2014. 2.1.1.6.1 FeO–Fe 2 O 3 –SiO 2 Slags. It has been customary since early times in copper smelting, when acid refractories were used universally, to add SiO 2 to form a slag with the iron that has been oxidized. This is still the most common
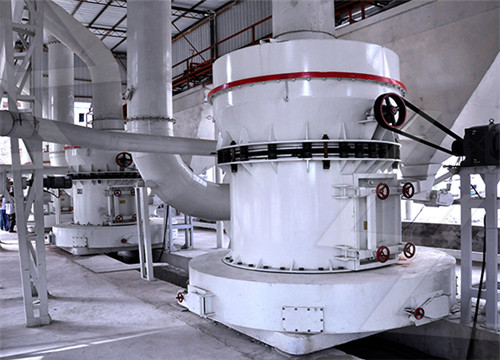
An overview of Southern African PGM smelting Mintek
Nickel of Russia. Smaller (but still significant) quantities of PGMs are produced by Falconbridge and Inco of Canada, also as co-products from nickel sulphide smelting. There are many similarities between PGM smelting and nickel sulphide smelting, and the range of technologies in use includes six-in-line rectangular electric furnaces, three-