Grinding Classifying Efficient
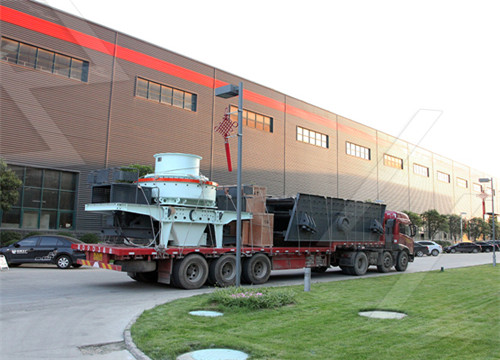
Grinding and Classifying Systems neuman-esser.de
根据热度为您推荐•反馈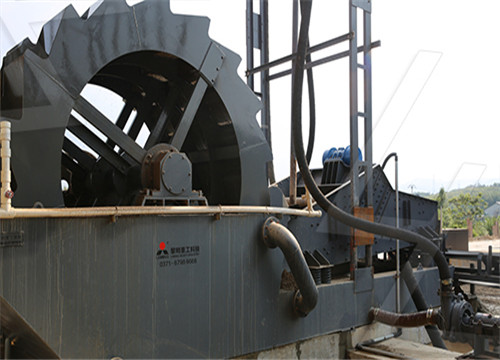
CFS/HD-S High-efficiency Fine Classifier GrindingDispersing
This high efficiency air classifier was developed for ultra-fine, sharp separation, and is often used in conjunction with grinding plants. The optimized classifier wheel geometry
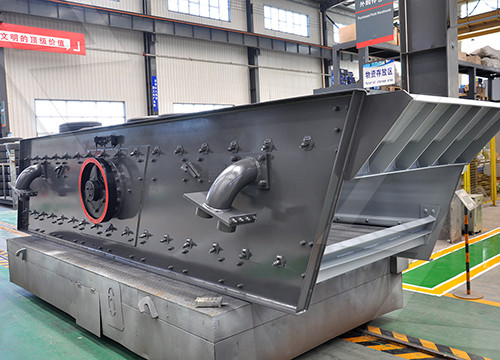
Efficient Grinding and Classifying of Powder Coatings
IntroductionPowder Grinding SystemParticle Size DistributionsGrinding Systems For Small BatchesSummary
The feeding of chips out of a vessel is done by a dosing rotary airlock. The chips are transported by airflow into the ICM, where the grinding and classification process takes place. The ICM grinds the powder with hammers that have a tip speed of up to 130 m/s. The solids are comminuted in the milling chamber at the exterior circumference of the gr...
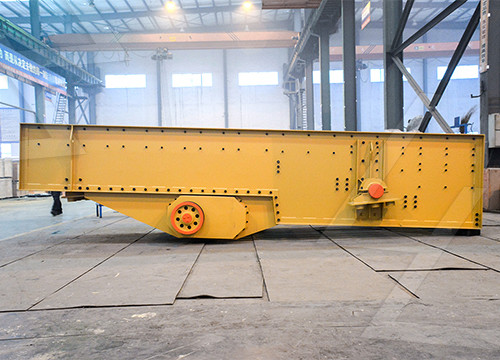
High-efficiency classification FCB TSV™ Classifier Fives
For a grinding mill to reach optimal performance levels, it needs to incorporate a highly efficient classifier that separates fine product from coarse materials. The classifier improves the product quality by ensuring
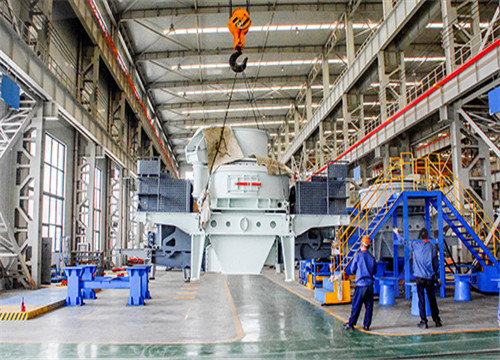
GRINDING OPTIMISATION Combining forces
Figure 7: capacity increase by upgrading an HPGR in pre-grinding mode into semi-finish grinding mode with 2-Stage Koesep using the example of a cement plant in Austria
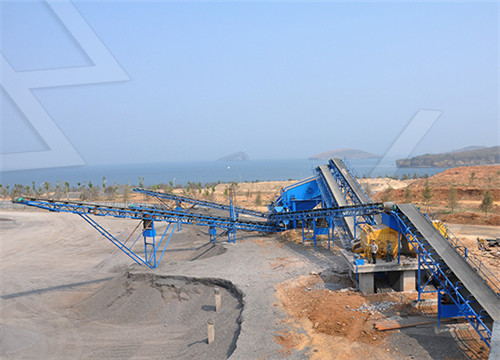
CFS Fine Classifier NETZSCH GrindingDispersing
Classifying Fine Powder. When a screening machine cannot be used to separate fine powder due to the desired final fineness or other product characteristics, our "standard"
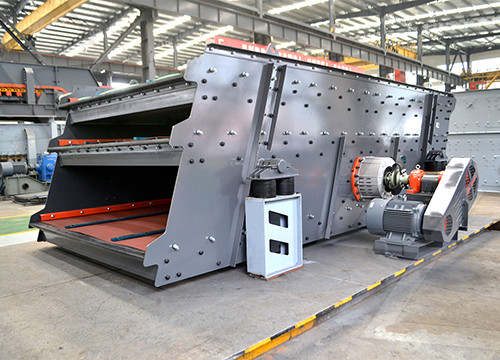
3 Important Indicators In Grinding And Classification
2020年2月24日Grinding and Classifying Efficiency The efficiency in the grinding and classification stage mainly refers to the grinding efficiency, that is, the amount of ore
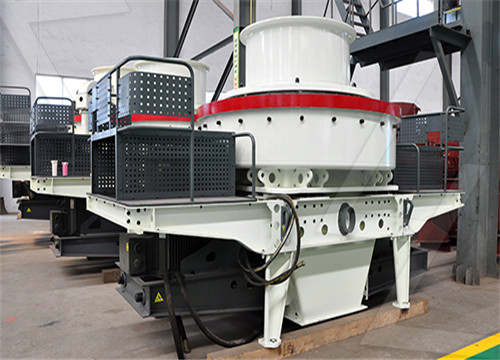
Ways to Improve Classifying Efficiency_ahhli4007的博客
2012年8月25日The basic components of the grinding and classification process control system : (1) grinding and classification process control system.which is composed of
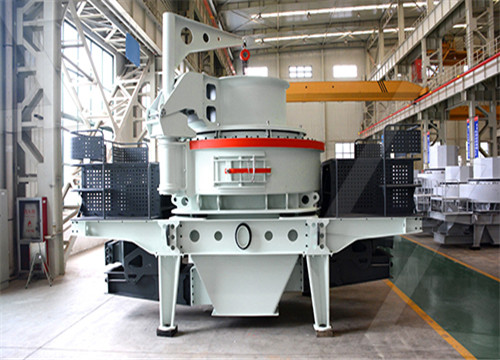
10 Ways to Improve the Grinding Efficiency of Your Ball Mill
2019年4月15日According to foreign reports, the automatic control of the grinding and classifying system can increase the production capacity by 2.5%~10%, and 0.4-1.4 kwh
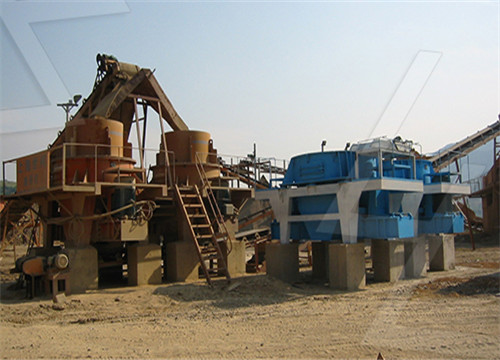
Air Classifiers Sturtevant Inc.
Three types of separators each with a high-precision method of classifying particles according to size or density. For dry materials of 100 mesh and smaller, air
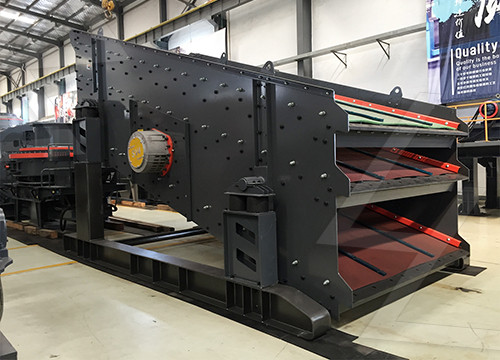
Improvement of pulverization efficiency for micro-sized particles
2019年11月2日The schematic grinding and classification structure of AJMS was shown in Fig. 1. The AJMS is a device that can transform the pulverized material into fine particles particularly from submicron to several microns. As a result, the classified particle becomes smaller and the classification efficiency becomes higher once the centrifugal force
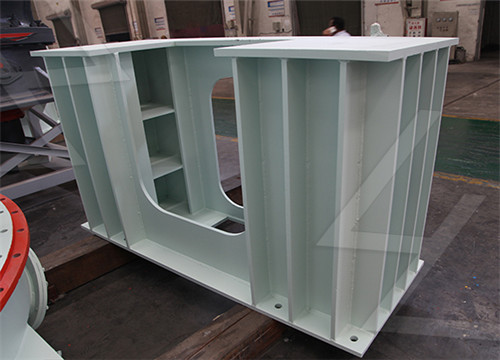
Impact of the powder flow behavior on continuous fine grinding
2018年11月1日1. Introduction. The energy efficiency of dry fine grinding processes can mainly be increased by either (1) further development of mills and mill equipment, (2) improving classifiers as well as grinding-classifying-circuits or (3) enhancing the process behavior of the ground material (Scheibe et al., 1978).Since the demand on fine and ultra
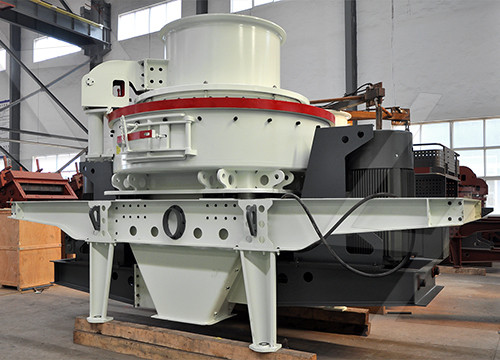
CFS/HD-S High-efficiency Fine Classifier GrindingDispersing
This high efficiency air classifier was developed for ultra-fine, sharp separation, and is often used in conjunction with grinding plants. The optimized classifier wheel geometry produces the finest cut points and high yields that have not been possible with production scale conventional air classifiers with only one classifier wheel.
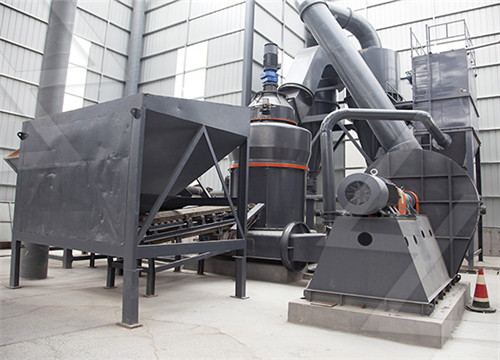
Particle-size reduction Chemical Engineering Page 1
2012年11月1日There are seven types of stresses that can be imparted to achieve size reduction, including the following: • Compression between two rigid surfaces • Compression between surfaces and adjacent bed of solids • Shearing forces by mechanical means (tearing, cleaving, cutting or shredding) • Shearing forces due to surrounding media
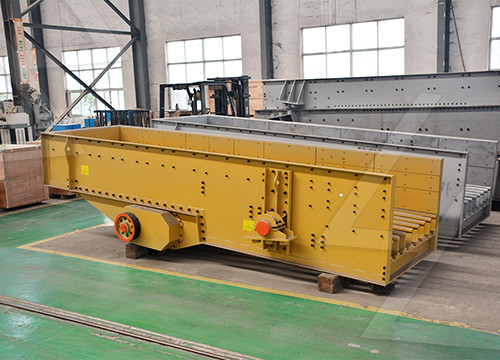
InlineStar Inline Classifier NETZSCH GrindingDispersing
An In-Line classifier combined with a fine grinding mill enables one to reduce the number plant components and energy! The intermediate separation of the product after the grinding stage is no longer required eliminating the need for cyclone, filter and exhaust blower. The classification results are impressive.
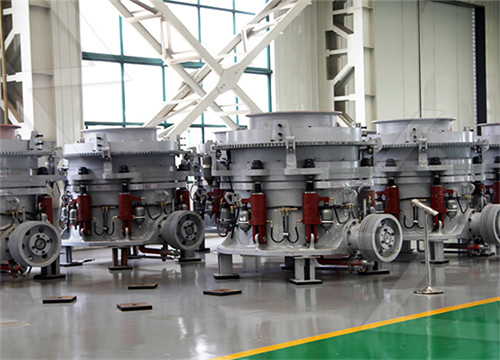
3 Important Indicators In Grinding And Classification Stage
In this post you're going to know about the important indicators in grinding and classification stage and what influences these indicators. This post includes 3 important indicators: grinding fineness. grinding capacity. grinding classification efficiency. So if you want to learn more about grinding and classifaction,you'll love this post.
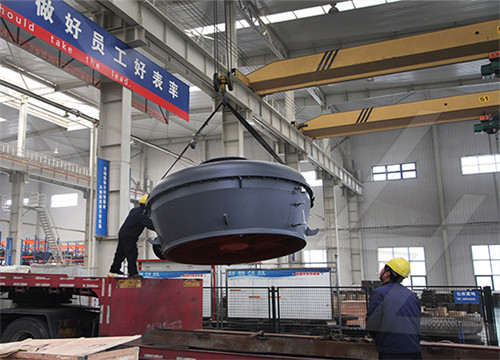
Ways to Improve Classifying Efficiency_ahhli4007的博客-CSDN博客
2012年8月25日The basic components of the grinding and classification process control system : (1) grinding and classification process control system.which is composed of the following three basic control aspects: given control of the amount of ore grinding concentration control, grading the indiscriminate flow concentration (particle size) control.
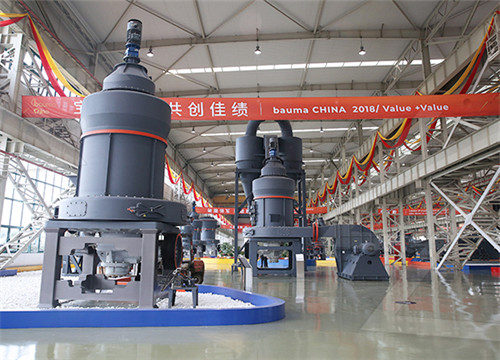
Ball Charge and Grinding Efficiency Grinding
The volume of grinding media in a mill is directly related to grinding efficiency. The higher the volume of grinding media the more effective the grind. Balls must be added to maintain the media load and mill power
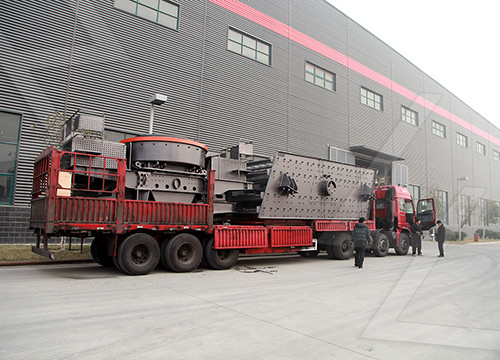
Air Classifiers Sturtevant Inc.
For dry materials of 100 mesh and smaller, air classification provides the most effective and efficient means for separating a product from a feed stream for dedusting, or for increasing productivity when used in conjunction with grinding equipment.
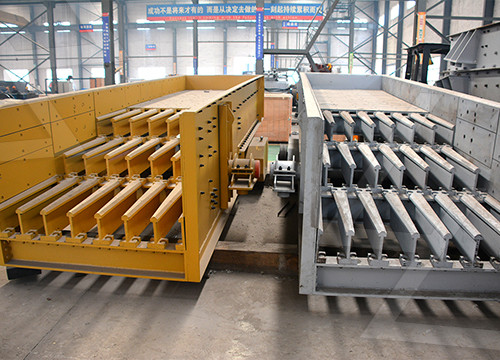
Energy-Efficient Technologies in Cement Grinding
2016年10月5日Performance of grinding circuits has been improved in recent years by the development of machinery such as high-pressure grinding rolls (HPGR) (roller presses), Horomills, high-efficiency
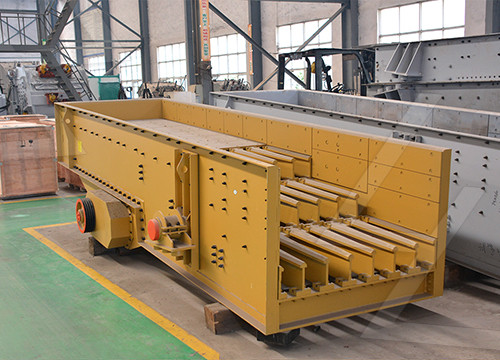
Factors Affecting Ball Mill Grinding Efficiency
2017年10月25日c) Closed Circuit Grinding Also closely related to the ability of a ball mill to perform most effectively on a particular material size distribution is the increased grinding efficiency observed with increased
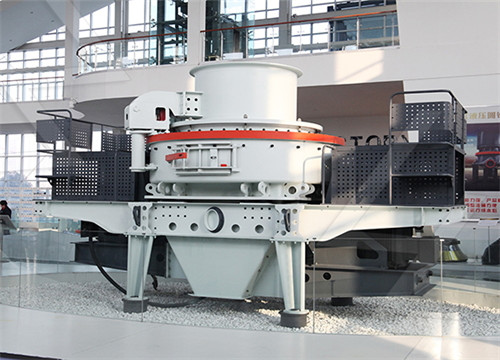
What Factors Will Influence Ball Mill Grinding Efficiency?
2021年3月26日Ball mill grinding efficiency is influenced by many factors: ore grindability, feed size, grinding product size, ball mill diameter and length, ball mill working speed, liner type, steel ball loading system, grinding concentration, return sand ratio in closed-circuit grinding and feed rate. To improve the ball mill grinding efficiency, you must
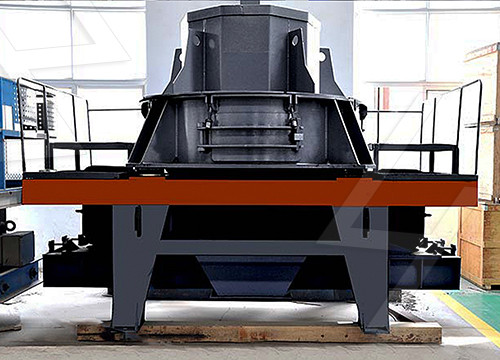
Classifying System
classifying system is a new generation of high-efficiency sorting equipment independently developed by Guilin Hongcheng. It mainly includes LFX series sorting machines and FW series sorting machines, covering powder sorting functions from 80 mesh D97 to 3000 mesh D97. The whole system has fast material flow, high classification accuracy, convenient
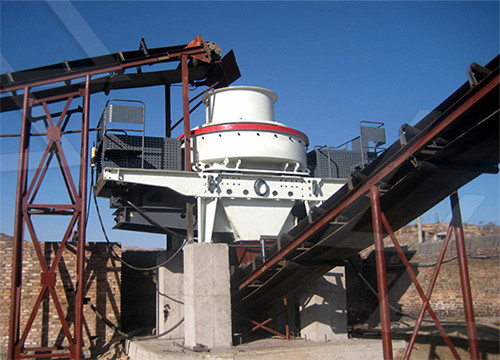
HOSOKAWAMICRON CORPORATION
The ACM Pulverizer is a fine impact mill with a built-in classifier, widely used for many applications with over 2500 units sold throughout the world. Adjusting the rotating speed of the grinding rotor and the classifying rotor can easily control the product size. There are many models of the ACM.
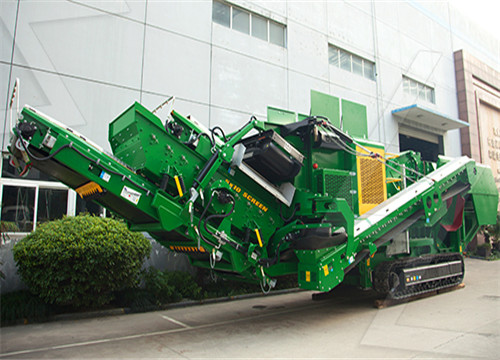
Improvement of pulverization efficiency for micro-sized particles
2019年11月2日The schematic grinding and classification structure of AJMS was shown in Fig. 1. The AJMS is a device that can transform the pulverized material into fine particles particularly from submicron to several microns. As a result, the classified particle becomes smaller and the classification efficiency becomes higher once the centrifugal force
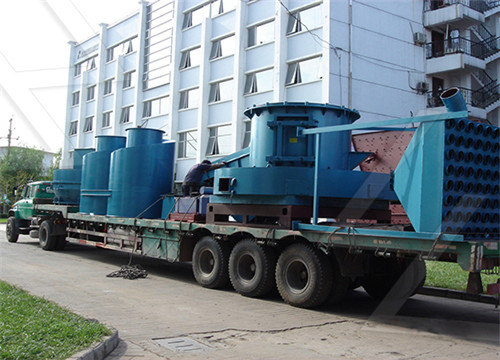
Impact of the powder flow behavior on continuous fine grinding
2018年11月1日1. Introduction. The energy efficiency of dry fine grinding processes can mainly be increased by either (1) further development of mills and mill equipment, (2) improving classifiers as well as grinding-classifying-circuits or (3) enhancing the process behavior of the ground material (Scheibe et al., 1978).Since the demand on fine and ultra
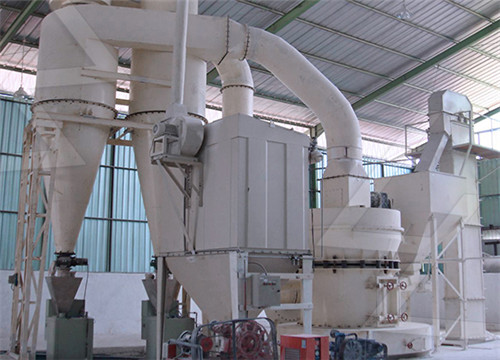
Classifying NETZSCH GrindingDispersing
We carry out the project planning, production and commissioning of individual machines as well as complete classifying plants. NETZSCH Classifying Solutions CFS Fine Classifier CFS/HD-S High-efficiency Fine Classifier InlineStar Inline Classifier SmartRemoval Classifying Laboratory Machines CFS 5CFS 8 Fine Classifier
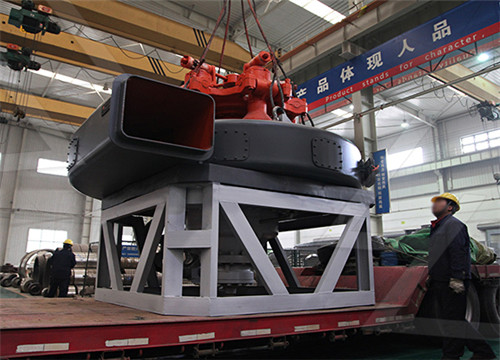
Particle-size reduction Chemical Engineering Page 1
2012年11月1日There are seven types of stresses that can be imparted to achieve size reduction, including the following: • Compression between two rigid surfaces • Compression between surfaces and adjacent bed of solids • Shearing forces by mechanical means (tearing, cleaving, cutting or shredding) • Shearing forces due to surrounding media
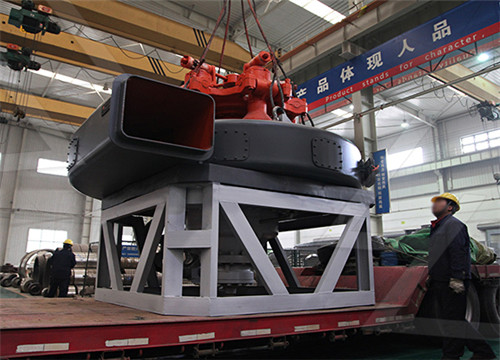
CFS/HD-S High-efficiency Fine Classifier GrindingDispersing
This high efficiency air classifier was developed for ultra-fine, sharp separation, and is often used in conjunction with grinding plants. The optimized classifier wheel geometry produces the finest cut points and high yields that have not been possible with production scale conventional air classifiers with only one classifier wheel.
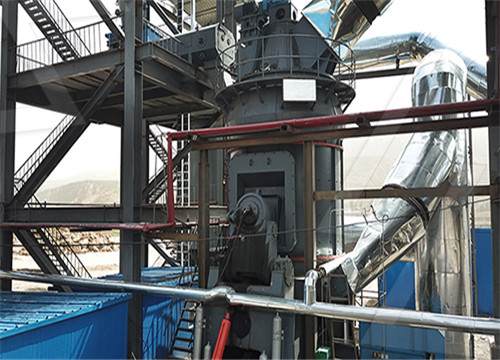
Effect of kinetic comminution parameters and classification efficiency
2000年1月1日Download Citation Effect of kinetic comminution parameters and classification efficiency on output during closed-circuit cement grinding, Part 2 The simulation of closed-circuit grinding was
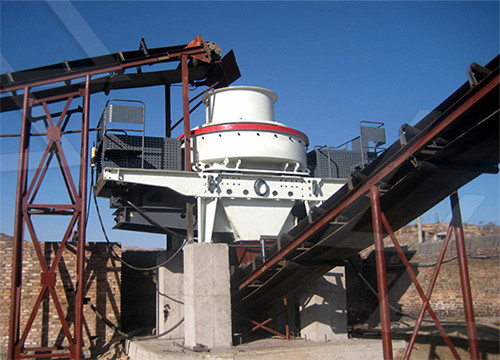
3 Important Indicators In Grinding And Classification Stage
In this post you're going to know about the important indicators in grinding and classification stage and what influences these indicators. This post includes 3 important indicators: grinding fineness. grinding capacity. grinding classification efficiency. So if you want to learn more about grinding and classifaction,you'll love this post.
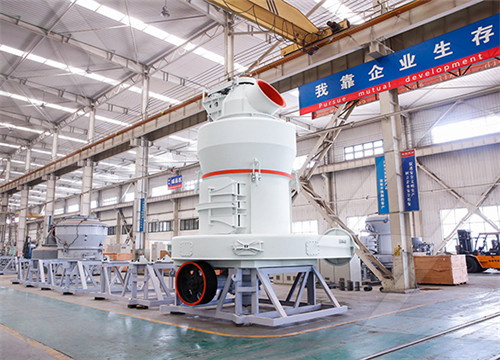
Ways to Improve Classifying Efficiency_ahhli4007的博客-CSDN博客
2012年8月25日The basic components of the grinding and classification process control system : (1) grinding and classification process control system.which is composed of the following three basic control aspects: given control of the amount of ore grinding concentration control, grading the indiscriminate flow concentration (particle size) control.
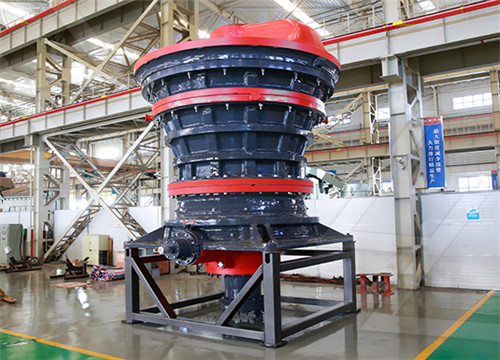
Ball Charge and Grinding Efficiency Grinding
The volume of grinding media in a mill is directly related to grinding efficiency. The higher the volume of grinding media the more effective the grind. Balls must be added to maintain the media load and mill power
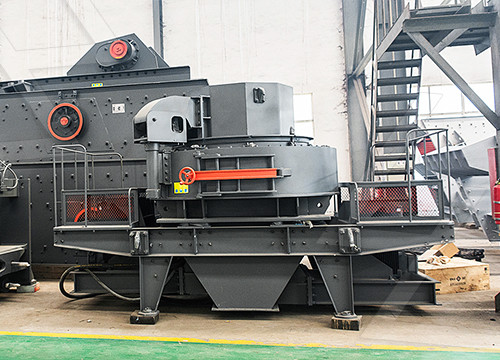
What Factors Will Influence Ball Mill Grinding
2021年3月26日Ball mill grinding efficiency is influenced by many factors: ore grindability, feed size, grinding product size, ball mill diameter and length, ball mill working speed, liner type, steel ball loading system,

Grinding Classifying Drying Grinding Classifying Efficient
3. grinding and classifying efficiency. the efficiency in the grinding and classification stage mainly refers to the grinding efficiency, that is, the amount of ore processed by electric energy per kilowatt hour consumed, also known as. > Consider Wet Or Dry Grinding Milling Process.
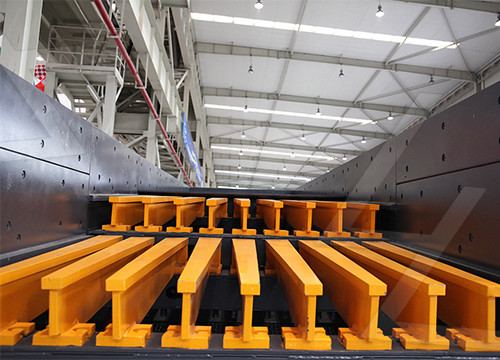
Classifying System
classifying system is a new generation of high-efficiency sorting equipment independently developed by Guilin Hongcheng. It mainly includes LFX series sorting machines and FW series sorting machines, covering powder sorting functions from 80 mesh D97 to 3000 mesh D97. The whole system has fast material flow, high classification accuracy, convenient
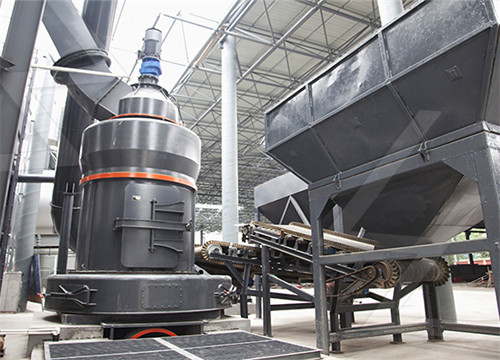
Protein Shifting and Enrichment with the use of Dry Grinding
2020年5月19日Fine grinding Fracturing of united cell structures with the aim of separating the starch granules from the proteins. The result are singular starch and protein granules as well as cell fragments gained from protein granules that partially contain starch granules.Classifying Efficient separati...
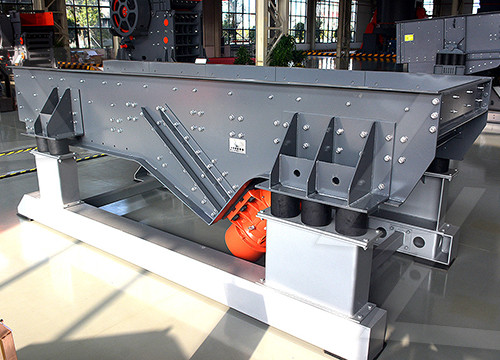
Industrial application of system integration updated technology
The CFD theoretical simulation calculation results show that compared with the original straight blades, the U-shaped blades reduce the resistance by 30%, improve the classifying efficiency by 9.13%, and reduce the vertical mill cycle load by 312% under the same working conditions.