Iron Mining Wet Crusher Process Description

11.19.2 Crushed Stone Processing and Pulverized
11.19.2.1 Process Description 24, 25 Crushed Stone Processing primary crusher. Jaw, impactor, or gyratory crushers are usually used for initial reduction. The ground material and return oversized material that can be pulverized using either wet or dry processes.
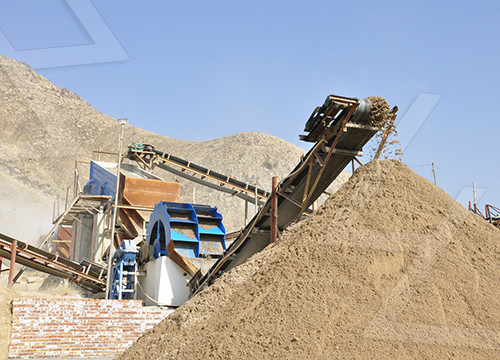
Iron Mining Process Minnesota Iron
At the processing plant, the taconite is crushed into very small pieces by rock crushing machines. The crushers keep crushing the rock until it is the size of a marble. The rock
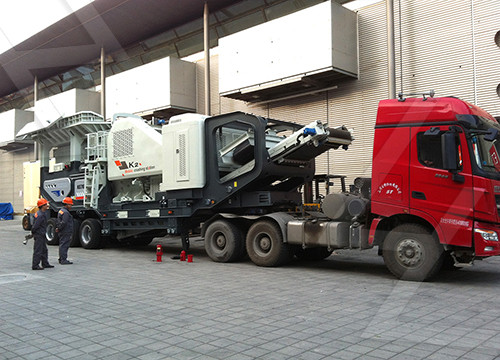
The six main steps of iron ore processing Multotec
Screening. We recommend that you begin by screening the iron ore to separate fine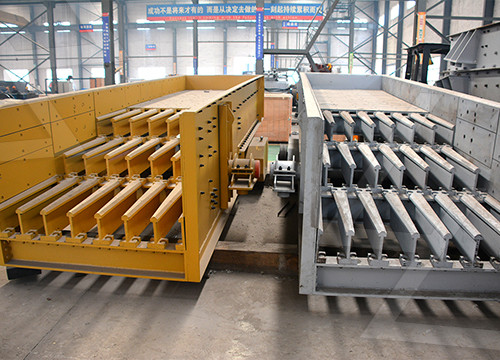
Iron processing Definition, History, Steps, Uses,Facts
Iron (Fe) is a relatively dense metal with a silvery white appearance and distinctive magnetic properties. It constitutes 5 percent by weight of the Earth’s crust, and it is the fourth most
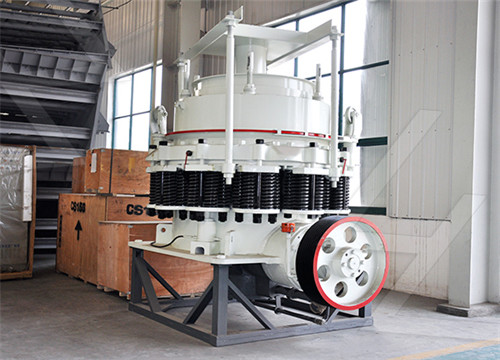
11.24 Metallic Minerals Processing US EPA
The emission factors in Tables 11.24-1 and 11.24-2 are for the process operations as a whole. At most metallic mineral processing plants, each process operation requires
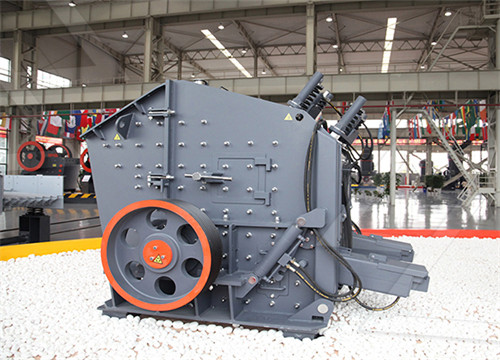
Iron Mining Process Equipment Flow Cases JXSC
Iron Ore Mining Process. 1. Large raw iron ore for primary crushing are fed into the jaw crusher by Plate feeder and are reduced to 8 inches or smaller. After first crushing, the
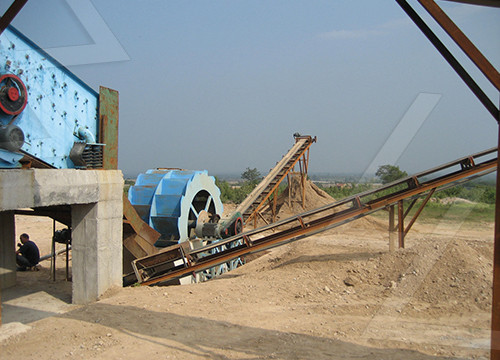
Rock Crushing Process in Mining Mineral ProcessingMetallurgy
2015年7月18日Rock Crushing Process in Mining Let’s follow a rock through a crushing cycle to see what variables will have to be controlled. First the rock will enter the crushing
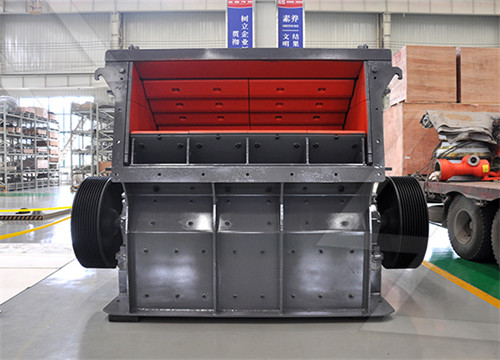
Process Description and Abbreviated History of
Wet concentrate is dried, then melted in electric furnaces, and excess iron sulphides are removed in the ACP converter. A slag-cleaning furnace treats gangue from the converter,
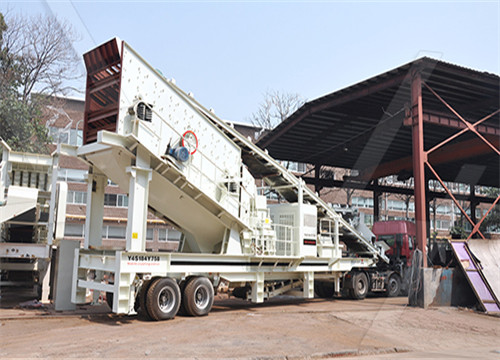
Our Mining Process Iron Ore Company of Canada
Our Mining Process Iron Ore Company of Canada. What We Do. IOC’s operations are integrated across our mine and processing plant in Labrador City, Newfoundland and
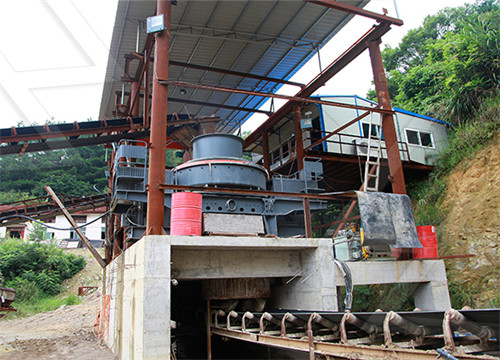
Crushing Metso Outotec
The crushers are built to perform with the lowest cost per ton, featuring a unique combination of crusher cavity design, crushing forces, reliability and safety. Engineered
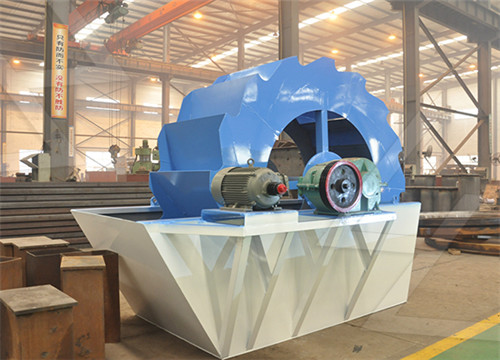
11.19.2 Crushed Stone Processing and Pulverized Mineral
11.19.2.1 Process Description 24, 25 Crushed Stone Processing primary crusher. Jaw, impactor, or gyratory crushers are usually used for initial reduction. The ground material and return oversized material that can be pulverized using either wet or dry processes. The classifier can either be associated with the grinding operation, or it
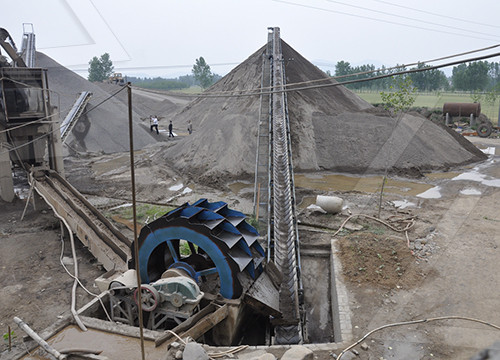
Iron Ore production in the Pilbara Rio Tinto
Process Processing of the ore ranges from simple crushing and screening to a standard size, through to processes that beneficiate or upgrade the quality of the iron ore products. This is done by physical processes, which remove impurities by differences in particle density or size gravity or size separation. Processing may be wet or dry.
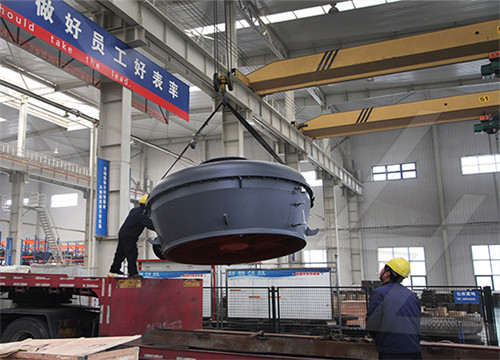
Iron Mining Process Minnesota Iron
The iron ore is separated from the taconite using magnetism. The remaining rock is waste material and is dumped into tailings basins. The taconite powder with the iron in it is called concentrate. Pellets The concentrate (the wet taconite powder) is rolled with clay inside large rotating cylinders.
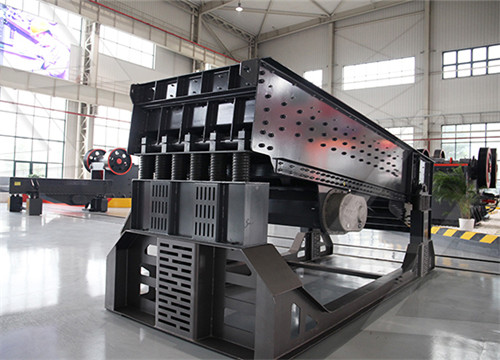
Roller crushers in iron mining, how does the degradation of
2021年4月1日Currently, in the mining process, roller crushers have been playing an important role due to their high productivity displayed in iron ore mining, as an example is an iron ore mine with friable hematite lithology and among others with uniaxial compression resistance of up to 200 MPa and Bond abrasiveness of up to 0, 37 g.
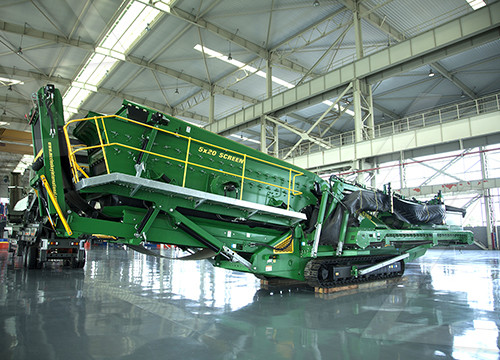
Iron Ore AnalysisProcess Optimization Solutions
2017年7月27日During the entire iron ore production process, we deliver tailored analytical solutions for exploration geologists, mine planners, process engineers as well as for geometallurgists and quality managers. Improve recovery rates and Iron ore beneficiation Watch on Iron ore mining Predictive real-time analysis in the mine Learn
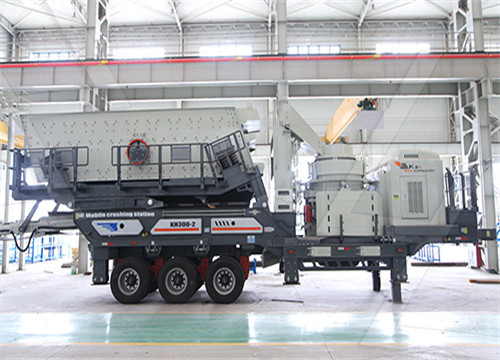
Process Description and Abbreviated History of Anglo
Wet concentrate is dried, then melted in electric furnaces, and excess iron sulphides are removed in the ACP converter. A slag-cleaning furnace treats gangue from the converter, while a slag milling and flotation circuit treats the slag from the electric furnaces. The concentrate handling section currently treats around 72 000 t of wet
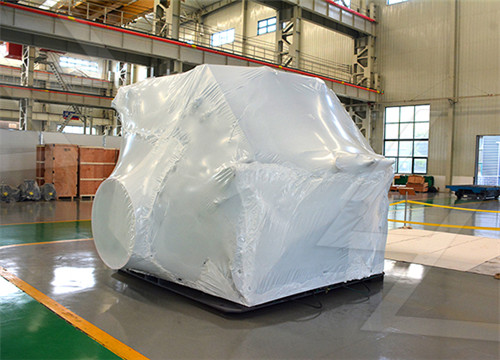
12.5 Iron And Steel Production US EPA
lance with high-pressure nitrogen. The process duration varies with the injection rate, hot metal chemistry, and desired final sulfur content, and is in the range of 5 to 30 minutes. 12.5.1.4 Steelmaking Process — Basic Oxygen Furnaces In the basic oxygen process (BOP), molten iron from a blast furnace and iron scrap are refined
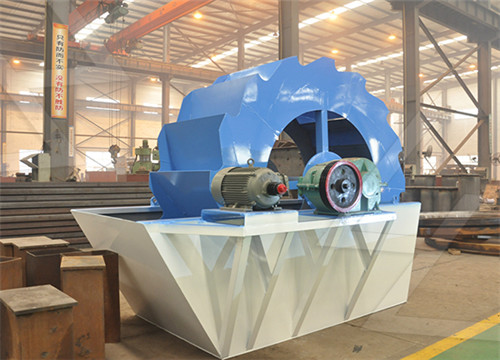
BENEFICIATION OF IRON ORE National Institute of
A part of the ROM ore is beneficiated by Wet process while the other part of the ROM ore is beneficiated by the Dry process. In the Wet process, the feed ROM of-1200mm size is feed to primary crusher by Mining Department through 100T dumper, 3.4 Process Description The jigging process produces iron ore concentrate (-10mm)
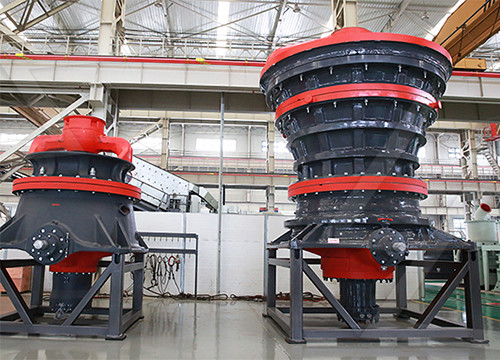
Minerals Free Full-Text Economic and Socio-Environmental
2020年10月26日In our previous studies, we demonstrated the performance of novel superfine crusher and pneumatic planar magnetic separator as energy-efficient technologies for dry processing of magnetite ores. The present study investigates the economic and socio-environmental benefits of applying these technologies in conceptual
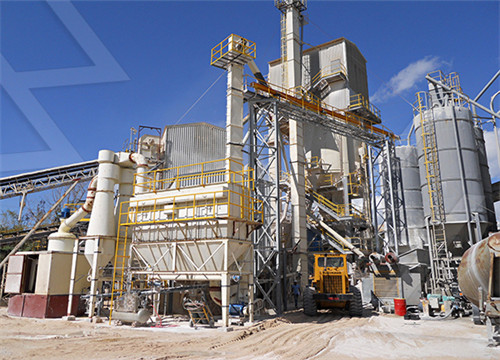
sbmchina/sbm malawi mining grinding.md at main github
Contribute to sbmcrushers/sbmchina development by creating an account on GitHub.
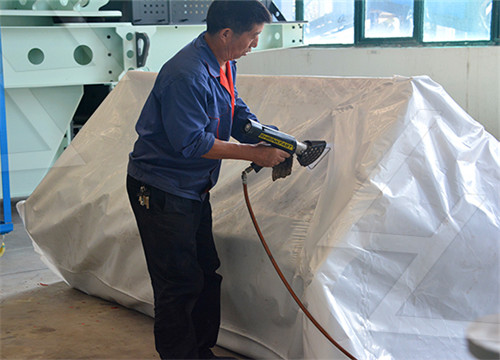
Mining and processing plant engineering design
ESFC, an international company, offers financing and engineering design for mining and processing plants under an EPC contract, including research, development of individual technical solutions, etc.
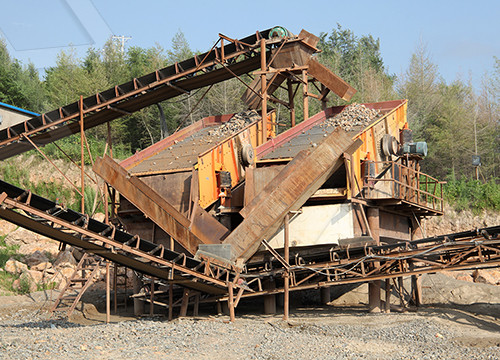
What Type of Crusher Is Best for Primary Crushing?
2021年3月25日The crusher can handle the all-in feed. The gradation is controlled by adjusting the spacing between the mantle and the concaves at their closest point. For a smaller product size, the main shaft can be raised to create a smaller space between the mantle and the liners.
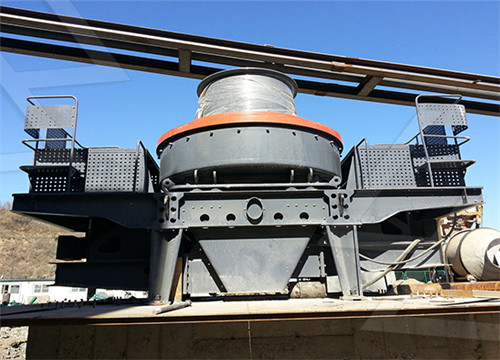
Iron ore BHP
There are four main types of iron ore deposit: massive hematite, which is the most commonly mined, magnetite, titanomagnetite, and pisolitic ironstone. These ores vary in colour from dark grey, bright yellow, or deep purple to rusty red. Iron is responsible for the red colour in many of our rocks and the deep red sands of the Australian deserts.
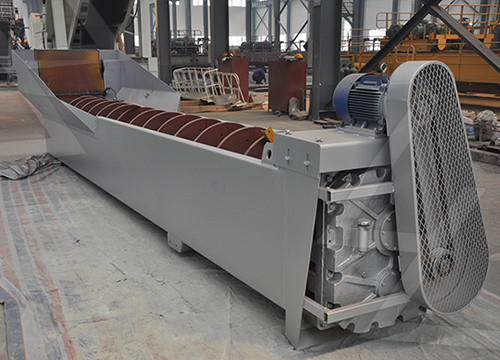
Rock Crusher Eastman Rock Crusher
Which hammer crusher can crush iron ore (100TPH)? Understanding the stages of crushing process and the types of crushers that best fit each stage can simplifies your equipment selection. Each type of crusher is different and used to achieve a certain end result. Dry or wet and sticky: 3/1 to 5/1: Heavy mining, quarried materials, sand
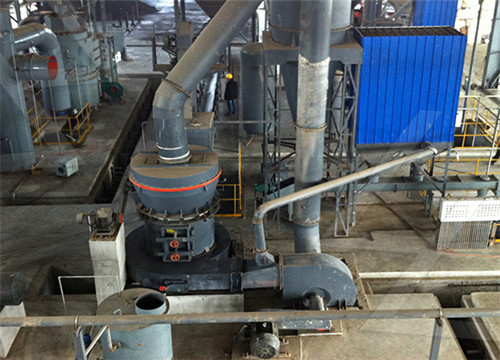
11.19.2 Crushed Stone Processing and Pulverized Mineral
11.19.2.1 Process Description 24, 25 Crushed Stone Processing primary crusher. Jaw, impactor, or gyratory crushers are usually used for initial reduction. The ground material and return oversized material that can be pulverized using either wet or dry processes. The classifier can either be associated with the grinding operation, or it
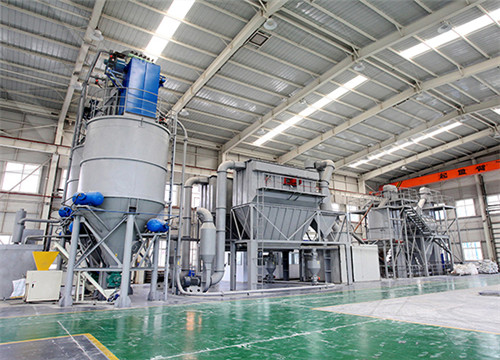
Iron Ore production in the Pilbara Rio Tinto
Process Processing of the ore ranges from simple crushing and screening to a standard size, through to processes that beneficiate or upgrade the quality of the iron ore products. This is done by physical processes, which remove impurities by differences in particle density or size gravity or size separation. Processing may be wet or dry.
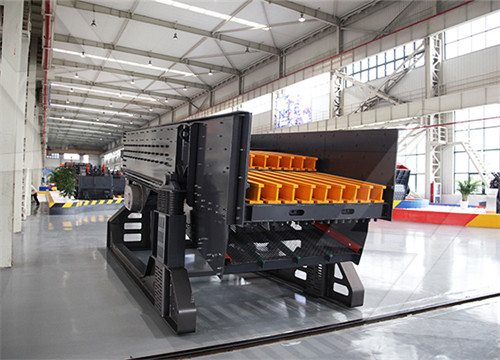
Iron ore BHP
There are four main types of iron ore deposit: massive hematite, which is the most commonly mined, magnetite, titanomagnetite, and pisolitic ironstone. These ores vary in colour from dark grey, bright yellow, or deep purple to rusty red. Iron is responsible for the red colour in many of our rocks and the deep red sands of the Australian deserts.
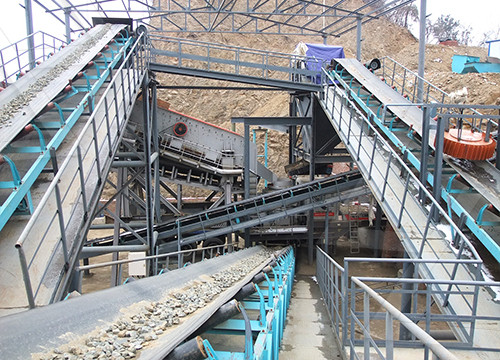
Roller crushers in iron mining, how does the degradation of
2021年4月1日Currently, in the mining process, roller crushers have been playing an important role due to their high productivity displayed in iron ore mining, as an example is an iron ore mine with friable hematite lithology and among others with uniaxial compression resistance of up to 200 MPa and Bond abrasiveness of up to 0, 37 g.
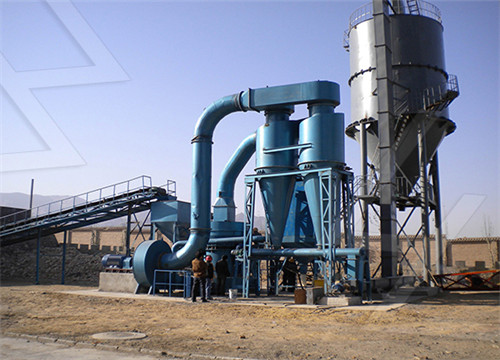
Process Description and Abbreviated History of Anglo
Wet concentrate is dried, then melted in electric furnaces, and excess iron sulphides are removed in the ACP converter. A slag-cleaning furnace treats gangue from the converter, while a slag milling and flotation circuit treats the slag from the electric furnaces. The concentrate handling section currently treats around 72 000 t of wet
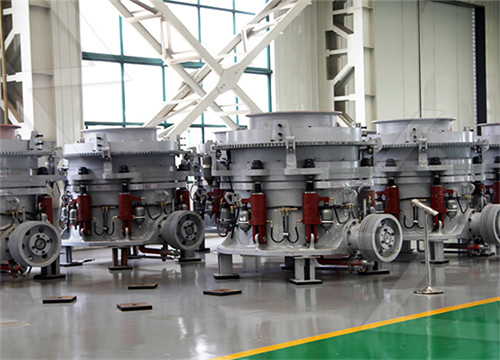
12.5 Iron And Steel Production US EPA
lance with high-pressure nitrogen. The process duration varies with the injection rate, hot metal chemistry, and desired final sulfur content, and is in the range of 5 to 30 minutes. 12.5.1.4 Steelmaking Process — Basic Oxygen Furnaces In the basic oxygen process (BOP), molten iron from a blast furnace and iron scrap are refined
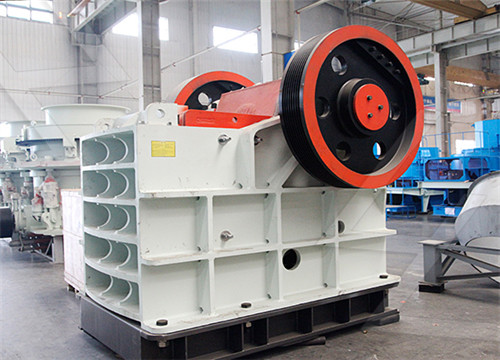
BENEFICIATION OF IRON ORE National Institute of
A part of the ROM ore is beneficiated by Wet process while the other part of the ROM ore is beneficiated by the Dry process. In the Wet process, the feed ROM of-1200mm size is feed to primary crusher by Mining Department through 100T dumper, 3.4 Process Description The jigging process produces iron ore concentrate (-10mm)
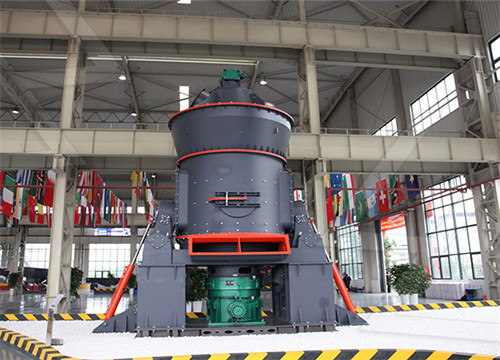
Minerals Free Full-Text Economic and Socio-Environmental
2020年10月26日In our previous studies, we demonstrated the performance of novel superfine crusher and pneumatic planar magnetic separator as energy-efficient technologies for dry processing of magnetite ores. The present study investigates the economic and socio-environmental benefits of applying these technologies in conceptual
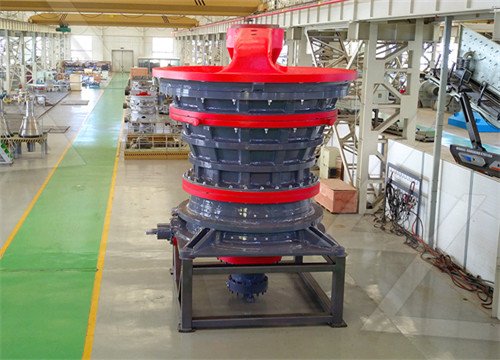
Mining and processing plant engineering design
ESFC, an international company, offers financing and engineering design for mining and processing plants under an EPC contract, including research, development of individual technical solutions, etc.

sbmchina/sbm malawi mining grinding.md at main github
Contribute to sbmcrushers/sbmchina development by creating an account on GitHub.
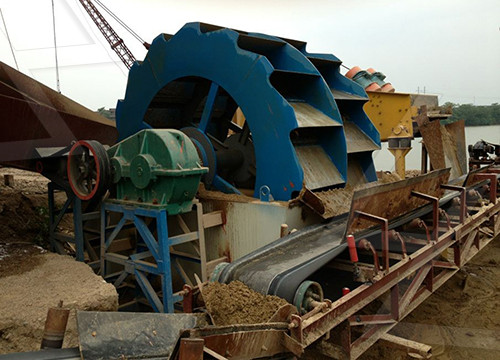
Sand WashingWaste Recycling Wet Processing Solutions CDE
CDE is the world's number one wet processing equipment company for sand and aggregates, mining, C&D waste recycling and wastewater solutions. Learn more. +44 28 8676 7900. solution helps Garrick Bros to extract a range of aggregates and manufactured sands for construction applications from crusher dust.
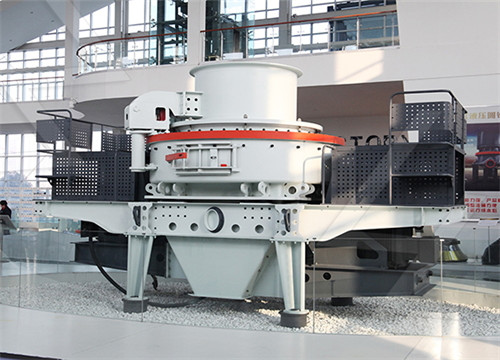
Rock Crusher Eastman Rock Crusher
Which hammer crusher can crush iron ore (100TPH)? Understanding the stages of crushing process and the types of crushers that best fit each stage can simplifies your equipment selection. Each type of crusher is different and used to achieve a certain end result. Dry or wet and sticky: 3/1 to 5/1: Heavy mining, quarried materials, sand
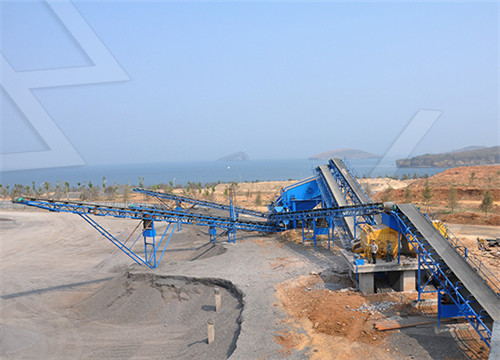
Cone crusher basics in 4 minutes SRP
This is the starting point for understanding how cone crushers work and how they can make your mine or quarry more productive. Elsewhere on the site you can find detailed information about all aspects of crushing and screening, but to make sense of these it helps to understand the basics of cone crushing. That’s what you’ll find here!