Report On Cement Grinding Optimisation
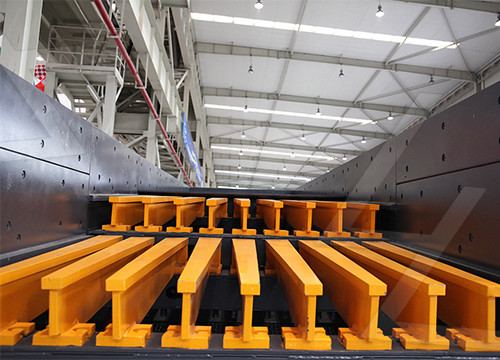
Energy and cement quality optimization of a cement
2018年7月1日Energy optimization of a circuit has been subject of many of the studies. Jankovic et al. [12] considered the optimization alternatives of cement grinding

[PDF] Cement grinding optimisation Semantic Scholar
2004年11月1日The Optimization of Calcareous Fly Ash-Added Cement Containing Grinding Aids and Strength-Improving Additives G. Kaplan, S. Yildizel, S. Memiş, A.
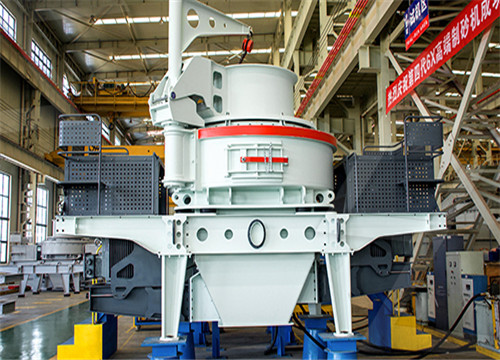
进一步探索
(PDF) Cement grinding optimisation Alex Jankovic AcaCement grinding optimisation Request PDF根据热度为您推荐•反馈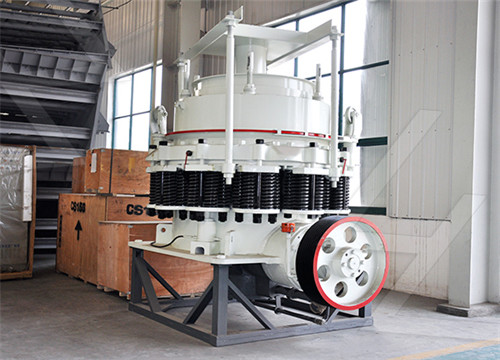
Cement grinding optimisation Request PDF
2004年11月1日The electrical energy consumed in cement production is approximately 110kWh/tonne, and around 40% of this energy is consumed for clinker grinding. There
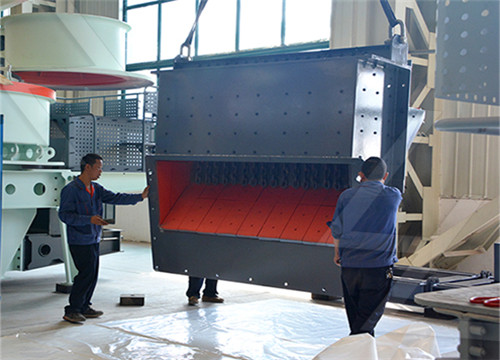
(PDF) Performance Evaluation of Vertical Roller Mill in
2017年9月11日The cement grinding circuits are operated at high flow rates hence high amount of circulating loads occur within the system.
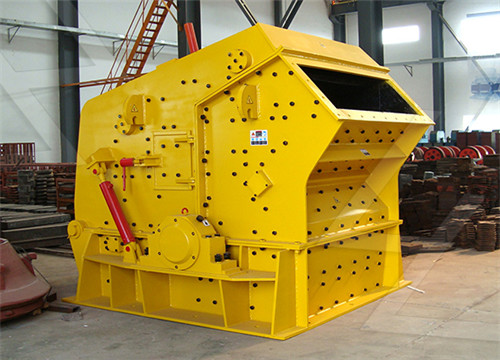
PROCESS DIAGNOSTIC STUDIES FOR CEMENT MILL
HOLTEC has undertaken Performance Optimisation of the cement grinding circuits by doing process diagnostic studies in many cement plants. The stone describes the
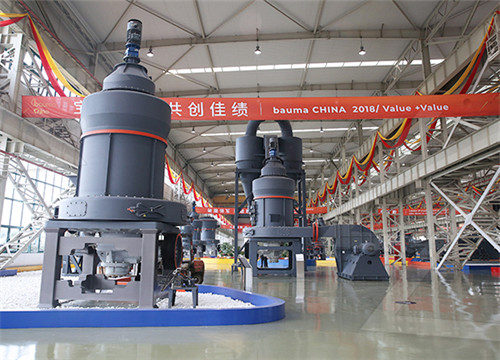
Cement plant performance optimization Benchmarking,
Cement process analysis, diagnostics and optimization Starting point: Advanced process control portfolio in cement ABB has extensive cement process know-how acquired
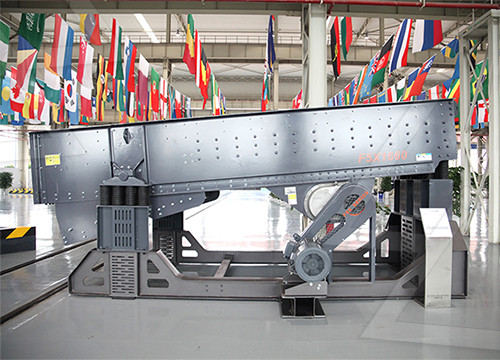
Grinding Optimisation Library
Vertical Roller Mills (VRMs) VRM Optimisation. The difference in performance between ball mill and VRM cement is largely due to process factors. The observed performance
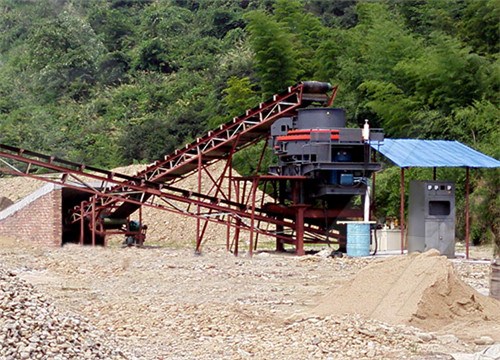
Cement Grinding Optimization PDF Mill (Grinding)
高达$3返现Cement Grinding Optimization Free download as Word Doc (.doc / .docx), PDF File (.pdf), Text File (.txt) or read online for free. Cement Grinding Optimization
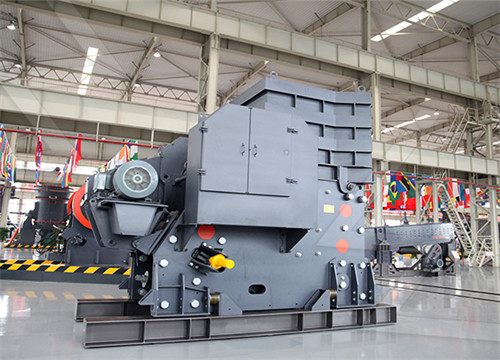
Simulation and Optimization of an Integrated Process
2021年3月9日In this study the process flow diagram for the cement production was simulated using Aspen HYSYS 8.8 software to achieve high energy optimization and
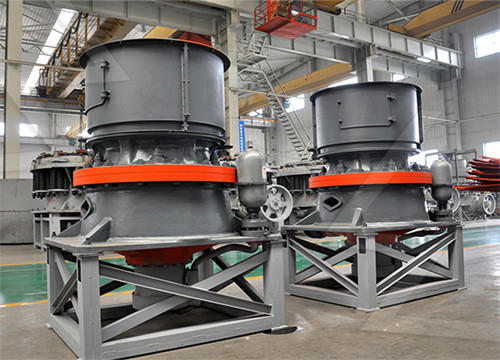
Cement grinding optimisation ScienceDirect
2004年11月1日To optimise cement grinding, standard Bond grinding calculations can be used as well as modelling and simulation techniques based on population balance model (PBM). Mill power draw prediction can be carried out using Morrell’s power model for tumbling mills. 3.1. Bond method
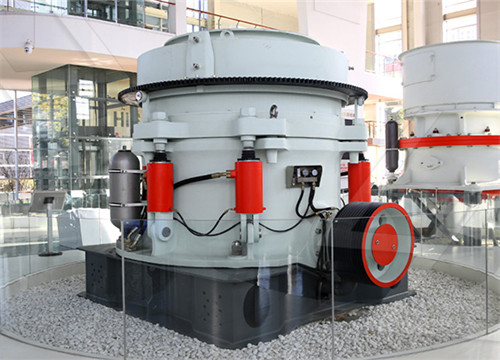
Cement grinding optimisation ScienceDirect
2004年11月1日Grinding process modelling and simulation methods can be used for optimisation. A case study conducted using the data from an industrial cement plant indicates that: • Pre-crushing of cement clinker using a Barmac crusher offers realistic benefits to a cement plant in terms of process efficiency. •
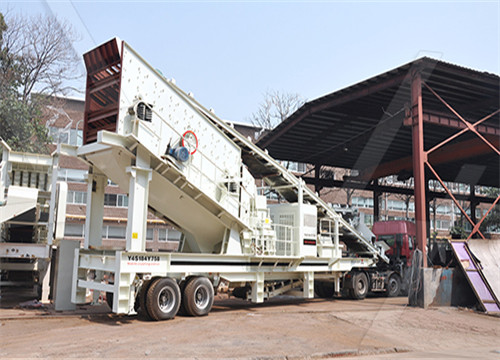
Cement grinding optimisation Request PDF
2004年11月1日The electrical energy consumed in cement production is approximately 110kWh/tonne, and around 40% of this energy is consumed for clinker grinding. There is potential to optimise conventional...
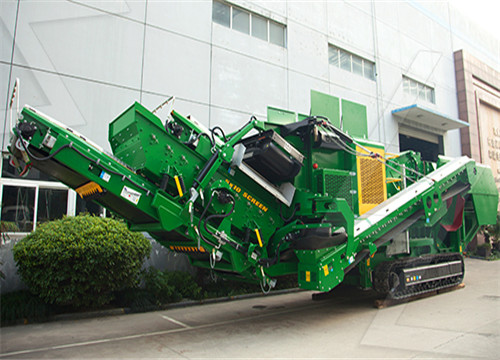
(PDF) Performance Evaluation of Vertical Roller Mill
2017年9月11日Grinding and separation efficiency of vertical roller mill were evaluated. In addition to these, performance figures of vertical roller mill and conventional closed ball mill circuit were...
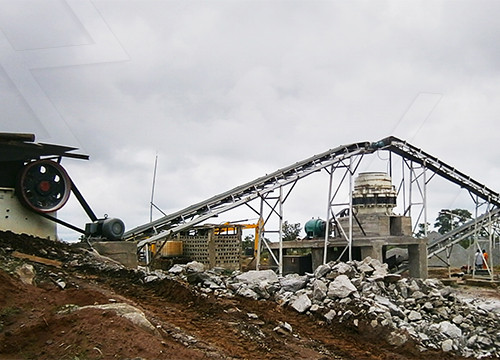
Cement plant performance optimization Benchmarking,
Cement process analysis, diagnostics and optimization Starting point: Advanced process control portfolio in cement ABB has extensive cement process know-how acquired through decades of collaboration with leading customers of this industry. In particular, process optimization has been one area where ABB has excelled with hundreds of kilns, mills and
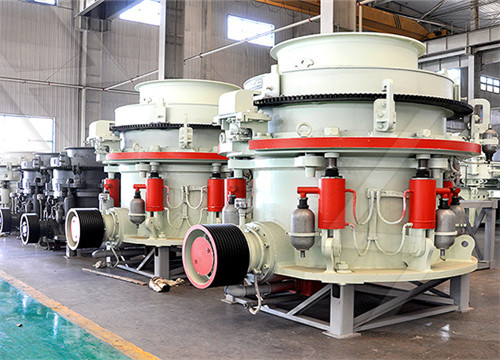
OPTIMIZATION OF CEMENT GRINDING OPERATION IN
Condition in one of the grinding chambers of the mill . Results of Optimization . The graphical analysis presented in Figure 2 represents progress of grinding along the length of the mill after optimizing the grinding process. rogress of grinding is clearly visible in Desired p the graphs. Figure -2: Analysis of longitudinal samples.
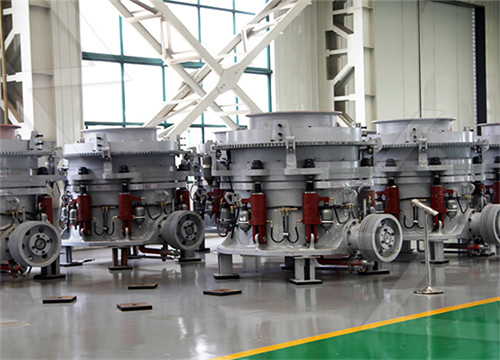
GRINDING OPTIMISATION Combining forces
Upgrading cement grinding systems offers both process and commercial benefits. The use of a high-pressure grinding roll in semi-finish grinding mode significantly reduces and space. Therefore, Germany-based Maschinenfabrik Köppern has developed a compact air classifier that enables grinding system upgrades by integrating only one combined
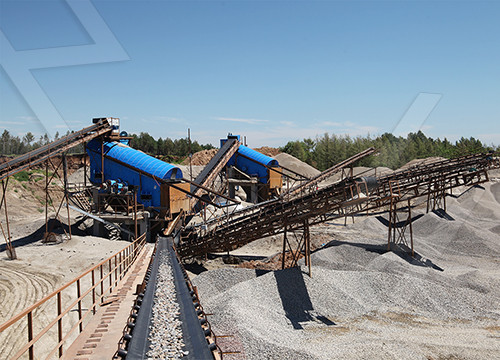
CiteSeerX — CEMENT GRINDING OPTIMISATION Pennsylvania
This stone describes the tools available for the analysis and optimisation of cement grinding circuits. The application of the Bond based methodology as well as Population Balance Models (PBM) is presented using a case study. The throughput of current conventional closed grinding circuit can be increased by 10-20 % by pre-crushing the
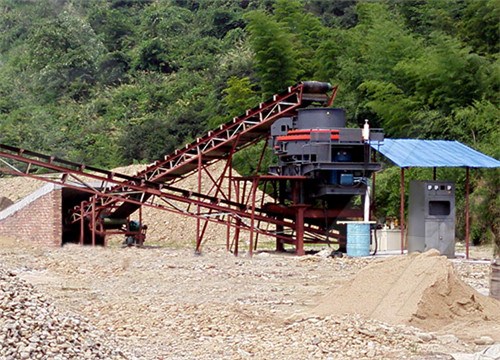
LOW-CARBON CEMENTS Admixtures and sustainability
kWh/ton cost (US$/t of cement) 2.40 2.14 R&M cost (US$/t of cement) 0.40 0.36 Annual saving 0.65Mta ≈US$528,000. New cement additives to help stabilize vertical roller mills (VM) and reduce water injection. Effective for reducing cement pre-hydration and improving cement quality and performance, such as: Grinding aids for vertical roller
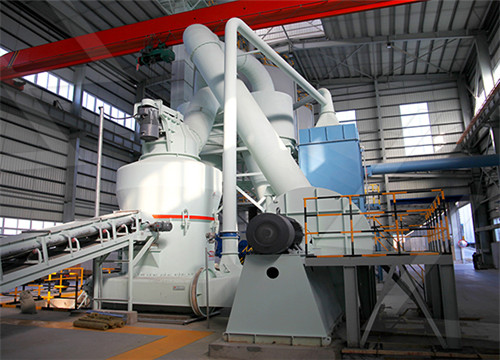
Grinding optimization Magotteaux
Cement plants and grinding optimization The matter of grinding optimization is important in any cement plant. Controlling cost and quality of the finished products is important in staying operational. Magotteaux´s
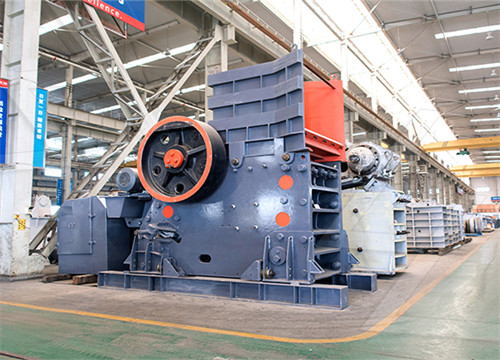
Digitization and the future of the cement plant McKinsey
2020年9月16日According to our analyses, the cement plant of the future could reduce emissions by up to 75 percent by 2050 compared with 2017. Around 20 percent will come from operational advances, such as energy-efficiency measures and clinker substitution.
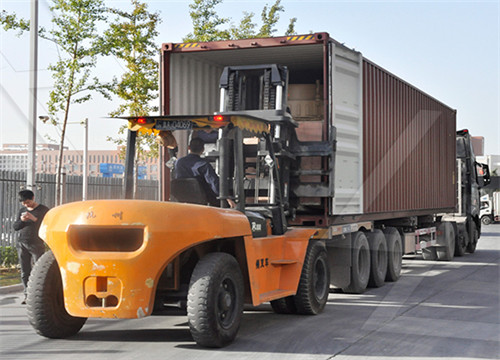
Industrial : Optimization for the Cement Industry ABB
Cement Kiln Optimization Controlling a cement rotary kiln is a very difficult task. The process is intrinsically unstable and there are long time delays and large pertur-bations acting on it. Only a perfect mix of expe-rience, deep knowledge, mathematical tech-niques and state-of-the-art software can achieve optimal behaviour over long periods
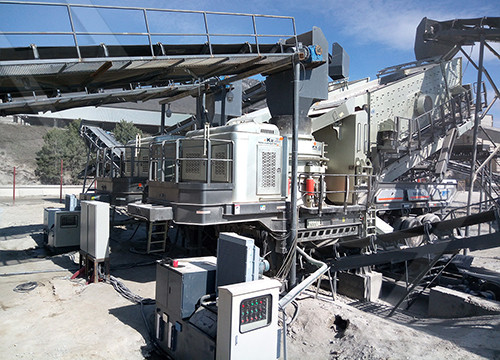
Ball mill media optimization Metcom Tech
mill grinding rate over the material’s grindability as measured in the lab. Mill percent solids optimization has thusly been achieved (McIvor et al., 2000). For media sizing, maximizing the mill grinding rate on a given ore is equivalent to maximizing the mill grinding efficiency. Ores of different grindability will be part of the discussion.
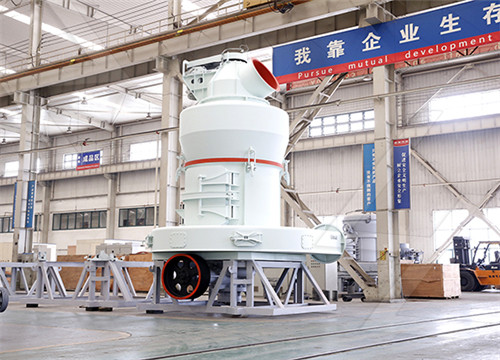
Ambuja Cement − Annual Report 2021-22
Optimisation of kiln and cement grinding mill to reduce power consumption from 61.4 to 60.2 kWh/t of clinker in kiln and 37.4 to 36.0 kWh/t of cement Grinding; PLANTS OF TOMORROW. Our investment in Industry 4.0 under the ‘Plants of Tomorrow’ programme is part of Holcim’s Strategy for Growth 2022. The initiative aims to make manufacturing
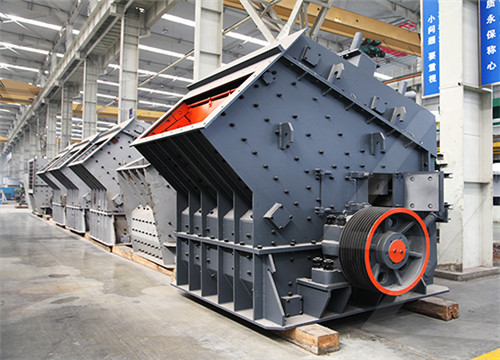
Cement grinding optimisation ScienceDirect
2004年11月1日The current world consumption of cement is about 1.5 billion tonnes per annum and it is increasing at about 1% per annum. The electrical energy consumed in cement production is approximately 110. kWh/tonne, and around 40% of this energy is consumed for clinker grinding.. There is potential to optimise conventional cement
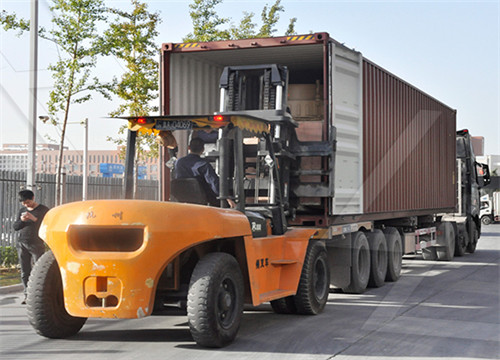
Cement grinding optimisation ScienceDirect
2004年11月1日Grinding process modelling and simulation methods can be used for optimisation. A case study conducted using the data from an industrial cement plant indicates that: • Pre-crushing of cement clinker using a Barmac crusher offers realistic benefits to a cement plant in terms of process efficiency. •
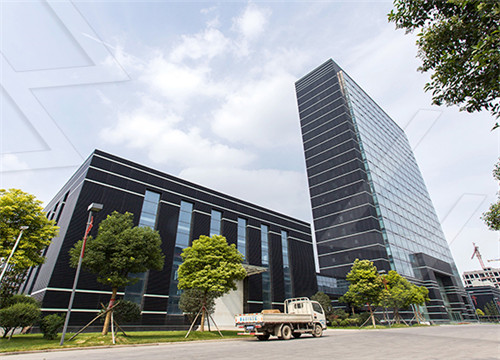
Cement plant performance optimization Benchmarking,
Cement process analysis, diagnostics and optimization Starting point: Advanced process control portfolio in cement ABB has extensive cement process know-how acquired through decades of collaboration with leading customers of this industry. In particular, process optimization has been one area where ABB has excelled with hundreds of kilns, mills and
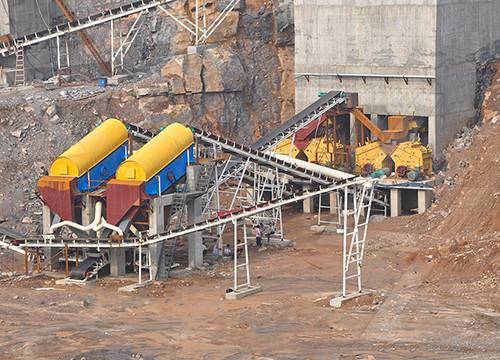
GRINDING OPTIMISATION Combining forces
Upgrading cement grinding systems offers both process and commercial benefits. The use of a high-pressure grinding roll in semi-finish grinding mode significantly reduces and space. Therefore, Germany-based Maschinenfabrik Köppern has developed a compact air classifier that enables grinding system upgrades by integrating only one combined
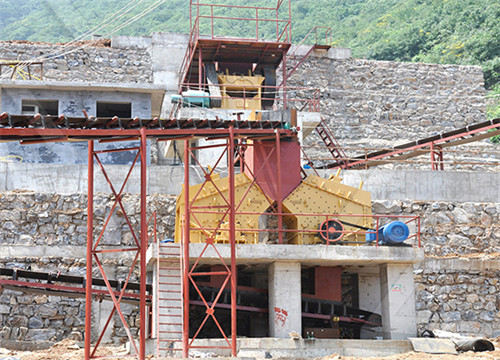
OPTIMIZATION OF CEMENT GRINDING OPERATION IN
Condition in one of the grinding chambers of the mill . Results of Optimization . The graphical analysis presented in Figure 2 represents progress of grinding along the length of the mill after optimizing the grinding process. rogress of grinding is clearly visible in Desired p the graphs. Figure -2: Analysis of longitudinal samples.
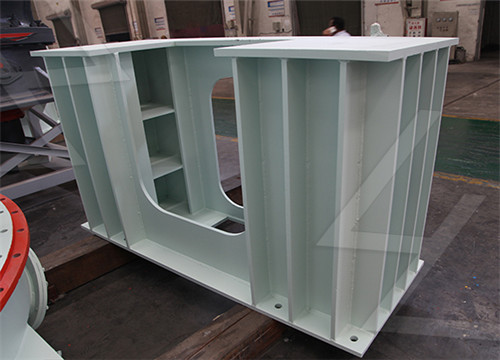
CiteSeerX — CEMENT GRINDING OPTIMISATION Pennsylvania
This stone describes the tools available for the analysis and optimisation of cement grinding circuits. The application of the Bond based methodology as well as Population Balance Models (PBM) is presented using a case study. The throughput of current conventional closed grinding circuit can be increased by 10-20 % by pre-crushing the
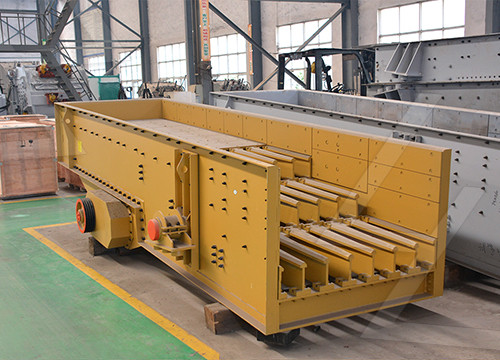
LOW-CARBON CEMENTS Admixtures and sustainability
kWh/ton cost (US$/t of cement) 2.40 2.14 R&M cost (US$/t of cement) 0.40 0.36 Annual saving 0.65Mta ≈US$528,000. New cement additives to help stabilize vertical roller mills (VM) and reduce water injection. Effective for reducing cement pre-hydration and improving cement quality and performance, such as: Grinding aids for vertical roller
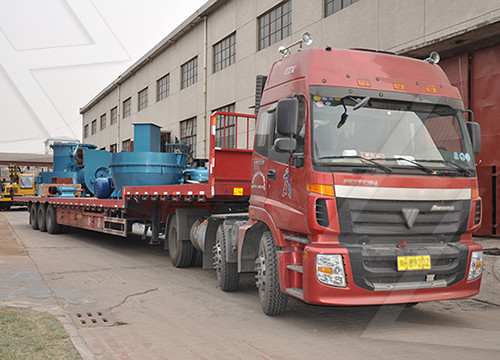
Industrial : Optimization for the Cement Industry ABB
Cement Kiln Optimization Controlling a cement rotary kiln is a very difficult task. The process is intrinsically unstable and there are long time delays and large pertur-bations acting on it. Only a perfect mix of expe-rience, deep knowledge, mathematical tech-niques and state-of-the-art software can achieve optimal behaviour over long periods
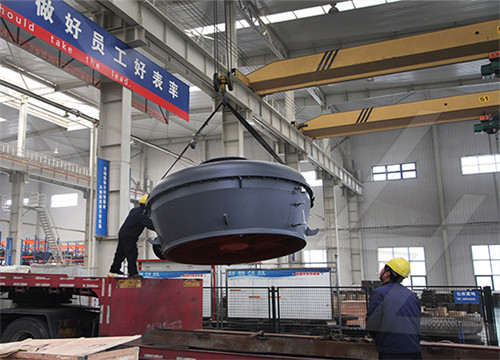
Grinding optimization Magotteaux
Cement plants and grinding optimization The matter of grinding optimization is important in any cement plant. Controlling cost and quality of the finished products is important in staying operational. Magotteaux´s

Cement Grinding Optimisation PDF Scribd
1991年1月1日The increasing demand for “finer cement” products, and the need for reduction in energy consumption and green house gas emissions, reinforces the need for grinding optimisation. This stone describes the
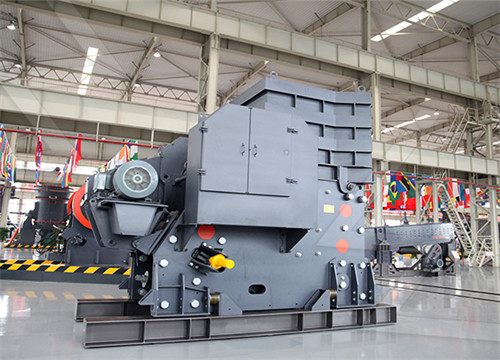
Ball mill media optimization Metcom Tech
mill grinding rate over the material’s grindability as measured in the lab. Mill percent solids optimization has thusly been achieved (McIvor et al., 2000). For media sizing, maximizing the mill grinding rate on a given ore is equivalent to maximizing the mill grinding efficiency. Ores of different grindability will be part of the discussion.
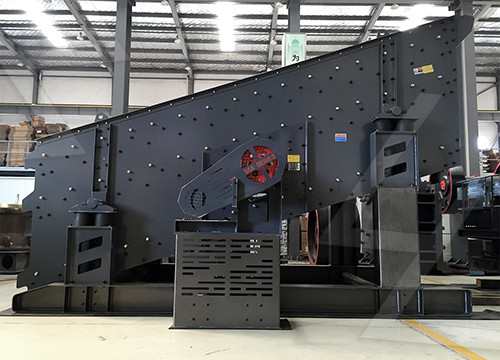
Ambuja Cement − Annual Report 2021-22
Optimisation of kiln and cement grinding mill to reduce power consumption from 61.4 to 60.2 kWh/t of clinker in kiln and 37.4 to 36.0 kWh/t of cement Grinding; PLANTS OF TOMORROW. Our investment in Industry 4.0 under the ‘Plants of Tomorrow’ programme is part of Holcim’s Strategy for Growth 2022. The initiative aims to make manufacturing
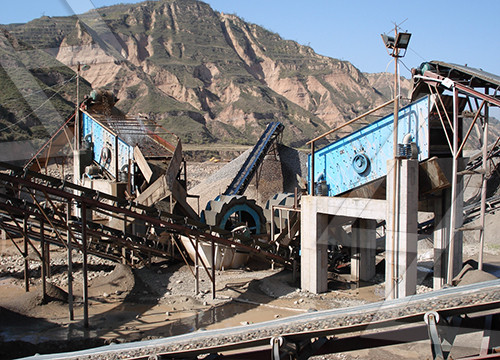
report on cement grinding optimisation-Vertical roller mill optimisation
Vertical roller mill optimisation International Cement Report On Cement Grinding Aid Trial
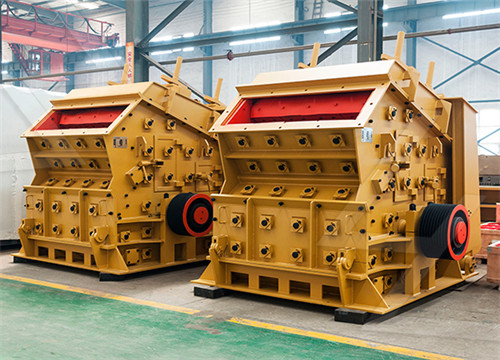
ABB Ability Expert Optimizer for cement
Mill optimization Grinding makes up a big portion of the electrical energy consumed on the plant, thus the efficiency of grinding operations has a big influence on your energy bill. EO optimizes your grinding circuit to increase throughput and secure consistent output quality while lowering energy consumption. Material blending