Iron Ore Magnetic Separation Process Pdf
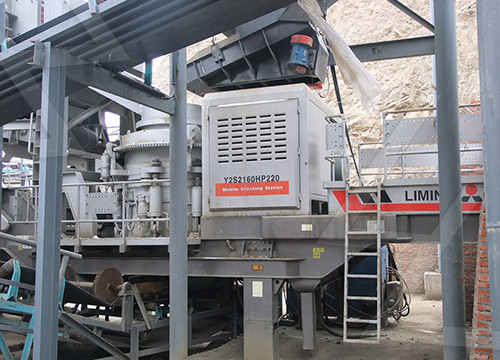
Iron Ore 2nd Edition Elsevier
2021年12月2日DRM-free (EPub, PDF) eBook Format Help. Print Paperback30% off $365.00 $255.50 Chapter 9 Physical separation of iron ore: magnetic separation;

进一步探索
Iron Ore 2nd edition , VitIron Ore 1st Edition根据热度为您推荐•反馈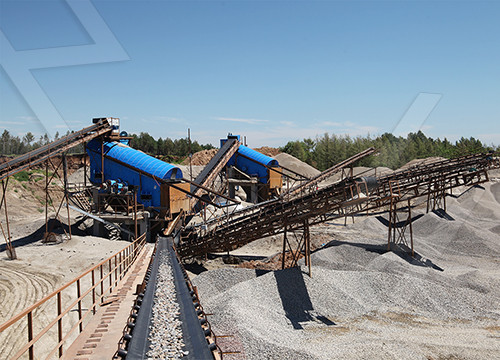
Developments in the physical separation of iron ore:
2015年1月1日Because the crystal water in limonitic ores will report to the iron ore concentrate in magnetic separation, the iron ore concentrate grade is limited to about
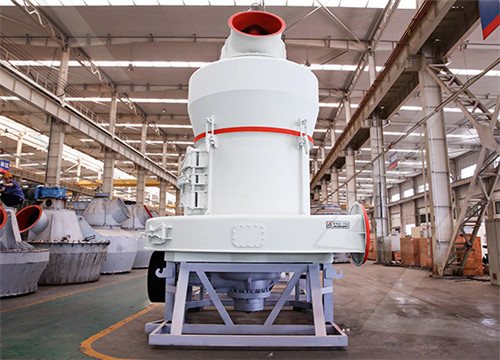
FR SUHFLSLWDWLRQ Institute of Physics
contained in iron ore and characterization using XRD to see crystal structure as well as the grain size of the iron ore. 3. Results and Discussion By using this method of analysis is
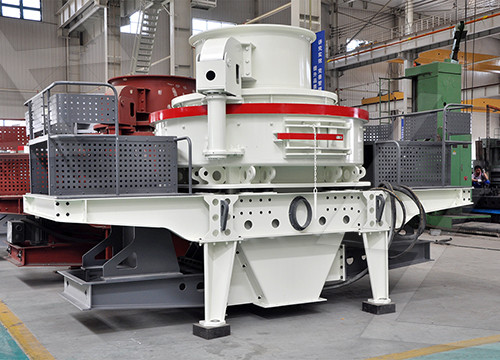
ADVANCES IN MAGNETIC SEPARATION OF ORES
magnetic separation. Dry Magnetic Separation of Iron Ore: There are many inherent advantages in processes that utilize dry magnetic separation to beneficiate iron ore.
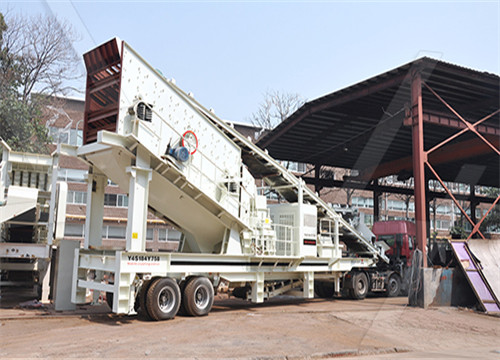
Increasing efficiency of iron ore magnetic separation by using
enhance efficiency of iron ore magnetic separation by applying ultrasonic technologies. Thus, it is required to combine research results in the following directions: theoretical and
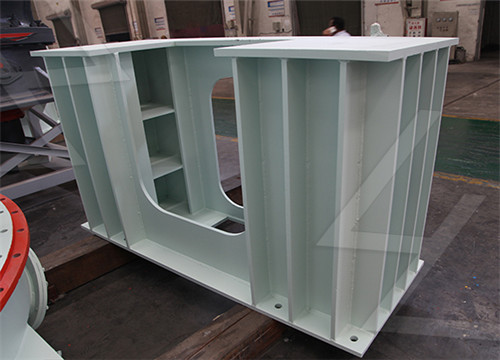
(PDF) Wet High Intensity Magnetic Separation of Iron
1996年1月1日Magnetic separation and flotation are the two commonly used iron beneficiation processes and selecting the most effective process to treat low-grade ore depends mainly on the...
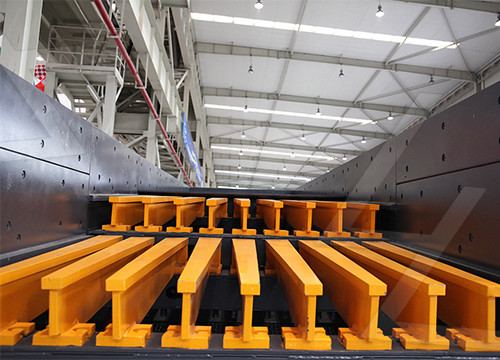
[PDF] Dry Magnetic Separation of Iron Ore of the Bakchar Deposit
In this study, strategies for enrichment of iron ore samples of Demir Export A.Ş. via conventional magnetic separation were evaluated. Fe% and SiO2 % of the iron ore
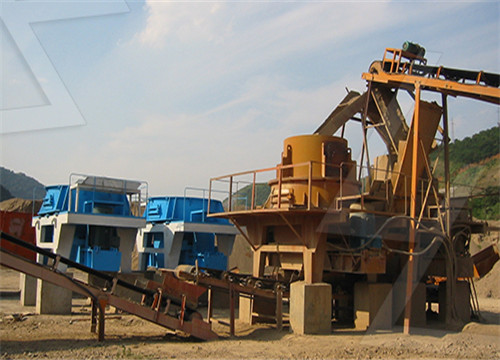
[PDF] HIGH INTENSITY MAGNETIC SEPARATION OF IRON
2010年1月1日The conventional method for processing iron ore is by crushing the run of mine (ROM) material to <40 mm size fraction followed by scrubbing and/or wet screening at 10 mm to generate à40+10 mm...
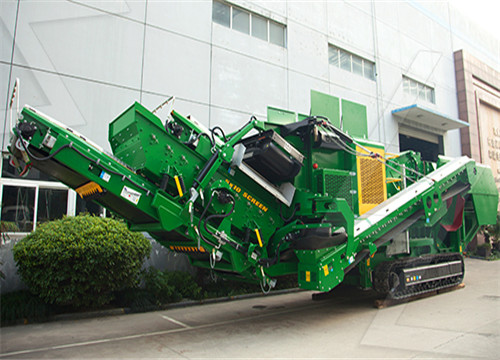
The six main steps of iron ore processing Multotec
Six steps to process iron ore 1. Screening We recommend that you begin by screening the iron ore to separate fine particles below the crusher’s CSS before the crushing stage. A
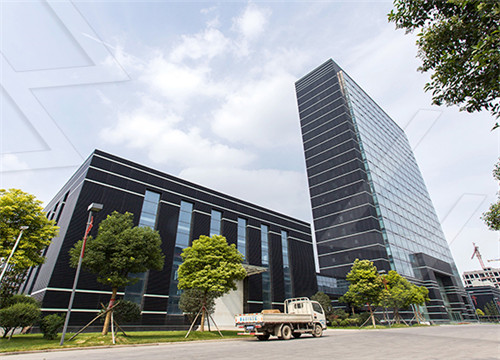
FR SUHFLSLWDWLRQ Institute of Physics
contained in iron ore and characterization using XRD to see crystal structure as well as the grain size of the iron ore. 3. Results and Discussion By using this method of analysis is conducted to sample iron ore magnetic separation process (magnetic separation) iron ore samples and conducted chemical separation process (method of precipitation).
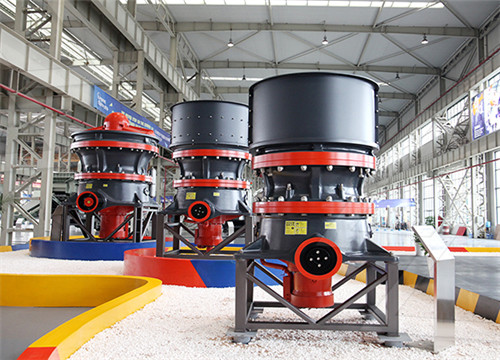
Separation and purification of high-purity quartz from high
2023年1月1日The iron ore tailing sample was a granular high-silicon solid waste obtained after the beneficiation process of iron ore following the steps of stage grinding–gravity separation–magnetic separation–anion reverse flotation. The sample had a size distribution ranging from 0.42 to 831.76 µm.
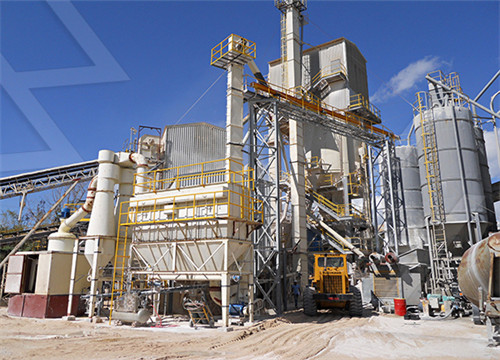
Magnetic Separator an overview ScienceDirect Topics
9.5.2 Utilization of subeconomic iron ores As magnetic separators progress toward larger capacity, higher efficiency, and lower operating costs, some subeconomic iron ores have been utilized in recent years.
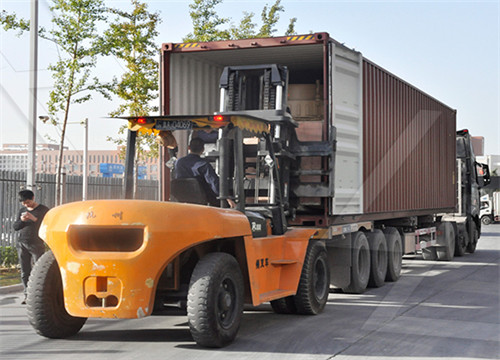
Increasing efficiency of iron ore magnetic separation by
enhance efficiency of iron ore magnetic separation by applying ultrasonic technologies. Thus, it is required to combine research results in the following directions: theoretical and practical research into iron ore magnetic separation; methods and means of operative control over physical-mechanical and chemical-
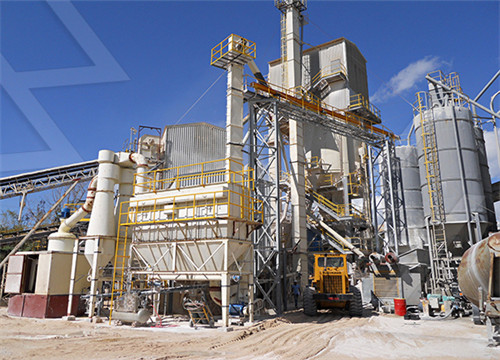
A Beneficiation Study on a Low Grade Iron Ore by Gravity and Magnetic
2018年8月25日In this , a sample from Tange-zagh iron mine was characterized by gravity and magnetic separation methods. The mineralogical studies showed that hematite and goethite are the main iron-bearing minerals with insignificant amounts of FeO. The results indicated that spiral separation yields higher separation efficiency than others.
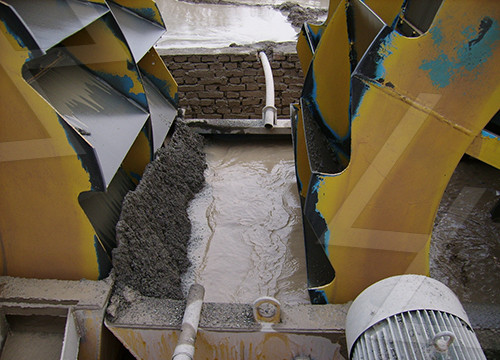
ADVANCES IN MAGNETIC SEPARATION OF ORES
magnetic separation. Dry Magnetic Separation of Iron Ore: There are many inherent advantages in processes that utilize dry magnetic separation to beneficiate iron ore. Wet concentration of magnetite ore, in comparison, re- quires 500 to 1000 gal of water per ton of concen- trate produced. This means extensive use of water
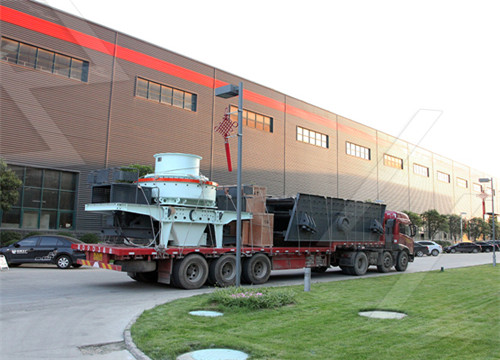
Dry Magnetic Separation of Iron Ore of the Bakchar
2015年12月31日Magnetic separation has been applied in ore processing to separate magnetic materials, such as iron oxides, from the bulk of nonmagnetic minerals with smaller specific densities [8]. This...
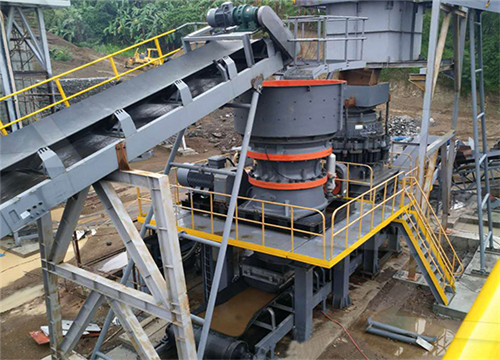
Discrete Event Simulation of an Iron Ore Milling Process
grinding machines along with the classifiers and magnetic separators and simulate the combination in a magnetite plant. 3. System definition . In this study, a whole processing plant simulation modeling approach is followed. The study focuses on modeling an iron ore magnetic separation processing plant in Arena discrete event

Super iron ore concentrate preparation equipment and production process
The invention relates to a super iron ore concentrate preparation equipment and production process adopting pre-grading magnetic separation. The equipment at least comprises a rough concentration unitand a fine concentration unit which are connected with each other. The equipment further comprises a screening unit, wherein the sizes of screening holes
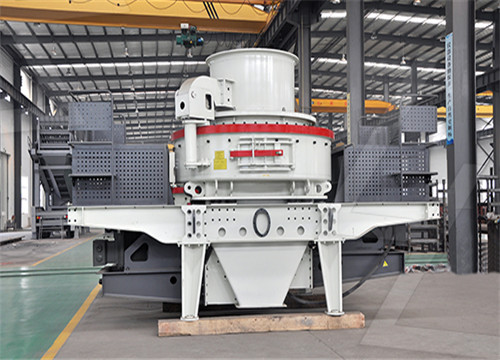
Open Access proceedings Journal of Physics: Conference series
2022年8月25日The mineral composition of iron ore after separation process, generated by X-ray fluorescence (XRF) as seen in Table 1, indicated that the magnetite (Fe2O3) is dominated by 86.55%, since the it shows that mineral composition iron ore by magnetic separation contains Fe2O3 of 86.81% in purity and followed by some minor

BENEFICIATION OF IRON ORE National Institute of
The jigging process produces iron ore concentrate (-10mm) with Fe>64% and Al2O3 = 2.25%, Jig tailings and slimes. Classifier fine ore is conveyed by Belt conveyor to Jig Bins, gravity separation, magnetic separation, and bio beneficiation can be used for the up gradation of iron ore slimes in India. The enhanced low alumina ore can then be
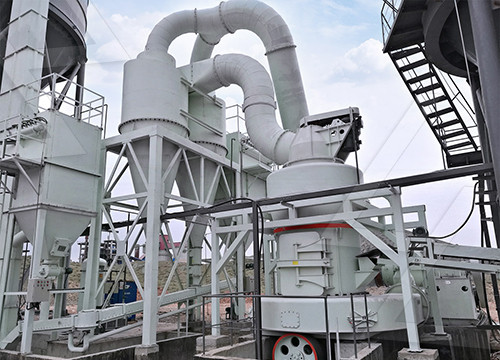
(PDF) Wet High Intensity Magnetic Separation of Iron Minerals
1996年1月1日The Series L Model 4 (L-4 machine) (Eriez Manufacturing Co.) was used for magnetic separation of the ore samples. The L-4 machine uses wire mesh or pipe matrix fixed inside the casing as magnetic
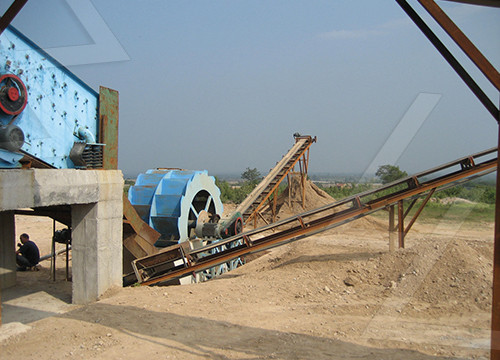
Iron Extraction From Oolitic Iron Ore by a Deep Reduction Process
2011年8月1日A laboratory experiment was carried out to extract iron from oolitic iron ore by a deep reduction and magnetic separation technique. The raw coal with fixed carbon of 66.54% was used as the reductant. The iron was successfully extracted from the oolitic iron ore which otherwise is nearly impossible to be separated due to its extremely fine-grain

Open Access proceedings Journal of Physics: Conference series
2022年8月25日The mineral composition of iron ore after separation process, generated by X-ray fluorescence (XRF) as seen in Table 1, indicated that the magnetite (Fe2O3) is dominated by 86.55%, since the it shows that mineral composition iron ore by magnetic separation contains Fe2O3 of 86.81% in purity and followed by some minor
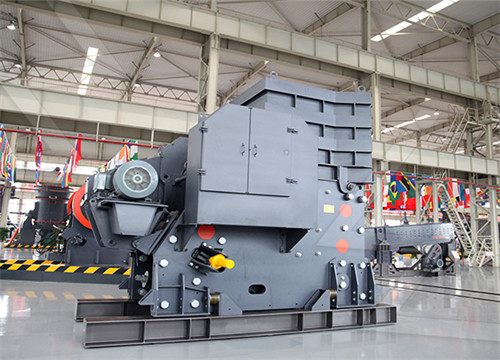
FR SUHFLSLWDWLRQ Institute of Physics
contained in iron ore and characterization using XRD to see crystal structure as well as the grain size of the iron ore. 3. Results and Discussion By using this method of analysis is conducted to sample iron ore magnetic separation process (magnetic separation) iron ore samples and conducted chemical separation process (method of precipitation).
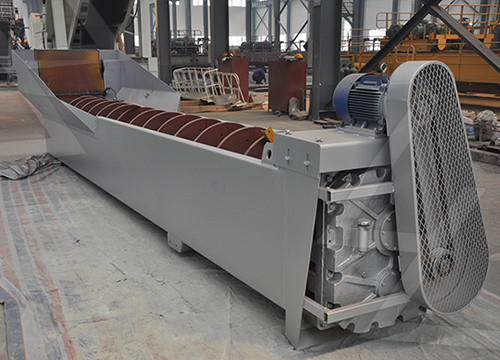
Separation and purification of high-purity quartz from high
2023年1月1日The iron ore tailing sample was a granular high-silicon solid waste obtained after the beneficiation process of iron ore following the steps of stage grinding–gravity separation–magnetic separation–anion reverse flotation. The sample had a size distribution ranging from 0.42 to 831.76 µm.
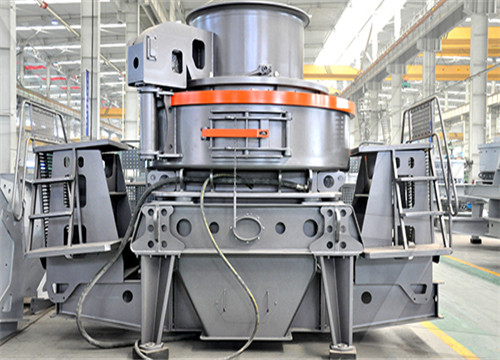
Magnetic Separator an overview ScienceDirect Topics
9.5.2 Utilization of subeconomic iron ores As magnetic separators progress toward larger capacity, higher efficiency, and lower operating costs, some subeconomic iron ores have been utilized in recent years.
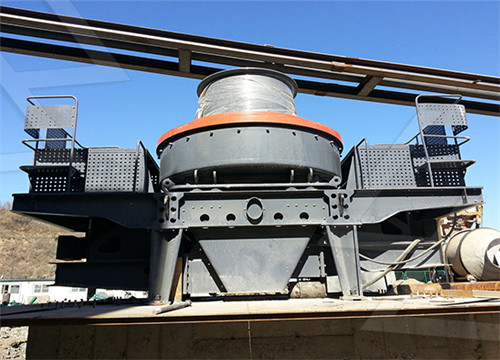
Increasing efficiency of iron ore magnetic separation by
enhance efficiency of iron ore magnetic separation by applying ultrasonic technologies. Thus, it is required to combine research results in the following directions: theoretical and practical research into iron ore magnetic separation; methods and means of operative control over physical-mechanical and chemical-

Iron Extraction From Oolitic Iron Ore by a Deep Reduction Process
2011年8月1日A laboratory experiment was carried out to extract iron from oolitic iron ore by a deep reduction and magnetic separation technique. The raw coal with fixed carbon of 66.54% was used as the reductant. The iron was successfully extracted from the oolitic iron ore which otherwise is nearly impossible to be separated due to its extremely fine-grain
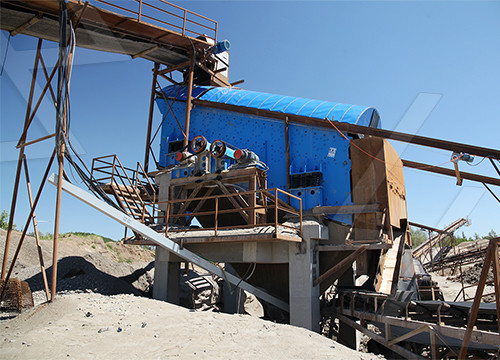
Dry Magnetic Separation of Iron Ore of the Bakchar
2015年12月31日Magnetic separation has been applied in ore processing to separate magnetic materials, such as iron oxides, from the bulk of nonmagnetic minerals with smaller specific densities [8]. This...
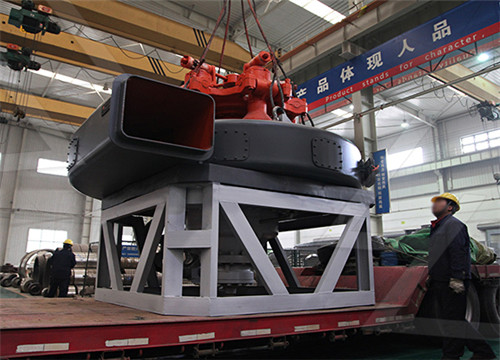
Mechanism of improved magnetizing roasting of siderite–hematite iron
2019年3月12日A fluidized-bed magnetizing roasting–magnetic separation process was selected to treat this type of material. Phase transformations and microstructural changes in the product resulting from magnetizing roasting under different reducing gases (CO, H 2, CO + H 2) were clarified by vibrating sample magnetometry, X-ray diffraction, scanning
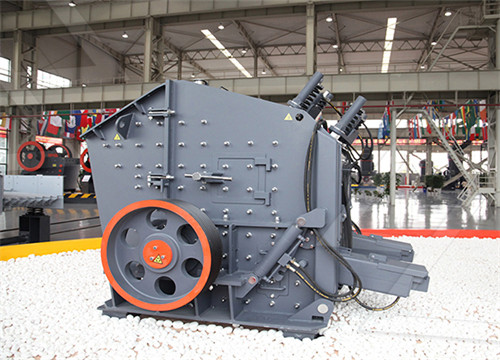
Super iron ore concentrate preparation equipment and production process
The invention relates to a super iron ore concentrate preparation equipment and production process adopting pre-grading magnetic separation. The equipment at least comprises a rough concentration unitand a fine concentration unit which are connected with each other. The equipment further comprises a screening unit, wherein the sizes of screening holes
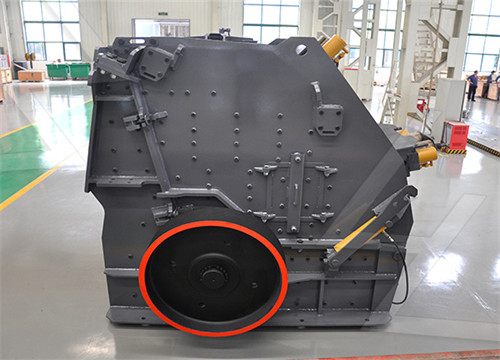
(PDF) Wet High Intensity Magnetic Separation of
1996年1月1日The Series L Model 4 (L-4 machine) (Eriez Manufacturing Co.) was used for magnetic separation of the ore samples. The L-4 machine uses wire mesh or pipe matrix fixed inside the casing as
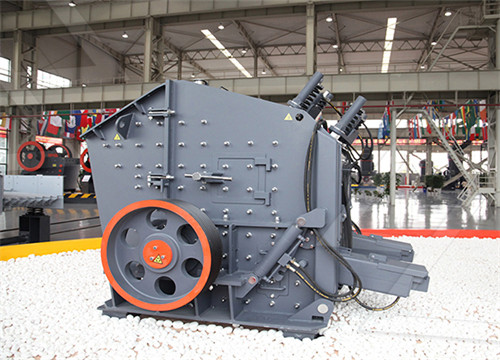
BENEFICIATION OF IRON ORE National Institute of
The jigging process produces iron ore concentrate (-10mm) with Fe>64% and Al2O3 = 2.25%, Jig tailings and slimes. Classifier fine ore is conveyed by Belt conveyor to Jig Bins, gravity separation, magnetic separation, and bio beneficiation can be used for the up gradation of iron ore slimes in India. The enhanced low alumina ore can then be
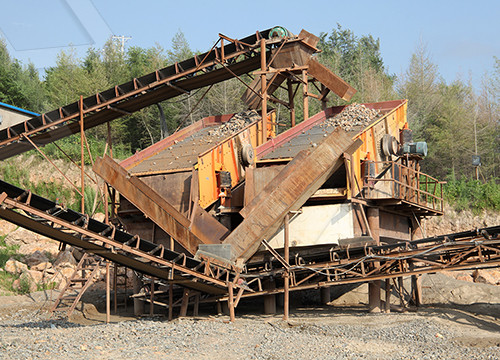
Process for recovering iron and rare earth in baotite low-intensity
2013年8月27日The invention belongs to the technical field of mineral engineering and aims at providing a process for recovering iron and rare earth in baotite low-intensity magnetic separation tailings. Iron content in the tailings in the existing technological process of a bayan obo iron mine is about 13% ordinarily, dissemination particles of
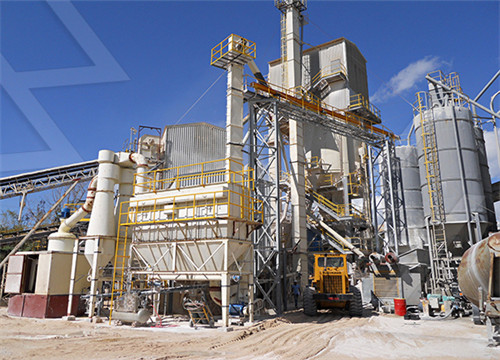
Pilot-scale extraction of iron from flotation tailings via suspension
2021年9月1日@article{Tang2021PilotscaleEO, title={Pilot-scale extraction of iron from flotation tailings via suspension magnetization roasting in a mixture of CO and H2 followed by magnetic separation}, author={Zhidong Tang and Qi Zhang and Yong-sheng Sun and Peng Gao and Yuexin Han}, journal={Resources Conservation and Recycling},